Advancements in straight bevel gear design have been instrumental in pushing the boundaries of gear technology and improving the performance of various mechanical systems. Some of the key advancements include:
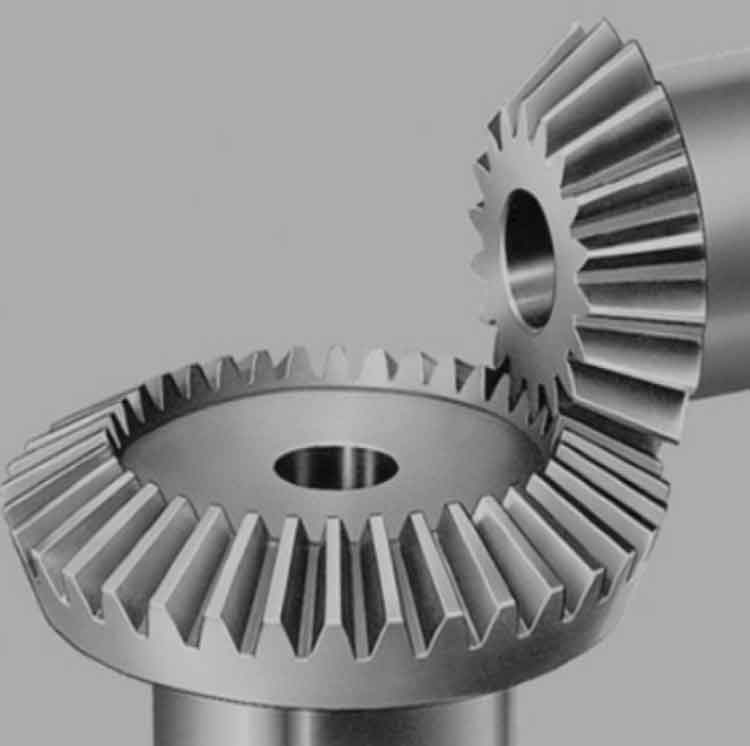
1. Computer-Aided Design (CAD) and Simulation:
The advent of powerful CAD software and simulation tools has revolutionized the design process. Engineers can now create and analyze intricate gear geometries, optimize tooth profiles, and simulate gear meshing behavior under different conditions. This has led to more efficient and precise straight bevel gear designs.
2. Advanced Manufacturing Techniques:
Innovations in manufacturing technologies, such as CNC machining and 5-axis milling machines, have enhanced the precision and repeatability of straight bevel gears. These advancements allow for the production of complex gear geometries with tight tolerances, improving gear performance and reducing noise.
3. Material Science and Heat Treatment:
Advancements in material science have led to the development of high-performance materials suitable for straight bevel gears. Heat treatment processes, such as carburizing and induction hardening, can improve the surface hardness and wear resistance of gears, increasing their durability and load-carrying capacity.
4. Surface Coatings and Finishing:
Advanced surface coatings and finishing techniques can further enhance the wear resistance and reduce friction in straight bevel gears. Coatings like diamond-like carbon (DLC) or nitriding improve the gear’s performance and extend its service life.
5. Tooth Profile Optimization:
Researchers continuously explore new tooth profiles and modifications to improve gear meshing and reduce noise. Optimization techniques, such as profile crowning and lead modifications, can minimize tooth contact stresses and improve gear efficiency.
6. Noise and Vibration Analysis:
Advancements in noise and vibration analysis tools have enabled engineers to identify and mitigate gear noise issues. Through careful analysis and design adjustments, noise levels in straight bevel gears can be significantly reduced.
7. Integrated Gearbox Design:
Modern gearbox design considers the overall system, including gear layout, housing structure, and lubrication, to optimize the performance of straight bevel gears in the context of the entire system. This integrated approach leads to more efficient and reliable gearboxes.
8. Industry 4.0 and Smart Manufacturing:
The integration of Industry 4.0 concepts, such as the Internet of Things (IoT) and real-time data analytics, has allowed for the monitoring and predictive maintenance of gear systems. This proactive approach helps prevent unexpected failures and improves the overall reliability of straight bevel gears.
9. Lightweight Materials and Design Optimization:
Advances in lightweight materials and design optimization techniques have enabled the development of compact and lightweight straight bevel gear systems. This is especially critical in industries such as aerospace and automotive, where weight reduction is a priority.
These advancements in straight bevel gear design have not only improved the efficiency and performance of gear systems but also expanded their applications to new and challenging environments. As technology continues to evolve, the future of straight bevel gears looks promising, with ongoing efforts to further optimize their design and manufacturing processes.