Spur gear is one of the simplest and most commonly used types of gears in various mechanical systems, from clocks to high-powered engines. Understanding the mechanics of spur gear involves exploring their design principles, operational dynamics, and practical applications. Here’s a detailed overview:
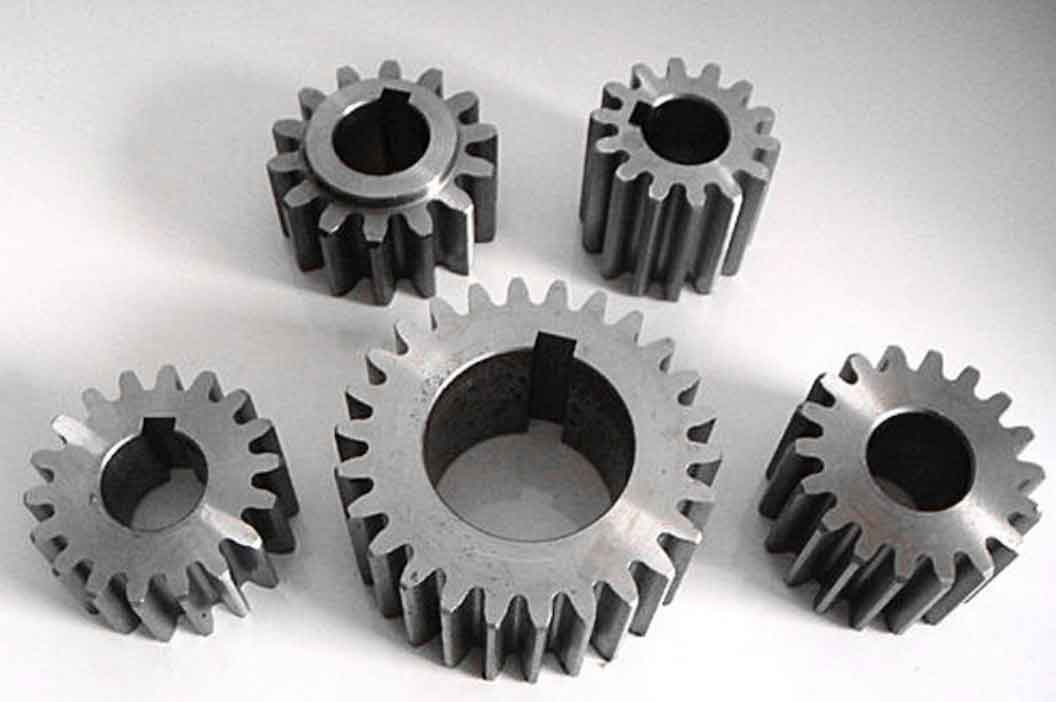
Basic Principles of Spur Gear Mechanics
1. Design and Geometry
- Tooth Profile: The most common profile for the teeth of spur gear is the involute curve. This profile provides constant velocity ratio and smooth operation because it ensures that the force acts along a single line of action, minimizing losses due to friction and slippage.
- Pitch Circle: The pitch circle is an imaginary circle that passes through the point where the teeth of two gear effectively mesh. It’s crucial for determining the size and spacing of the teeth.
- Module: This is a measure of the size of the teeth in relation to the pitch circle diameter. It is defined as the ratio of the pitch diameter to the number of teeth. The module system simplifies the design and interchangeability of spur gear.
2. Gear Ratio
- Definition: Spur gear ratio is the ratio of the number of teeth on the driven gear to the number of teeth on the driving gear. It determines how the speed and torque are altered between the input and output spur gears.
- Impact on Performance: The higher gear ratio reduces speed and increases torque, while a lower gear ratio increases speed and reduces torque, crucial for adapting spur gear system to different mechanical needs.
3. Contact Ratio
- Explanation: The contact ratio is the average number of teeth in contact between the driving and driven spur gear. Higher contact ratios lead to smoother and quieter operation.
- Enhancements: It can be improved by increasing the face width or modifying the tooth height and geometry.
Operational Dynamics
1. Load Distribution
- Gears need to be designed to distribute loads evenly across the tooth surfaces. Uneven load distribution can lead to premature wear and gear failure.
2. Stress and Strain
- The stresses on spur gear teeth include bending stress at the tooth root and contact stress on the tooth surface. Proper material selection and heat treatment can help manage these stresses.
3. Efficiency
- Spur gear is highly efficient, with efficiencies ranging from 95% to 99%. The efficiency is mainly lost due to friction between the meshing teeth and any resulting heat generation.
Practical Applications
1. Automotive
- In automotive transmissions, spur gear is used in sequences to achieve various gear ratios, helping to adjust the torque and speed sent to the drive shaft.
2. Industrial Machinery
- Spur gear is prevalent in conveyor systems, pumping systems, and other machinery where straightforward, reliable power transmission is necessary.
3. Consumer Electronics
- In devices like printers and digital cameras, small spur gear play essential roles in ensuring precise movements and operations.
4. Robotics
- Spur gear is used extensively in robots for precise control over limb movements and other operational mechanisms due to their simplicity and reliability.
Conclusion
Spur gears are a fundamental element in mechanical engineering, valued for their simplicity, reliability, and efficiency. Their design principles ensure that they can be adapted to a wide range of applications, making them indispensable in both everyday devices and complex machinery. Understanding these mechanics not only aids in designing more effective gear systems but also in diagnosing and resolving issues in existing applications.