(1) Comparison between simulation and experiment
Figure 1 compares the acceleration simulation and experimental results of pinion end with obvious tooth surface damage, in which dimensionless time is used for simulation and absolute time (s) is used for measured data.The direction acceleration of meshing line basically agrees with the simulation and experiment results, and there is obvious impact with a period of 4.17ms. The maximum acceleration is 30-40m/s2.The experimental results are basically in agreement with each other, with a period of 4.17ms and a maximum acceleration of 30-40m/s2.The experimental results are basically in agreement with each other, with a period of 4.17ms and a maximum acceleration of 30-40m/s2.The acceleration signal of friction direction, simulation and experiment results are also in good agreement, and the period is consistent with the direction of engagement line. Due to the continuous action of friction, the vibration attenuation on the engagement line is slow.At the same time, it is found that the X-direction acceleration experiment results are larger than the simulation values, which indicates that the roughness estimation of damaged tooth surface by simulation is smaller.
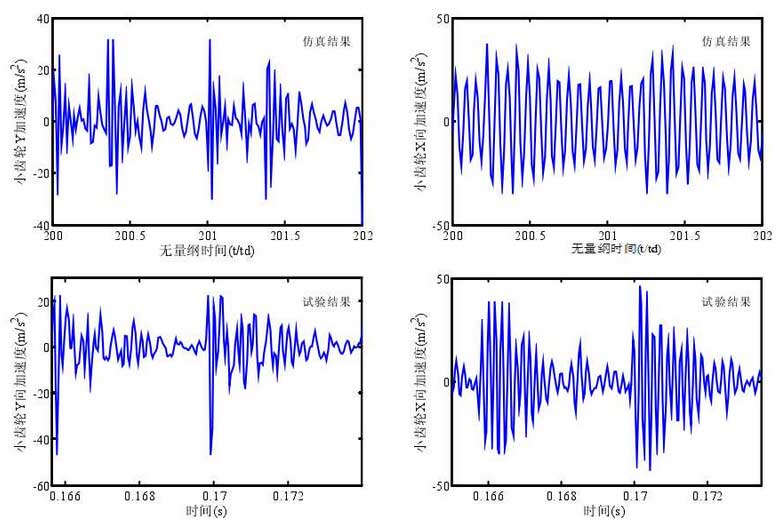
(2) Comparison of vibration characteristics
The acceleration of pinion bearing and case surface before and after tooth surface damage is compared and analyzed.
As shown in Figure 2, when obvious damage occurs to the tooth surface, the spectrum distribution of vibration acceleration in friction direction (X-direction) is basically the same as that of intact tooth surface. Frequency multiplication of engagement frequency is obvious. The maximum acceleration occurs at 5280Hz (22-order frequency multiplication of engagement frequency), while the amplitude increases by 2.6m/s2 (22-order frequency multiplication of engagement frequency), while the amplitude increases by 2.6m/s2 (engagement frequency).22-order frequency multiplication) and the amplitude is increased by 2.6m/s2. It can be seen that the tooth surface roughness directly affects the vibration intensity in the direction of meshing line.
In the direction of engagement line (Y), the vibration acceleration after increasing the tooth surface roughness decreases slightly (0.3m/s2) and the maximum amplitude before damage (0.3m/s2) decreases (0.3m/s2) and corresponds to the 10th and 9th order respectively.The results show that the micro-variation of tooth surface roughness has little effect on the vibration of the meshing line. Because the friction moment restrains the fluctuation of driving torque, increasing friction reduces the vibration of the meshing line to a certain extent, which is in accordance with the conclusions of simulation analysis.On the other hand, the increase of tooth surface roughness is conducive to the formation of oil film between teeth, which increases the meshing damping and suppresses the vibration on the meshing line.
The surface acceleration of the box reflects the combination of the direction of meshing line and the direction of friction force, as well as the influence of the inherent characteristics of the box.The frequency domain distribution of surface acceleration is basically the same before and after the change of tooth surface roughness. The engagement frequency of 5th, 10th and 15th order is obvious. At the same time, with the increase of roughness, the acceleration amplitude increases (maximum s/m (acceleration to X gear is 2) s/m (acceleration to Y gear is 2) 1.5m/s2) 1.5m/s2).It can be seen that the change of tooth surface roughness causes obvious change of vibration amplitude on the surface of the box. If combined with the vibration signals in X and Y directions, the change of tooth surface micro-morphology can be judged by the change of vibration amplitude.
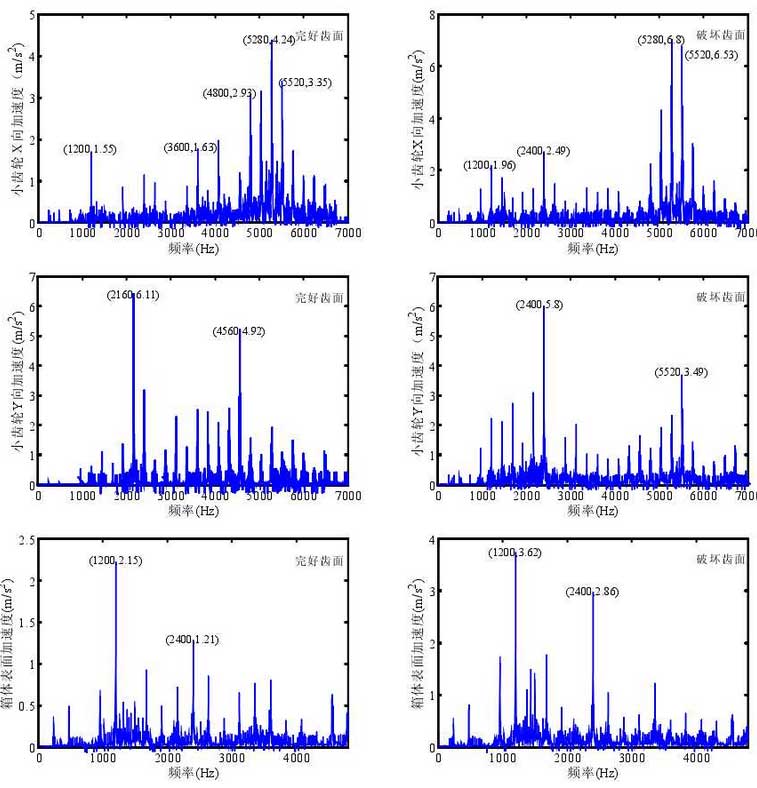