Introduction
Gears play a crucial role in mechanical systems, transmitting power and motion between different components. Among the various types of gears, Spiral Bevel Gears are widely used in numerous applications due to their unique characteristics and superior performance. This article aims to provide a comprehensive understanding of Spiral Bevel Gears, including their characteristics, manufacturing processes, performance analysis, applications, maintenance, and research and development trends.
Characteristics of Spiral Bevel Gears
Spiral Bevel Gears are characterized by their spiral-shaped teeth, which are designed to provide smooth and efficient power transmission. The spiral angle of the teeth allows for gradual engagement, reducing shock and noise during operation. Compared to other types of gears, such as straight bevel gears, Spiral Bevel Gears offer several advantages. They have higher transmission efficiency, enabling more power to be transferred with less energy loss. Additionally, their smooth operation results in lower noise and vibration levels, making them suitable for applications where quiet performance is essential. Moreover, Spiral Bevel Gears can handle high loads and torque, making them reliable in demanding mechanical systems. However, they also present some challenges, such as complex manufacturing processes and high precision requirements, which can lead to increased costs.
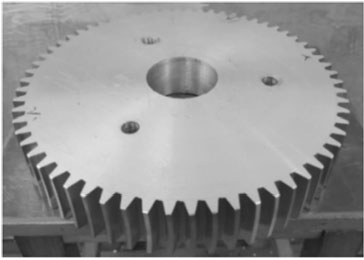
Manufacturing Processes of Spiral Bevel Gears
The manufacturing of Spiral Bevel Gears involves several intricate processes. Traditional manufacturing methods include gear cutting, such as milling, broaching, and hobbing, followed by grinding and finishing operations to achieve the desired surface finish and accuracy. These processes require skilled operators and precise machinery to ensure the quality of the gears. In recent years, advanced manufacturing technologies like Computer Numerical Control (CNC) machining have been adopted, which offers greater precision and flexibility in producing Spiral Bevel Gears. Additionally, 3D printing and additive manufacturing are emerging as potential techniques for gear production, although they are still in the development stage and have certain limitations. Quality control and inspection are critical steps in the manufacturing process to ensure that the gears meet the required standards. Metrology and measurement techniques are used to check the tooth profiles and dimensions, while non-destructive testing methods help detect any defects or cracks.
Performance Analysis of Spiral Bevel Gears
The performance of Spiral Bevel Gears is evaluated through various analyses, including meshing and contact analysis, transmission efficiency and power loss assessment, and noise and vibration characterization. Meshing and contact analysis focuses on the tooth contact patterns and stress distribution, which affects the load distribution and durability of the gears. Transmission efficiency is influenced by factors such as friction losses and load sharing between teeth, and efforts are made to improve efficiency through lubrication strategies and gear geometry optimizations. Noise and vibration are important considerations, as excessive noise and vibration can affect the performance and reliability of the mechanical system. Tooth modifications and profile optimization, as well as the use of damping materials and isolation techniques, can help reduce noise and vibration. Dynamic load analysis and fatigue life prediction are also essential to ensure the reliability and longevity of the gears.
Applications of Spiral Bevel Gears
Spiral Bevel Gears find extensive applications in various industries. In the automotive industry, they are used in transmission systems, including gearboxes and differentials, to transfer power from the engine to the wheels. They play a crucial role in improving vehicle performance and efficiency. In the aerospace industry, Spiral Bevel Gears are employed in aircraft engines and flight control systems, where high reliability and safety standards are required. In industrial machinery, such as mining equipment and manufacturing machines, they are used to handle heavy loads and operate in harsh environments. Additionally, they are used in robotics and automation for precise motion control, and in medical devices where reliability and accuracy are paramount. Case studies can illustrate the specific applications and success stories of Spiral Bevel Gears in different industries.
Maintenance and Inspection of Spiral Bevel Gears
Regular maintenance and inspection of Spiral Bevel Gears are essential to ensure their optimal performance and longevity. Preventive maintenance measures can help detect and address potential issues before they lead to failure or downtime. Inspection techniques include visual inspection for signs of wear and damage, measurement of tooth wear and clearance, and the use of non-destructive testing methods to detect cracks and defects. Monitoring performance parameters such as noise, vibration, and temperature can also provide valuable insights into the condition of the gears. Maintenance procedures involve proper lubrication, cleaning, and replacement of worn parts, as well as ensuring correct alignment and adjustment. Predictive maintenance and condition monitoring using sensors and data analysis are becoming increasingly important to implement proactive maintenance strategies.
Research and Development Trends in Spiral Bevel Gears
Ongoing research in the field of Spiral Bevel Gears focuses on several areas. Material innovations aim to develop high-strength and lightweight materials that can improve the fatigue resistance and durability of the gears. Design optimizations involve the use of advanced modeling and simulation techniques to explore new tooth geometries and configurations for enhanced performance. Surface treatments and coatings are being investigated to enhance the wear resistance and corrosion protection of the gears. Additionally, the integration of smart technologies, such as the Internet of Things (IoT) and sensor integration, is being explored to enable real-time monitoring and predictive maintenance. Looking towards the future, Spiral Bevel Gears are expected to play a significant role in emerging industries and technologies, contributing to sustainable development through improved energy efficiency and reduced emissions. Collaboration and innovation in the gear industry will continue to drive the development of more advanced and reliable Spiral Bevel Gears.
Case Studies
To further illustrate the practical applications and benefits of Spiral Bevel Gears, several case studies can be presented. These case studies can showcase specific projects or products where Spiral Bevel Gears have been successfully used, highlighting the challenges faced and the solutions implemented. Lessons learned from these case studies can provide valuable insights and best practices for the design, manufacturing, and maintenance of Spiral Bevel Gears.
Conclusion
In conclusion, Spiral Bevel Gears are essential components in various mechanical systems, offering superior performance and reliability. Their unique characteristics, combined with advancements in manufacturing and technology, make them a key element in many industries. Understanding their characteristics, manufacturing processes, performance analysis, applications, and maintenance is crucial for engineers and researchers to utilize them effectively. Continued research and development in this field will lead to further improvements and innovations in Spiral Bevel Gear technology, driving the progress of mechanical engineering.
Throughout this article, the term “Spiral Bevel Gear” has been repeatedly mentioned to emphasize its central role in the discussion. By delving into the details of Spiral Bevel Gears, we hope to provide a comprehensive and valuable resource for those interested in this important area of mechanical engineering.