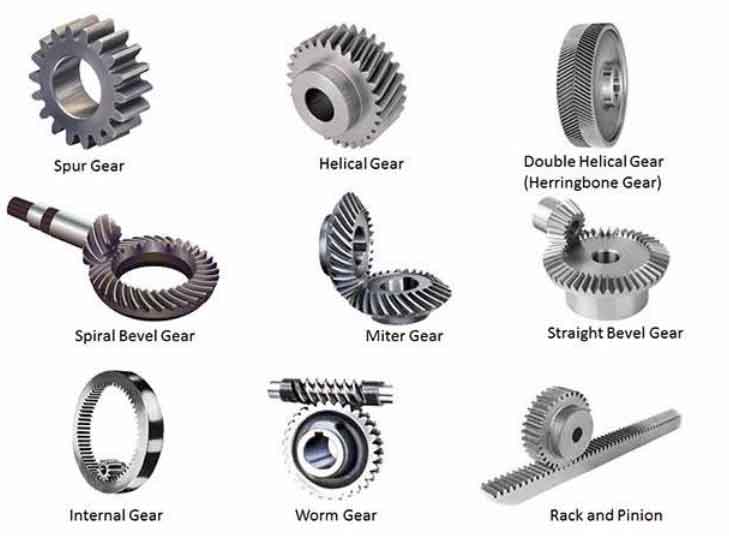
Spur gears are among the most common types of gears used in various mechanical systems due to their simplicity and effectiveness in transmitting power and motion. Here’s a detailed look at the advantages and disadvantages of spur gears, providing insight into their widespread use and limitations.
Advantages of Spur Gears
- Simplicity in Design and Manufacture: Spur gears have a straightforward design with teeth that are parallel to the axis of rotation. This simplicity makes them easier and more cost-effective to design and manufacture than more complex gear types.
- High Efficiency: Due to their simple geometry, spur gears are highly efficient in transmitting power. Their straight teeth mean there is less friction between the gear teeth, leading to higher efficiency rates, often above 95% for well-designed spur gear sets.
- Ease of Maintenance: The simple design of spur gears also makes them easier to maintain and inspect compared to gears with more complex shapes. This can lead to lower long-term maintenance costs.
- Versatility: Spur gears can be used in a wide range of applications, from simple mechanical devices to high-speed and high-load applications such as power plants and transport systems.
- High Load Capacity: When designed properly, spur gears can handle a significant amount of load. Their robustness makes them suitable for applications requiring the transmission of large forces.
- Precise Rotation Ratio: The design of spur gears allows for a very precise control of the rotation ratio between the driving and driven gears, which is crucial in many applications where timing and coordination are important.
Disadvantages of Spur Gears
- Noise and Vibration: One of the main drawbacks of spur gears is the noise generated, especially at high speeds. The direct engagement of the teeth causes sudden changes in force, leading to noise and vibrations.
- No Axial Load: Spur gears cannot handle axial loads due to the orientation of their teeth. This limits their use in applications where such forces are present.
- Limited Application in Non-Parallel Shafts: They are primarily used to transmit power between parallel shafts. For applications requiring the transmission of power between non-parallel shafts, other types of gears, like bevel or helical gears, are more appropriate.
- Stress Concentration: The direct engagement of the teeth can lead to stress concentrations at the tooth edges, which may result in tooth breakage or gear failure under heavy loads or improper material selection.
- Operational Limitations: While efficient, the design of spur gears means they are not the best choice for applications requiring quiet operation or the ability to handle high-speed loads with minimal vibration.
Spur gears offer a range of advantages, including simplicity, efficiency, and versatility, making them suitable for a wide variety of applications. However, the disadvantages, particularly regarding noise and vibration at high speeds, limit their use in certain scenarios. The choice to use spur gears depends on the specific requirements of the application, balancing factors such as cost, efficiency, noise levels, and operational demands.