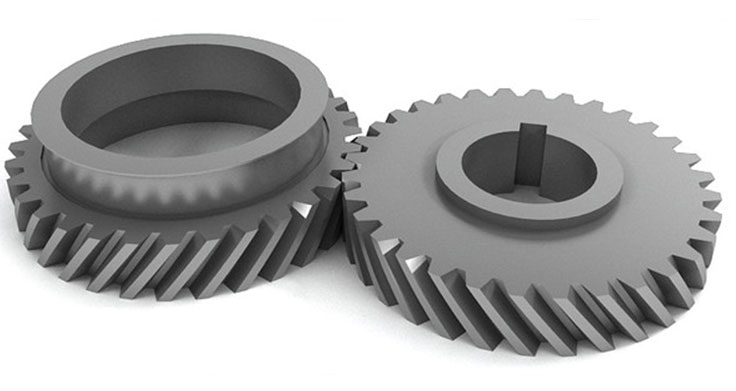
Advancements in helical gear technology have been driving gear system evolution, leading to improved performance, efficiency, and reliability in various industries. Some key innovations and advancements that have contributed to the evolution of helical gear systems include:
1. Advanced Materials and Heat Treatment:
- The use of high-performance materials, such as alloy steels and advanced composites, has increased the load-carrying capacity and durability of helical gears. Additionally, advancements in heat treatment techniques have allowed for precise control of material properties, resulting in stronger and more wear-resistant gears.
2. Precision Gear Manufacturing:
- Modern manufacturing technologies, such as CNC machining and gear grinding, have enhanced the precision of helical gear manufacturing. This improved accuracy ensures smoother gear tooth profiles, leading to reduced noise and improved gear meshing efficiency.
3. Computer-Aided Gear Design:
- Computer-aided design (CAD) and simulation software have revolutionized gear design. Engineers can now optimize gear tooth profiles, helix angles, and microgeometry using sophisticated algorithms, leading to higher gear efficiency and performance.
4. Tooth Surface Coatings:
- The application of advanced surface coatings, such as diamond-like carbon (DLC) and other low-friction coatings, has reduced friction and wear on gear teeth. These coatings improve gear efficiency and prolong gear life in demanding applications.
5. Microgeometry Modifications:
- Innovations in microgeometry modifications, such as tooth crowning and flank modifications, have allowed engineers to tailor gear tooth contact patterns for specific applications. These modifications optimize load distribution, reduce noise, and increase gear efficiency.
6. Noise and Vibration Reduction:
- Advancements in gear tooth profile design and surface finishing techniques have contributed to significant noise and vibration reduction in helical gear systems. This has made helical gears more suitable for applications where quiet operation is essential.
7. Lubrication and Cooling Techniques:
- Improved lubrication and cooling strategies have been developed to optimize gear performance and reduce heat generation. Proper lubrication and cooling ensure smooth gear operation and prevent premature wear.
8. Integration with Smart Technologies:
- Helical gears are being integrated with smart technologies, such as condition monitoring and predictive maintenance systems. These innovations allow for real-time gear health monitoring, early fault detection, and improved gear system reliability.
9. Miniaturization and Lightweight Design:
- Innovations in gear design and manufacturing have allowed for miniaturization of helical gears without sacrificing performance. These lightweight and compact helical gears are suitable for applications with limited space and weight constraints.
10. Hybrid Gear Systems:
- Hybrid gear systems, which combine helical gears with other gear types or technologies, are being explored to maximize gear system efficiency and performance for specific applications.
These advancements in helical gear technology have led to more reliable, efficient, and versatile gear systems in industries such as automotive, aerospace, robotics, industrial machinery, and renewable energy. As gear technology continues to evolve, helical gears will remain at the forefront, driving further innovations in gear system design and performance optimization.