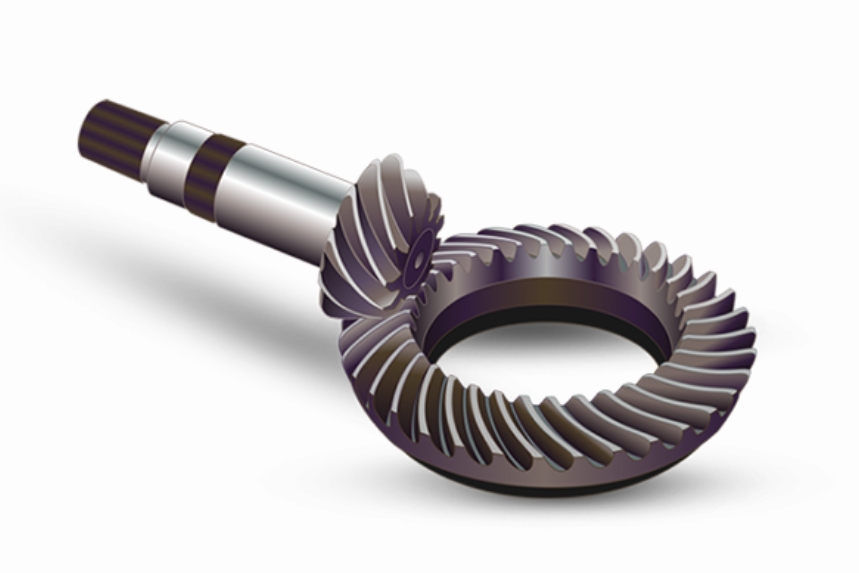
Advancements in machining technologies have significantly improved the precision, efficiency, and versatility of spiral bevel gear production. Spiral bevel gear is used in various industries for power transmission, particularly in applications where a change in the direction of rotation is required. Here are some key advancements in machining technologies for spiral bevel gear production:
1. Computer-Aided Design (CAD) and Simulation
- Virtual Modeling: CAD software allows for the precise design and simulation of spiral bevel gear, ensuring optimal tooth geometry and contact patterns.
- Finite Element Analysis (FEA): FEA is used to simulate gear meshing and analyze stress distribution, helping optimize gear designs for strength and durability.
2. CNC Machining
- High-Precision Machining: Computer Numerical Control (CNC) machines offer high precision in cutting spiral bevel gear teeth, ensuring accurate tooth profiles and surface finishes.
- 5-Axis Machining: 5-axis CNC machines enable simultaneous machining of complex gear geometries, reducing production time and improving accuracy.
3. Gear Cutting Technologies
- Gear Hobbing: Hobbing machines are used to cut spiral bevel gear teeth with high precision and efficiency.
- Gear Shaping: Shaping machines can also be used to cut spiral bevel gear teeth, offering flexibility in gear production.
4. Gear Grinding
- Precision Grinding: Gear grinding processes, such as generating grinding and form grinding, are used to achieve high precision in tooth profiles and surface finishes.
- Continuous Generating Grinding: This method allows for high-speed and high-precision production of spiral bevel gear with improved surface quality.
5. Laser Machining
- Laser Cutting: Laser cutting is used for precise cutting of spiral bevel gear blanks and for creating features like keyways and splines with high accuracy.
- Laser Hardening: Laser hardening is employed to selectively harden gear tooth surfaces, improving wear resistance and durability.
6. Advanced Cutting Tools
- Carbide Tools: High-performance carbide cutting tools are used for machining spiral bevel gears, offering superior wear resistance and cutting performance.
- Coated Tools: Coatings like TiN, TiAlN, and DLC are applied to cutting tools to enhance their wear resistance and tool life.
7. Process Optimization
- Simulation Software: Advanced software tools are used to simulate gear cutting processes and optimize tool paths for improved efficiency and reduced production time.
- In-Process Monitoring: Real-time monitoring of machining processes allows for adjustments to be made to optimize performance and ensure quality.
These advancements in machining technologies have enabled manufacturers to produce spiral bevel gear with higher precision, efficiency, and durability, meeting the stringent requirements of modern industrial applications.