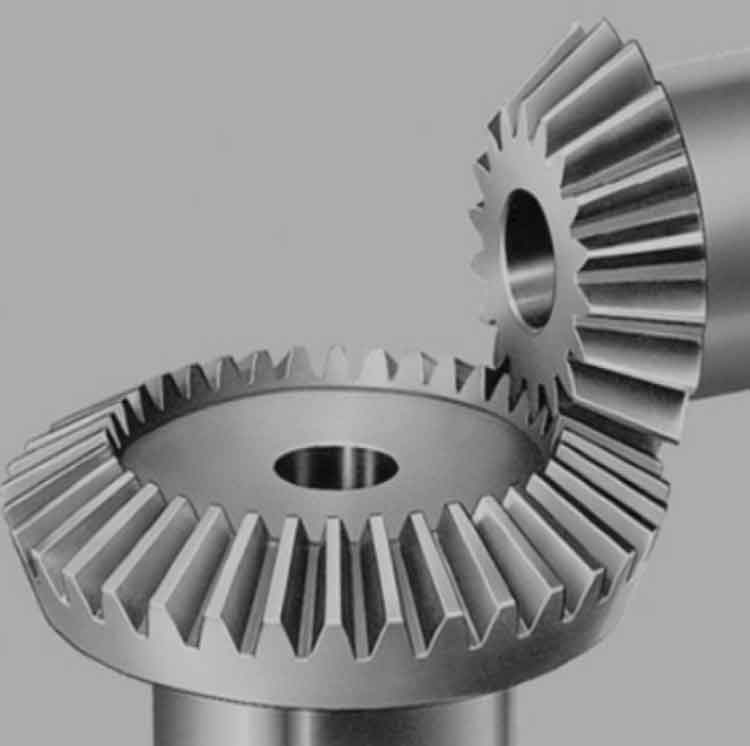
Case Study 1: Mining Equipment Gearbox Optimization
Challenge: A mining equipment manufacturer faced challenges with the gearbox of their excavators, which experienced frequent breakdowns due to high loads, extreme operating conditions, and uneven power distribution among the gears.
Solution: Engineers analyzed the gearbox design and proposed an optimized configuration using straight bevel gears. They adjusted the gear tooth profile and improved the gear meshing to ensure better load distribution. Additionally, they utilized advanced materials and heat treatment processes to enhance gear strength and wear resistance.
Result: The optimized gearbox with straight bevel gears significantly improved the overall performance and durability of the excavators. The new design reduced maintenance downtime and increased the mean time between failures, leading to higher productivity and cost savings for the mining company.
Case Study 2: Agricultural Machinery Transmission Optimization
Challenge: An agricultural machinery manufacturer faced challenges with the transmission system of their tractors, particularly regarding gear noise, efficiency, and power delivery.
Solution: Engineers analyzed the existing transmission system and proposed an optimized gearbox using straight bevel gears. They implemented tooth modifications to reduce noise and vibration. Additionally, they improved the gear quality and precision manufacturing to enhance gear efficiency.
Result: The optimized transmission system with straight bevel gears led to quieter operation and improved overall efficiency of the tractors. The gear noise was significantly reduced, enhancing the comfort of the operators. Moreover, the improved efficiency resulted in fuel savings and increased tractor performance.
Case Study 3: Marine Propulsion Gearbox Redesign
Challenge: A shipbuilding company faced challenges with the propulsion gearbox of their vessels, experiencing excessive wear and tear, and high maintenance costs.
Solution: Engineers redesigned the propulsion gearbox using straight bevel gears with advanced surface coatings for increased wear resistance. They optimized the gear contact patterns and load distribution to ensure uniform power transmission.
Result: The redesigned propulsion gearbox with straight bevel gears exhibited enhanced durability and reduced maintenance requirements. The use of advanced coatings significantly extended the gear life, resulting in cost savings for the shipbuilding company.
Case Study 4: Industrial Gear Unit Optimization
Challenge: A manufacturer of industrial machinery faced challenges with the gear unit of their equipment, including low gear efficiency and high noise levels.
Solution: Engineers optimized the gear unit using straight bevel gears with improved tooth geometry and gear meshing. They used computer simulations to analyze the gear contact patterns and optimize the gear design for higher efficiency.
Result: The optimized gear unit with straight bevel gears achieved higher efficiency and lower noise levels, leading to improved performance and reduced operating costs for the industrial machinery.
These case studies demonstrate the successful application of straight bevel gears in various industries, including mining, agriculture, marine, and industrial machinery. Gear design optimization using straight bevel gears can lead to enhanced performance, improved durability, and cost savings, making them an excellent choice for numerous applications.