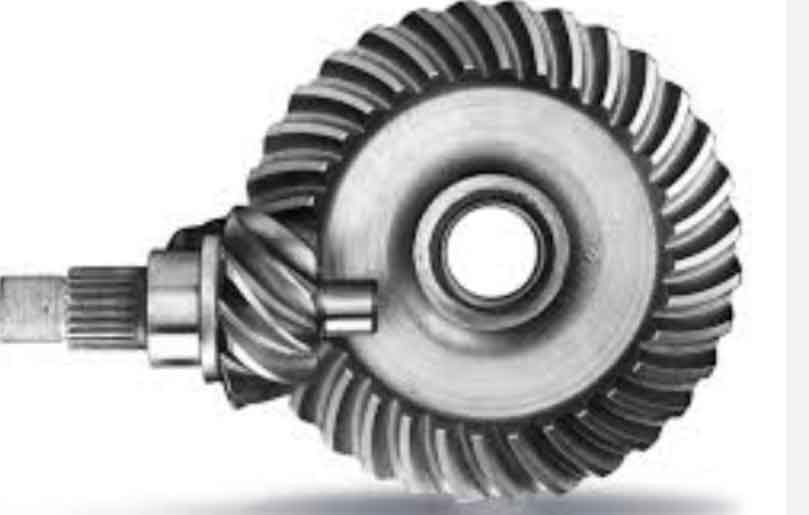
The manufacturing process of hypoid gears involves several steps, from initial design to final production. Here’s an overview of the typical manufacturing process for hypoid gears:
- Design and Engineering:
- The process begins with the design and engineering of the hypoid gears using specialized software and CAD (Computer-Aided Design) tools.
- The gear geometry, tooth profile, gear ratio, and other specifications are determined based on the application requirements.
- Gear Cutting:
- The first step in manufacturing hypoid gears is gear cutting, which involves creating the gear teeth.
- Gear cutting can be done using several methods, including face milling, face hobbing, and face grinding.
- Hypoid gears require specialized cutting machines capable of generating the unique tooth geometry.
- Heat Treatment:
- After gear cutting, the hypoid gears undergo heat treatment to enhance their mechanical properties.
- Heat treatment processes, such as carburizing or nitriding, are used to harden the gear surface and improve wear resistance.
- Gear Finishing:
- Once heat-treated, the gears undergo finishing processes to achieve the desired surface finish and tooth accuracy.
- Gear grinding and lapping are commonly used to improve the tooth profile and reduce surface roughness.
- Inspection and Quality Control:
- Throughout the manufacturing process, various inspections and quality control measures are implemented to ensure the gear’s dimensional accuracy and quality.
- Coordinate measuring machines (CMMs) and gear measuring instruments are used to verify the gear’s dimensional and functional characteristics.
- Assembly:
- In certain applications, hypoid gears are assembled with other components to form a complete gear system.
- This can involve aligning the gears, adjusting backlash, and ensuring proper gear meshing.
- Testing and Validation:
- Before the gears are ready for commercial use, they undergo testing and validation to ensure they meet the required performance standards.
- This may include tests for load capacity, noise levels, durability, and efficiency.
- Final Production and Packaging:
- Once the gears pass all the required tests, they are ready for final production and packaging.
- The gears are typically cleaned, inspected once again, and packaged for shipping to customers.
It’s important to note that the manufacturing process for hypoid gears may vary depending on the specific gear design, production methods employed by the manufacturer, and the level of customization required for the application.
Manufacturing hypoid gears requires specialized machinery, expertise in gear design and manufacturing, and strict quality control processes to ensure the gears meet the required specifications. Therefore, it’s recommended to work with experienced gear manufacturers or gear specialists who have the knowledge and capabilities to produce high-quality hypoid gears.