The load stroke curves of the two processes are shown in the figure. It can be seen from the figure that the load change trend of the two processes is relatively similar. It can be seen from the load curve that the forming process of the tooth shape can be divided into three stages: free deformation, filling and corner filling.
In the free deformation stage, due to the free fluidity of the blank, the load curve rises gently. The filling stage starts from the contact between the blank and the tooth cavity to the filling of the middle part of the tooth cavity. In this stage, due to the effect of the contact force, the action time is longer and the load increases gradually.
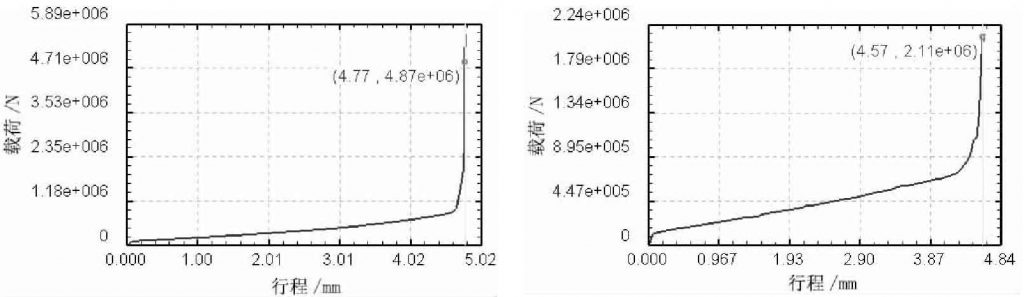
(a) Two way upsetting extrusion with toothed punch (b) two way upsetting extrusion with toothless punch
In the corner filling stage, the space that the blank can fill is very small, so the load increases sharply, so that the cavity can be fully and effectively filled until the load reaches the maximum and the forming is completed. Comparing with Fig. 1 (a) and Fig. 1 (b), it can be seen that in the process of forming spur internal gear, the upsetting extrusion load value of toothless punch is about 57% lower than that of toothed punch, which can reduce the die load and improve the die life.
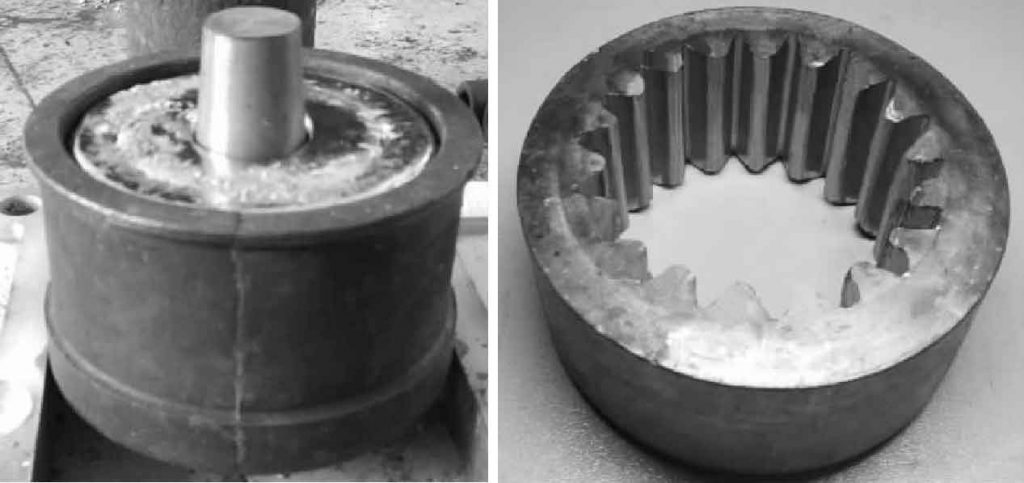
The assembly relationship of the two-way upsetting extrusion die is shown in Fig. 2. The iron material is melted in the resistance furnace and poured into the designed model (Fig. 2a). After condensation, the casting part is taken out and then turned. Finally, the straight tooth cylindrical internal gear is obtained as shown in Fig As shown in Fig. 2 (b), the tooth profile of the obtained spur gear is full filled, the profile is clear, the surface is smooth, and there is no folding and other defects. The experimental results are basically consistent with the numerical simulation results.