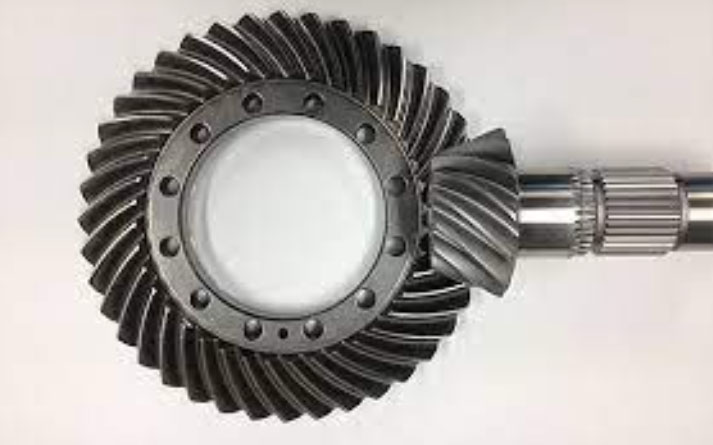
Advancements in hypoid gear technology have contributed to significant improvements in efficiency and reliability, making them even more suitable for various applications. Here are some key advancements in hypoid gear technology:
- Gear Design Optimization: Advanced computer-aided design (CAD) tools and simulation techniques have enabled more precise and optimized hypoid gear designs. Engineers can now analyze various parameters, such as tooth profile, tooth contact pattern, and gear geometry, to optimize gear performance. This results in improved efficiency, reduced noise and vibration, and enhanced gear life.
- Manufacturing Techniques: Modern manufacturing methods, such as CNC machining, have improved the precision and consistency of hypoid gear production. Computer-controlled machines ensure high accuracy in gear tooth profiles, resulting in better tooth meshing and reduced power losses. Additionally, advanced gear cutting technologies, such as multi-axis machining and five-axis milling, enable more complex and precise gear manufacturing.
- Material Selection and Heat Treatment: The development of advanced materials, such as high-strength alloys and surface coatings, has enhanced the durability and reliability of hypoid gears. These materials offer improved wear resistance, fatigue strength, and heat dissipation properties, allowing the gears to handle higher loads and operate in demanding conditions. Additionally, advancements in heat treatment techniques, such as carburizing and nitriding, improve the surface hardness and case depth of the gears, further enhancing their performance and longevity.
- Lubrication and Gearbox Design: Innovations in lubrication technology have contributed to the efficient operation and reduced friction losses of hypoid gear systems. Advanced lubricants with superior film-forming and anti-wear properties minimize gear wear and optimize power transmission efficiency. Furthermore, advancements in gearbox design, including better sealing, improved cooling, and optimized gear arrangements, have resulted in reduced losses and improved overall system efficiency.
- Noise and Vibration Reduction: Noise and vibration reduction is a crucial aspect of hypoid gear advancements. Innovative techniques, such as tooth modification and surface finishing, help to minimize gear meshing noise and vibrations. Computer-based analysis and simulation tools allow engineers to fine-tune gear designs to achieve quieter operation. Additionally, the use of noise-damping materials and vibration isolation techniques in gearbox housing further contribute to noise reduction.
- Integrated Monitoring and Control Systems: The integration of advanced monitoring and control systems in hypoid gear applications has improved reliability and maintenance practices. Real-time monitoring of gear performance parameters, such as temperature, vibration, and load, allows for proactive maintenance and helps prevent unexpected failures. Furthermore, the implementation of predictive maintenance strategies based on data analysis and condition monitoring optimizes gear reliability and reduces downtime.
These advancements in hypoid gear technology have led to improved efficiency, reliability, and overall performance in various applications, including automotive drivetrains, industrial machinery, aerospace systems, and more. By leveraging these advancements, engineers can design and manufacture hypoid gears that meet the ever-increasing demands for efficiency, durability, and reliability in power transmission systems.