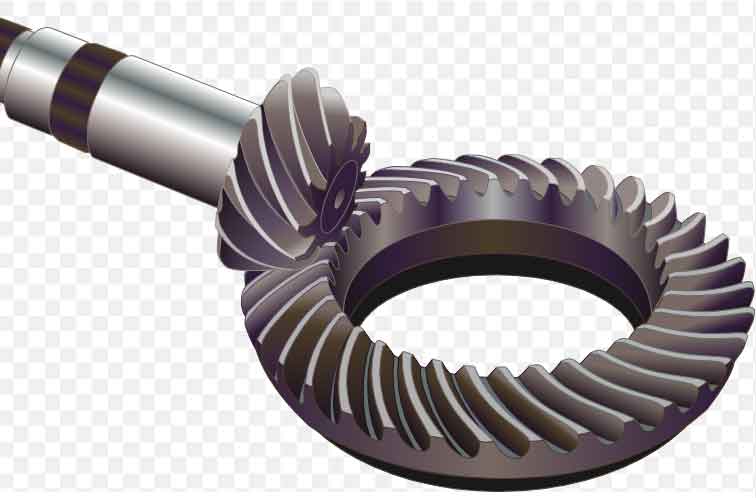
Precision engineering with spiral bevel gears involves meticulous attention to detail during the gear design and manufacturing processes to achieve high-quality gears with accurate tooth profiles and tight tolerances. Here are some design and manufacturing insights for precision engineering with spiral bevel gears:
Design Considerations:
1. Gear Geometry Optimization:
- Start with accurate gear geometry optimization using advanced gear design software. Consider factors such as the gear ratio, helix angle, number of teeth, and tooth thickness to meet the specific application requirements.
2. Tooth Profile Optimization:
- Optimize the tooth profile of the spiral bevel gears to achieve smooth and accurate tooth engagement. Tooth profile modifications, such as crowning and lead corrections, can be applied to improve contact patterns and reduce noise.
3. Material Selection:
- Choose high-quality materials with suitable mechanical properties, such as hardness and strength, to ensure the gears can withstand the expected loads and operating conditions.
4. Heat Treatment:
- Apply appropriate heat treatment processes to enhance the material properties of the gears, such as case hardening or carburizing, to improve wear resistance and fatigue strength.
5. Lubrication and Cooling:
- Design effective lubrication and cooling systems to ensure proper lubrication and heat dissipation during gear operation, preventing excessive wear and prolonging gear life.
6. Tolerance Analysis:
- Perform tolerance analysis to ensure that the gears meet the required dimensional and functional specifications. Tight tolerances are crucial for achieving precise gear meshing.
Manufacturing Techniques:
1. CNC Machining:
- Utilize advanced CNC machining techniques to achieve high precision in gear manufacturing. CNC machining ensures accurate gear tooth profiles and tight tolerances.
2. Gear Grinding:
- Implement gear grinding for high-precision finishing, ensuring accurate tooth geometry and surface quality. Grinding eliminates any errors introduced during earlier machining stages.
3. Gear Cutting and Shaping:
- Use gear cutting and shaping processes to rough out the gear teeth before finishing through gear grinding. This ensures that the gears are machined close to their final shape before the grinding process.
4. Inspection and Quality Control:
- Implement rigorous inspection and quality control procedures throughout the manufacturing process. Advanced measurement techniques, such as coordinate measuring machines (CMMs), are used to verify gear dimensions and tooth profiles.
5. Surface Treatments:
- Apply specialized surface treatments, such as shot peening or surface coatings, to enhance the gear’s surface hardness and improve wear resistance.
6. Gear Assembly:
- Precisely assemble the gears and ensure proper alignment to achieve smooth gear meshing and optimal performance.
Precision engineering with spiral bevel gears requires a combination of advanced design techniques, high-quality materials, and advanced manufacturing processes. Attention to detail at every stage, from gear design optimization to rigorous quality control, is essential to achieve gears with accurate tooth profiles, tight tolerances, and excellent performance. By following these design and manufacturing insights, engineers can ensure the production of high-precision spiral bevel gears suitable for critical applications in various industries.