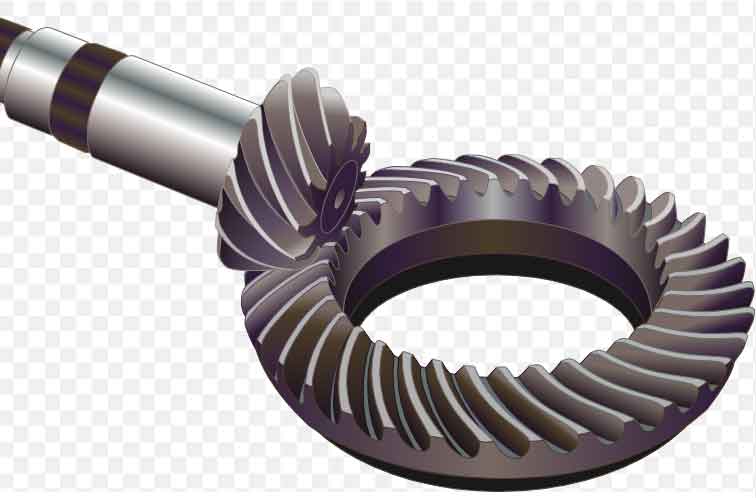
Advancements in spiral bevel gear technology have been instrumental in driving innovation across various engineering fields. As engineers and manufacturers continue to push the boundaries of gear design and manufacturing, several key advancements have emerged, contributing to improved performance, efficiency, and reliability. Here are some notable advancements in spiral bevel gear technology:
1. Computer-Aided Design (CAD) and Simulation:
The widespread adoption of CAD software and advanced simulation tools has revolutionized the gear design process. Engineers can now create complex 3D models of spiral bevel gears, analyze their performance under various loads and conditions, and optimize gear designs for specific applications. CAD and simulation enable faster prototyping, reduce development time, and lead to more reliable gear systems.
2. Advanced Manufacturing Techniques:
Modern manufacturing techniques, such as CNC machining, 5-axis milling, and high-precision gear grinding, have significantly improved the quality and precision of spiral bevel gears. These techniques allow for tight tolerances, improved surface finishes, and consistent tooth profiles, enhancing gear performance and efficiency.
3. Skiving and Scudding:
Skiving and scudding are advanced gear cutting methods that allow for the production of high-precision spiral bevel gears with superior surface finish and reduced noise. These techniques enable the creation of complex tooth profiles and are particularly beneficial for gear sets used in demanding applications, such as aerospace and automotive differentials.
4. Material and Heat Treatment Advances:
Advancements in metallurgy and heat treatment processes have led to the development of new materials with enhanced strength, wear resistance, and durability. Advanced heat treatment techniques, like case hardening and nitriding, further improve the gear’s surface hardness and toughness, increasing their load-carrying capacity and longevity.
5. Tooth Profile Optimization:
Researchers and engineers continuously study and optimize the tooth profile of spiral bevel gears to achieve smoother meshing, reduce noise, and improve efficiency. Advanced tooth profile designs, such as modified Gleason and Klingelnberg forms, allow for better load distribution and reduced stress concentrations.
6. Coating and Surface Treatments:
The application of advanced coatings and surface treatments, such as PVD (Physical Vapor Deposition) coatings, DLC (Diamond-Like Carbon) coatings, and shot peening, enhances the wear resistance and fatigue life of spiral bevel gears. These treatments improve gear reliability and performance under challenging operating conditions.
7. Digital Manufacturing and Industry 4.0:
Integration of digital manufacturing technologies and Industry 4.0 concepts into gear production facilitates data-driven decision-making, real-time monitoring of manufacturing processes, and predictive maintenance. These advancements contribute to more efficient production, reduced downtime, and higher quality gears.
8. Noise and Vibration Analysis:
Sophisticated noise and vibration analysis tools enable engineers to optimize gear designs for reduced noise emissions and smoother operation. By identifying noise sources and their causes, engineers can develop strategies to minimize gear noise, making them more suitable for applications requiring quiet operation.
In conclusion, advancements in spiral bevel gear technology have opened new horizons for innovation in engineering. Through improved design, precision manufacturing, material advancements, and data-driven approaches, spiral bevel gears continue to play a pivotal role in various industries, including aerospace, automotive, robotics, and industrial applications. These advancements have enabled the development of more efficient, reliable, and high-performance gear systems that drive progress in modern engineering and technology.