Cylindrical gear flowmeters are widely used in various fields due to their advantages such as small size, high precision, good stability, and wide range. However, the internal leakage phenomenon in cylindrical gear flowmeters is a problem that cannot be ignored. The leakage caused by the assembly clearance will make the actual measured flow rate smaller than the theoretical flow rate, which will affect the measurement performance of the flowmeter. Therefore, it is of great theoretical significance and application value to study the variation law of the measurement performance of the cylindrical gear flowmeter with the assembly clearance and reduce its influence by the assembly clearance.
1. Theoretical Basis
1.1 Working Principle of Cylindrical Gear Flowmeter
Inside the cylindrical gear flowmeter, there is a pair of cylindrical gears with circular cross-sections that mesh with each other. When the fluid enters from the inlet, the gears start to rotate under the action of the pressure difference at the inlet and outlet of the fluid. The gear teeth continuously divide the flowing liquid into multiple independent volume units and send them to the outlet. The total volume of the fluid discharged by the gears rotating one week is V, which can be calculated by the formula V = 2Nv, where N is the number of teeth of the gear.
There are three kinds of leakage in the cylindrical gear flowmeter, as shown in Figure 1. The leakage at the meshing point of the gears only accounts for about 5% of the total leakage flow, so this paper mainly analyzes the end face leakage and the radial leakage.
1.2 6-Degree-of-Freedom Model
During the normal working process, the gears in the cylindrical gear flowmeter rotate under the action of the pressure difference at the inlet and outlet, and the rotation process satisfies the equation of motion of the rigid body in the inertial system, as shown in Equation (2): L = I · ω, where L is the angular momentum, ω is the angular velocity of the rigid body in its own system, and I is the inertia tensor, which can be calculated by Equation (3): I = (I_x -I_xy -I_xz; -I_yx I_y -I_yz; -I_zx -I_zy I_z).
According to the theorem of momentum moment, dL/dt = T, where T is the resultant moment, including the driving moment and the resistance moment. When the force condition changes, the gear adjusts its motion state according to the motion equation. In the simulation process, the freedom of five directions of the gear in the cylindrical gear flowmeter can be limited by programming, and the moment of inertia in the rotation direction of the gear can be assigned. Under the set inlet flow velocity, the gear adjusts its rotation speed in real time according to the force condition. This study is based on this method to simulate the motion state of the gear in the cylindrical gear flowmeter and predict its metering performance.
2. Simulation Method
2.1 Simulation Model Establishment
The object of this study is the DN16 cylindrical gear flowmeter, and the experimental prototype is shown in Figure 2. The key dimensions of the experimental prototype were measured and the results are shown in Table 1. Referring to the experimental prototype, the flow channel was extracted using the 3D modeling software SolidWorks to draw the 3D model of the internal flow field of the flowmeter.
2.2 Mesh Generation
To facilitate the limitation of the total number of grids without affecting the flow field analysis at the key parts, the entire flow field was divided into five parts: inlet, upper end face clearance, lower end face clearance, gear and surrounding area, and outlet before meshing. Each flow field area and wall surface were named to set the boundary conditions and monitor the process parameters during the simulation. The 3D simulation model of the cylindrical gear flowmeter was imported into the PumpLinx software, and different grid generation modules were used to generate the grids for each area. To ensure the accuracy of the solution at the clearance, the grid division at the top clearance of the gear and the meshing clearance of the gear reached 18 layers, and the total number of grids in each area was 66w. The meshing result of the simulation flow field is shown in Figure 3.
2.3 Simulation Process
The initial conditions and boundary conditions for the simulation were set in PumpLinx, and the specific simulation process is shown in Figure 4.
2.4 Data Processing
During the simulation, the speed expression of the gear rotation was written through the compiler provided by PumpLinx to monitor the real-time rotation speed n_i of the gear. The speed expression is as follows: n = 60 / (2π) · ω. The average rotation speed n over one cycle was taken as the corresponding rotation speed value of the gear at this flow point, and the calculation process is shown in Equation (7): n = (n_1 + n_2 +… + n_n) / m, where m is the number of simulation steps in one cycle.
Using n – f, the simulated meter factor K of the cylindrical gear flowmeter at this flow point was calculated from the rotation frequency f of the gear and the instantaneous flow rate q_r, and the calculation process is shown in Equations (8) and (9): f = n · N / 60, K_s = 60f / q_s.
2.5 Reliability Verification of the Simulation Method
To verify the reliability of the simulation method, a real-flow test was carried out on the volume tube flow standard device of AVIC 304 Institute, and the system block diagram of the experimental device is shown in Figure 5. The measurement range of the device is (0.15 – 500) L/min, and the overall expanded uncertainty of the device is 0.05% (k = 2). During the experiment, the continuous adjustment of the system flow rate was achieved by adjusting the rotation speed of the servo motor and the proportional speed control valve, and the cumulative flow rate value in the volume tube was taken as the standard flow rate. The pulse signal of the measured flowmeter was collected and recorded by the signal acquisition device.
The experimental prototype was the DN16 cylindrical gear flowmeter mapped by simulation. According to the Verification Regulation of Liquid Positive Displacement Flowmeter JJG 667 – 2010, five flow points of 0.8, 20, 40, 60, and 80 L/min were determined, and the experiment was carried out under normal temperature conditions, and the test medium was YH – 15 aviation hydraulic oil.
During the experiment, each flow point was measured three times, and the meter factor of the cylindrical gear flowmeter was calculated by Equation (10), and then the average meter factor of the cylindrical gear flowmeter at this flow point was calculated by Equation (11). According to Equations (12) and (13), the average meter factor K and the linearity error E_L of the cylindrical gear flowmeter in the entire flow range were calculated. K_ij = N_ij / ((Q_s)ij) (i = 1, 2, 3, 4, 5; j = 1, 2, 3), K_i = 1/3 ∑(j = 1)^3 K_ij, K = 1/2 (K_imax + K_imin), E_L = (K_imax – K_imin) / (K_imax + K_imin) × 100%.
The experimental results were compared with the simulation results, as shown in Figure 6. It can be seen from Figure 6 that the simulation results and the experimental results have the same trend. When the flow rate is small, the meter factor of the cylindrical gear flowmeter is small, and as the flow rate increases, the meter factor gradually increases. To meet the simulation needs, the modeling and solving processes were idealized, so there is a certain deviation in the data between the simulation results and the experimental results, and the average meter factor differs by 8.8%, but the overall deviation is within the acceptable error range. Therefore, the simulation method based on the 6-degree-of-freedom model proposed in this paper is reliable and can be used to predict the performance of the cylindrical gear flowmeter.
3. Influence of Assembly Clearance on the Performance of Cylindrical Gear Flowmeter
3.1 Simulation Study on the Influence of Assembly Clearance
On the basis of the original model, the dimensions of the top circle and the end face clearance of the gear were changed, and the simulation method described above was used to simulate and analyze the cylindrical gear flowmeters with six different clearances. The clearance dimensions of each model are shown in Table 2, and the variation of the average meter factor and the linearity error calculated from the simulation results with the clearance is shown in Figure 7.
It can be seen from Figure 7 that as the top circle clearance and the end face clearance of the gear gradually decrease, the average meter factor and the linearity error both show a decreasing trend. The average meter factor decreases from 1074.95 L^(-1) to 1064.62 L^(-1), and the linearity error decreases from 0.63% to 0.18%, with the change rates of 0.96% and 71.43%, respectively. When the top circle clearance is 140 μm and the end face clearance of the gear is 100 μm, the linearity reaches the optimal value of 0.13%, and when the working clearance continues to decrease, the linearity error tends to increase, which needs to be explained by the basic theory of fluid mechanics.
3.2 Mechanism Analysis of the Influence of Assembly Clearance
The volume of a single metering chamber of the cylindrical gear flowmeter is 0.0004605 L, and 28 chamber volumes are discharged per revolution. The theoretical flow rate value q_t of the cylindrical gear flowmeter can be calculated by Equation (14), and the estimated value of the leakage flow Δq can be obtained by subtracting the inlet flow rate value q_s from the theoretical flow rate value q_t, as shown in Equation (15). The variation curve of the leakage flow of each model with the flow rate is shown in Figure 8.
q_t = 2Nv · n, Δq = q_s – q_t, where Δq is the estimated value of the leakage flow, q_s is the inlet flow rate value, q_t is the theoretical flow rate value, v is the volume of the unit volume, and n is the average rotation speed.
It can be seen from Figure 8 that when the clearance of the cylindrical gear flowmeter decreases within a certain range, the leakage flow decreases, but as the clearance continues to decrease, the leakage flow increases instead, and the leakage flow of Model 2 is the smallest. The measurement error caused by the leakage of each model was further estimated, and the variation curve of the measurement error with the flow rate is shown in Figure 9.
It can be seen from Figure 9 that as the gear clearance changes, the measurement error also changes due to the change of the leakage flow. The measurement error of Model 2 is the smallest, with an average absolute percentage error of 0.32%. To explain the influence of the assembly clearance on the measurement performance of the cylindrical gear flowmeter, the pressure loss at the inlet and outlet in the simulation flow field was extracted, and the variation curve of the pressure loss of each model with the flow rate is shown in Figure 10.
It can be seen from Figure 10 that the change trend of the pressure loss is basically the same as that of the leakage flow. When the clearance of the cylindrical gear flowmeter decreases within a certain range, the pressure loss decreases, which reduces the leakage flow, that is, the average meter factor increases. When the clearance continues to decrease, the flow area decreases, the viscous shear force increases, and the gear needs to overcome a greater resistance to rotate, resulting in a greater pressure loss, and the smaller the clearance, the greater the pressure loss, which increases the leakage flow, that is, the average meter factor decreases. Therefore, it can be concluded that the change of the pressure loss in the flow field leads to the change of the average meter factor.
Due to the small top circle clearance and the end face clearance of the gear, the fluid in the clearance is in a laminar flow state. In a complex flow field environment, due to the viscous force of the fluid, part of the fluid adheres to the surface of the gear and rotates with the gear, resulting in a certain deviation between the actual leakage flow and the theoretical leakage flow, which causes the linearity error of each model to change.
4. Influence of Medium Viscosity on the Performance of Cylindrical Gear Flowmeter
When the cylindrical gear flowmeter is actually applied, it will work at different temperatures, and different temperatures will change the basic properties of the medium. The viscosity of the medium has the greatest influence on the leakage flow of the cylindrical gear flowmeter. The kinematic viscosity of YH – 15 aviation hydraulic oil at different temperatures is shown in Table 3.
Using the above simulation method, the working performance of the cylindrical gear flowmeter under the viscosity conditions of 42.7, 22.5, 13.9, 9.7, 7.1, and 5.6 mm^2/s was simulated, and Model 2 with the smallest measurement error was used in the simulation model. Since the leakage flow of the cylindrical gear flowmeter at the minimum flow point of 0.8 L/min is small, only the simulation results at the other four flow points of 20, 40, 60, and 80 L/min under different viscosity conditions were compared. According to the simulation results, the meter factor, average meter factor, and linearity error corresponding to each flow point of the cylindrical gear flowmeter were calculated respectively. The variation curve of the meter factor with the flow rate under different viscosity conditions is shown in Figure 11, and the variation of the average meter factor and the linearity error with the viscosity is shown in Figure 12.
It can be seen from Figure 11 that the meter factor of the cylindrical gear flowmeter gradually increases with the increase of the flow rate. When the viscosity is 22.5 and 7.1 mm^2/s, the meter factor first increases and then decreases, because when the fluid gradually increases from a small flow rate, there is a transition process from laminar flow to turbulent flow, and the performance of the flowmeter will change at this time. It can be seen from Figure 12 that as the fluid viscosity gradually increases, the average meter factor of the cylindrical gear flowmeter shows an upward trend, and the linearity error shows a downward trend. When the viscosity is 42.7 mm^2/s, the linearity error of the cylindrical gear flowmeter is the smallest, indicating that the measurement performance of the cylindrical gear flowmeter is less affected by the high-viscosity fluid. The main reason for the change of the meter factor of the cylindrical gear flowmeter is that the flow state of the fluid under different viscosity conditions is different, resulting in different leakage flows. The leakage flow of the cylindrical gear flowmeter under different viscosity conditions was estimated, and the variation curve of the leakage flow with the flow rate under different viscosity conditions is shown in Figure 13.
It can be seen from Figure 13 that as the fluid viscosity continues to increase, the leakage flow of the cylindrical gear flowmeter shows a decreasing trend, and the decrease of the leakage flow will increase the meter factor. Therefore, the change of the leakage flow caused by the change of the fluid medium viscosity, and then the change of the meter factor, ultimately affects the measurement performance of the cylindrical gear flowmeter.
5. Conclusions
To improve the measurement accuracy of the cylindrical gear flowmeter and reduce the influence of the assembly clearance on the performance of the cylindrical gear flowmeter, this study obtained the variation law of the performance of the DN16 cylindrical gear flowmeter with the assembly clearance through CFD simulation, analyzed the influence mechanism of the assembly clearance on the measurement performance of the cylindrical gear flowmeter, and explored the variation law of the influence of the medium viscosity change on the performance of the cylindrical gear flowmeter. The following conclusions were drawn:
- The trend of the simulated meter factor of the cylindrical gear flowmeter with the flow rate is consistent with the experimental results, which verifies the effectiveness of the simulation method based on the 6-degree-of-freedom model.
- The simulation results of different top circle clearances and gear end face clearances show that as the clearance gradually decreases, the average meter factor and the linearity error of the cylindrical gear flowmeter both show a decreasing trend. When the top circle clearance is 140 μm and the end face clearance of the gear is 100 μm, the linearity error reaches the optimal value of 0.13%.
- As the assembly clearance changes, the leakage flow gradually changes, and the measurement error caused by the leakage flow also changes. When the top circle clearance is 170 μm and the end face clearance of the gear is 130 μm, the measurement error caused by the leakage flow is the smallest, better than 0.32%.
- The measurement performance of the cylindrical gear flowmeter is affected by the change of the medium viscosity. As the fluid viscosity gradually increases, the linearity error shows a decreasing trend. When the viscosity is 42.7 mm^2/s, the linearity error is the smallest, only 0.03%.
In summary, this study provides important guidance for the design, assembly, and application of the cylindrical gear flowmeter by revealing the influence of the assembly clearance and the medium viscosity on the performance of the flowmeter. Further research can be conducted to optimize the design of the flowmeter and improve its measurement accuracy in different working conditions.
Parameter | Value |
---|---|
Measurement Range of Experimental Device | (0.15 – 500) L/min |
Expanded Uncertainty of Experimental Device | 0.05% (k = 2) |
Number of Teeth of Gear in Cylindrical Gear Flowmeter | 14 |
Volume of Single Metering Chamber | 0.0004605 L |
Number of Chamber Volumes Discharged per Revolution | 28 |
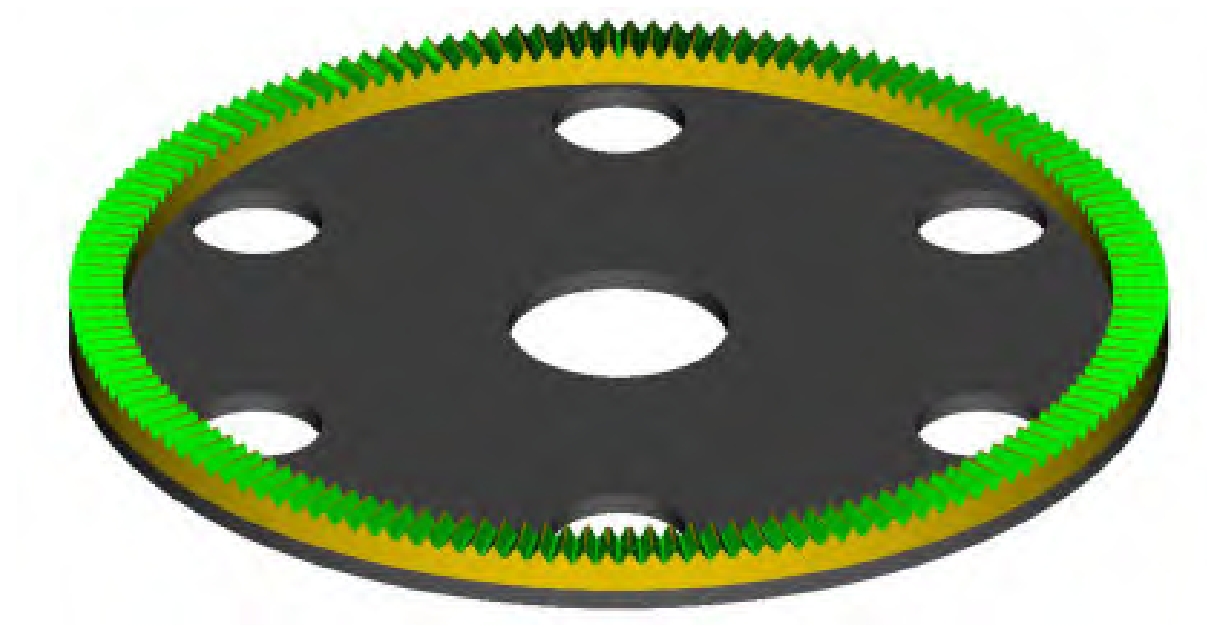