Modified straight bevel gears are widely used in various fields such as machine tools, automotive differentials, and other automotive components. The meshing characteristics of the gear pair, such as the contact area and contact form, can directly reflect the meshing performance of the gears. To optimize the design of modified straight bevel gear pairs, it is necessary to study the loaded contact analysis method of straight bevel gears.
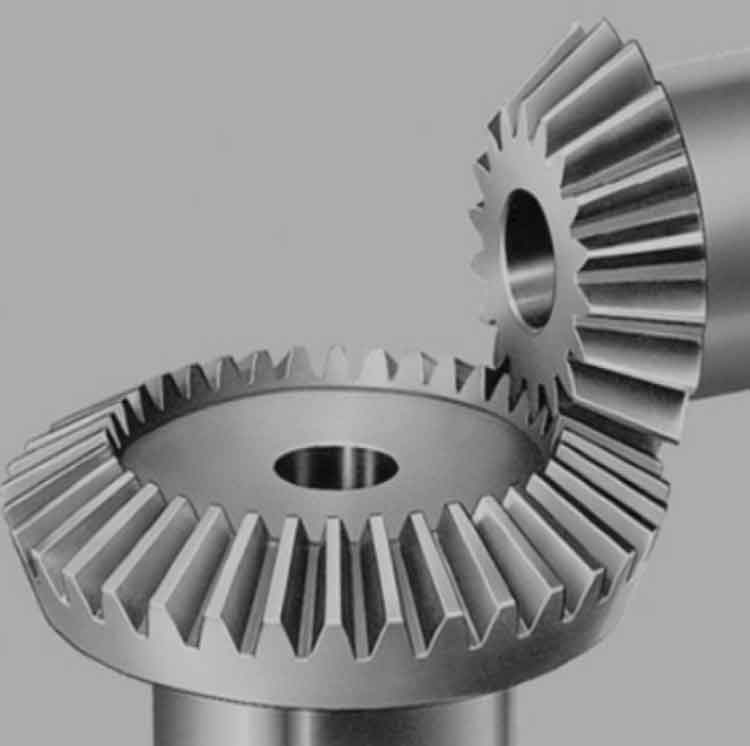
Mathematical Model of Modified Straight Bevel Gears:
- Spherical Involute Straight Bevel Gear Model:
- The tooth profile of a straight bevel gear in a spherical involute is generated based on the principle of spherical involute spreading.
- The transformation relationship between the fixed coordinate system S and the moving coordinate system S1 is expressed as follows:
- [x y z 1]^T = M1 * M2 * [x1 y1 z1 1]^T
- M1 = [sin(φh) cos(φk) 0 0; -cos(φh) sin(φk) 0 0; 0 0 1 0; 0 0 0 1]
- M2 = [1 0 0 0; 0 cos(δb) sin(δb) 0; 0 -sin(δb) cos(δb) 0; 0 0 0 1]
- The coordinates of point KA in the coordinate system S can be expressed as:
- x(φk) = R[cos(φk * sin(δb)) * sin(δb) * cos(φk) + sin(φk * sin(δb)) * sin(φk)]
- y(φk) = R[cos(φk * sin(δb)) * sin(δb) * sin(φk) – sin(φk * sin(δb)) * cos(φk)]
- z(φk) = R * cos(φk * sin(δb)) * cos(δb)
- The spherical involute at the small end, K’A’, can be expressed as:
- x(φk) = (R – B)[cos(φk * sin(δb)) * sin(δb) * cos(φk) + sin(φk * sin(δb)) * sin(φk)]
- y(φk) = (R – B)[cos(φk * sin(δb)) * sin(δb) * sin(φk) – sin(φk * sin(δb)) * cos(φk)]
- z(φk) = (R – B) * cos(φk * sin(δb)) * cos(δb)
- Tooth Root Fillet Model:
- The tooth root fillet must be tangent to the tooth root circle and the spherical involute tooth shape.
- The expression for the tooth root fillet is obtained from the literature [20] as:
- Rf = Mfi * (rf * cos(θ) rf * sin(θ) √(R^2 – rf^2) 1)^T
- Surface Equation of Modified Straight Bevel Gear:
- The modification amount is defined using a binary quadratic polynomial:
- δ(x, y) = a1 + a2 * x + a3 * y + a4 * x * y + a5 * x^2 + a6 * y^2
- Considering only the tooth length and tooth profile modification, the coefficients a5 and a6 can be expressed as:
- a5 = δs / (B / 2)^2
- a6 = δy / (Pind * Pend^2)
- The discrete points of the modified tooth surface are combined with the spline surface to generate a new tooth surface equation R(u, v).
- The B-Spline surface equation can be expressed as:
- R(u, v) = ∑(i=0 to m) ∑(j=0 to n) di,j * Ni,k(u) * Nj,l(v)
- To ensure C2 continuity of the surface, let k = l = 3, and the equation can be transformed into:
- R(u, v) = U * Mb * [d(i – 3, j – 3) d(i – 3, j – 2) d(i – 3, j – 1) d(i – 3, j); d(i – 2, j – 3) d(i – 2, j – 2) d(i – 2, j – 1) d(i – 2, j); d(i – 1, j – 3) d(i – 1, j – 2) d(i – 1, j – 1) d(i – 1, j); d(i, j – 3) d(i, j – 2) d(i, j – 1) d(i, j)] * Mb^T * V^T
- U = [1 u u^2 u^3]
- V = [1 v v^2 v^3]
- Mb = 1/6 * [1 4 1 0; -3 0 3 0; 3 -6 3 0; -1 3 -3 1]
- The normal vector n can be expressed as:
- n(u, v) = Ru × Rv
- The modification amount is defined using a binary quadratic polynomial:
Contact Analysis:
- Principle of Conjugate Contact:
- Two tooth surfaces are in conjugate contact when the following three principles are followed:
- The normal vectors at the contact point are collinear.
- The velocity vector is perpendicular to the normal vector.
- The position vectors are equal.
- Two tooth surfaces are in conjugate contact when the following three principles are followed:
- Collinearity of Normal Vectors:
- Assuming that the pinion rotates by an angle up around k(p)[g] and the gear rotates by an angle ug around k(g)[g] for conjugate contact, the expressions for ug and up can be obtained as:
- μp = tan^(-1)[((k(g)^(g) × k(g)^(p)) · (n(g)^(p) × k(g)^(p)) – k(g)^(g) · n(g)^(g)) / ((k(g)^(g) × k(g)^(p)) · n(g)^(p))] · n(g)^(p) / cos(tan^(-1)[((k(g)^(g) × k(g)^(p)) · (n(g)^(p) × k(g)^(p)) · n(g)^(p)) / ((k(g)^(g) × k(g)^(p)) · n(g)^(p))]) – tan^(-1)[((k(g)^(g) × k(g)^(p)) · (n(g)^(p) × k(g)^(p)) / ((k(g)^(g) × k(g)^(p)) · n(g)^(p)))]
- μg = tan^(-1)[((k(g)^(p) × k(g)^(g)) · (n(g)^(g) × k(g)^(g)) – k(g)^(p) · n(g)^(p)) / ((k(g)^(p) × k(g)^(g)) · n(g)^(g))] · k(g)^(p) / cos(tan^(-1)[((k(g)^(p) × k(g)^(g)) · (n(g)^(g) × k(g)^(g)) · n(g)^(g)) / ((k(g)^(p) × k(g)^(g)) · n(g)^(g))]) – tan^(-1)[((k(g)^(p) × k(g)^(g)) · (n(g)^(g) × k(g)^(g)) / ((k(g)^(p) × k(g)^(g)) · n(g)^(g)))]
- Assuming that the pinion rotates by an angle up around k(p)[g] and the gear rotates by an angle ug around k(g)[g] for conjugate contact, the expressions for ug and up can be obtained as:
- Perpendicularity of Normal Vector and Velocity Vector:
- The relative velocity vector can be expressed as:
- V^(p) = k(g)^(p) × R(g)^(p)
- V(g) = zg * k(g)^(g) × R(g)^(g)
- V(pg) = V(p) – V(g)
- Substituting the above equation into the second principle, we get:
- (zg * k(g)^(g) × R(g)^(g)) · n(g)^(g) + (zp * k(g)^(p) × R(g)^(p)) · n(g)^(p) = 0
- Transforming the above equation, we get:
- Δm = ((k(g)^(p) × R(g)^(p)) · n(g)^(p)) / ((k(g)^(g) × R(g)^(g)) · n(g)^(g)) – zg / zp = 0
- The relative velocity vector can be expressed as:
- Equality of Position Vectors:
- After the pinion and gear rotate by angles ug and up, respectively, the position vectors at the contact point should be equal.
- The following expression can be obtained:
- (R(ε)^(ε) * n(ε)^(ε))^T = M(k(ε)^(ε), με) * (R(ε)^(ε) * n(ε)^(ε))^T
- (R(g)^(p) * n(g)^(p))^T = M(k(g)^(p), μp) * (R(p)^(p) * n(p)^(p))^T
- If R(g)^(s) = R(g)^(p) does not hold, the difference vector ΔR(gp)[g] can be expressed as:
- ΔR(g)^(p) = R(g)^(g) – R(g)^(p)
- Then, this vector can be converted to the axial components as:
- ΔR(g)^(g) = -H * k(g)^(p) + J * k(g)^(g) – V * j(g)^(g)
- V = -ΔR(g)^(gp) · j(g)^(g)
- H = -ΔR(g)^(g) · k(g)^(p)
- J = ΔR(g)^(gp) · k(g)^(g)
- Solution of Contact Trace:
- There are two applicable scopes for TCA:
- Tooth Contact Analysis given the midpoint of the contact area.
- Tooth Contact Analysis given the installation position.
- For the above two contact forms, the explanations are as follows:
- Given the Midpoint of the Contact Area:
- Given the parameters ug and vg of the meshing point on the tooth surface of the gear, search the tooth surface with up and vp of the pinion tooth surface as independent variables.
- By solving the equation 0.001 – |J| ≥ 0 and 0.00002 – |Δm| ≥ 0, the unique solution for up and vp can be obtained.
- Substitute up and vp into the pinion tooth surface equation to obtain the normal vector.
- Obtain the current adjustment values V, H, and J from equation (23) and set them as the initial values V0, H0, and J0 for the installation position.
- Then, give an initial value to vg of the gear (increase or decrease by an increment ±Δvg in each iteration), and by constructing equation (25), the other three parameters ug, up, and vp can be obtained.
- The line connecting a series of meshing points is the meshing line.
- Given the Installation Position:
- Set the installation adjustment values V, H, and J as the initial values V0, H0, and J0 for the installation position.
- Solve the equation 0.001 – |J0 – J| ≥ 0, 0.0005 – |V0 – V| ≥ 0, 0.0005 – |H0 – H| ≥ 0, and 0.00002 – |Δm| ≥ 0 to obtain the parameters ug, vg, up, and vp corresponding to the midpoint of the contact area.
- After obtaining the contact midpoint, give an increment Δvg to vg of the gear, and iterate out the other three parameters ug1, up1, and vp1 for the contact point according to the first three equations in equation (26) (stop the calculation when it exceeds the tooth surface range), and the contact trace in the entire cycle can be obtained.
- Given the Midpoint of the Contact Area:
- There are two applicable scopes for TCA:
Calculation of Loaded Contact Characteristics:
- Contact Deformation and Elliptical Contact Area:
- According to the Hertz contact theory, when conjugate contact occurs, the load causes elastic deformation on the tooth surface, forming an elliptical contact area.
- The normal curvature on the surface represents the degree of bending of the curve in the normal direction of the surface.
- A point on the surface and the tangent vector dR = Ru * du + Rv * dv at this point can be expressed as:
- k = (L * du^2 + 2 * M * du * dv + N * dv^2) / (E * du^2 + 2 * F * du * dv + G * dv^2)
- The first fundamental quantities E, F, G and the second fundamental quantities L, M, N can be expressed as:
- E = Ru · Ru
- F = Ru · Rv
- G = Rv · Rv
- L = 1 / √(E * G – F^2) · |Rv * Rv * Ru * v|^T
- M = 1 / √(E * G – F^2) · |Ru * Rv * Ru * v|^T
- N = 1 / √(E * G – F^2) · |Ru * Ru * Rv * v|^T
- Principal Curvature and Direction:
- The principal curvature is the extreme value of the curvature at a point on the surface.
- To calculate the principal curvature and direction at a point on the surface, the equation (27) is converted into a fractional function expression:
- k(x) = (L * x^2 + 2 * M * x + N) / (E * x^2 + 2 * F * x + G)
- Taking the derivative with respect to x when x = du / dv, we get:
- (E * x^2 + 2 * F * x + G) * k'(x) + (L * x^2 + 2 * M * x + N) = 0
- At the extreme point of k, k'(x) = 0, we get the following expression:
- (k * E – L) * x + (k * F – M) = 0
- Substituting equation (32) into equation (31), we get:
- (k * F – M) * x + (k * G – N) = 0
- Further, the relationship between the principal curvature and the principal direction can be expressed as:
- {(k * E – L) * du + (k * F – M) * dv = 0; (k * F – M) * du + (k * G – N) * dv = 0}
- Relationship between Contact Ellipse Axes and Curvature:
- According to the Hertz theory, the relationship between the lengths a and b of the major and minor axes of the contact ellipse can be expressed as:
- ((kp1 + kg1) / (kp2 + kg2)) = ((a / b)^2 * E(e) – K(e)) / (K(e) – E(e))
- a * b = ((3 * F * Re) / (4 * η))^(2 / 3) * [F(e)]^2
- The parameters in the above equation are defined as:
- e = √(1 – (b / a)^2)
- Re = √(1 / (kp1 + kg1) * 1 / (kp2 + kg2))
- K(e) = ∫(0 to π/2) 1 / √(1 – e * sin^2(θ)) dθ
- E(e) = ∫(0 to π/2) √(1 – e * sin^2(θ)) dθ
- η = 1 / ((1 – v1^2) / E1 + (1 – v2^2) / E2)
- F(e) = ((4 / (π * e^2))^(1 / 3) * (b / a)^(1 / 2) * {[((a / b)^2 * E(e) – K(e)) * (K(e) – E(e))]^(1 / 6)}
- According to the Hertz theory, the relationship between the lengths a and b of the major and minor axes of the contact ellipse can be expressed as:
- Maximum Stress and Stress Distribution:
- The maximum stress value pmax can be obtained as:
- pmax = (3 * F) / (2 * π * a * b)
- The stress distribution along the major and minor axes can be expressed as:
- p(x) = pmax * √(1 – x / a)
- p(y) = pmax * √(1 – y / b)
- The maximum stress value pmax can be obtained as:
- Load Distribution and Contact Characteristics in Multi-tooth Meshing:
- In the multi-tooth meshing state, the external total load is distributed among multiple tooth pairs, resulting in time-varying contact characteristics during the meshing cycle.
- To solve the contact characteristics of multi-tooth meshing, the load distribution coefficient needs to be obtained.
- The modified straight bevel gear has a variable cross-section tooth profile. To calculate the deformation of the gear tooth as a whole is difficult, so the micro-element idea is used to slice the gear tooth.
- The gear tooth can be equivalent to a series of parallel slice tooth segments by dividing along the back cone.
- Each slice tooth is equivalent to a spring model, and the tooth stiffness can be expressed as:
- K = dK1 + dK2 + dK3 + dK4 +… + dKN – 1 + dKN = ∑(i=1 to N) dKi
- The deformation equivalent stiffnesses corresponding to bending, shear, and axial compression deformations can be expressed as:
- Kb = dKb1 + dKb2 + dKb3 + dKb4 +… + dKb(N – 1) + dKbN = ∑(i=1 to N) dKbi
- Ks = dKs1 + dKs2 + dKs3 + dKs4 +… + dKs(N – 1) + dKsN = ∑(i=1 to N) dKsi
- Ka = dKa1 + dKa2 + dKa3 + dKa4 +… + dKa(N – 1) + dKaN = ∑(i=1 to N) dKai
- According to the energy equivalence principle, dKb, dKs, and dKa can be expressed as:
- 1 / dKb = ∫(0 to xa) 3[((xa – x) * cos(α) – yα * sin(α))^2 / (2 * E * y^3 * db)] dx
- 1 / dKs = ∫(0 to xa) 1.2 * cos^2(α) / (2 * G * y * db) dx
- 1 / dKa = ∫(0 to xa) sin^2(α) / (2 * E * y * db) dx
- The total stiffness Kt of one gear can be expressed as:
- 1 / Kt = (1 / Kb + 1 / Ks + 1 / Ka)
- The Hertz contact equivalent stiffness Kh corresponding to the Hertz contact deformation generated at the contact surface between the pinion and the gear can be calculated using the approximate formula:
- Kh = (Ee^0.9 * (2 * a)^0.8 * F^0.1) / 1.275
- Ee = 2 * E1 * E2 / (E1 + E2)
- The total stiffness K(pg) of the gear pair can be expressed as:
- K(pg) = 1 / ((1 / K1(p)) + (1 / Kh) + (1 / K1(g)))
- The overall total deformation δ of the gear pair under the meshing force Ft can be expressed as:
- δ = F / K(pg)
- When double tooth pairs are in mesh, the load relationship between the two contact pairs is as follows:
- F = F1 + F2
- By setting the initial load distribution coefficient, obtaining the meshing forces of each tooth pair according to equation (48), and obtaining the total deformation δ of each tooth pair according to equation (46), through repeated iterations until the deformation coordination equation in equation (47) is satisfied, the load distribution coefficient is obtained. Finally, by substituting the loads of each tooth pair into equations (36) – (39), the contact characteristics can be obtained.
- Method Verification and Result Analysis:
- Comparison of Meshing Lines:
- The meshing lines obtained by the loading contact characteristic calculation method and the finite element method are compared, as shown in Figure 11.
- The results show that the two methods can effectively conduct contact analysis on the modified straight bevel gear to obtain the contact points and the contact trace during the entire meshing process.
- Comparison of Maximum Contact Stress:
- The maximum contact stress pmax obtained by the loading contact characteristic calculation method and the finite element method is compared, as shown in Figure 12.
- The results show that the calculation results of the two methods are close, and the change trend is consistent.
- In the case of a torque of 100 Nm and 150 Nm, the partial results of the contact force F, the lengths of the major and minor axes a and b, and the maximum contact stress pmax obtained by the two methods are shown in Tables 2 and 3, respectively.
- The results show that under different external load conditions, both methods can obtain accurate calculation results, with the contact force error within 1% and the maximum contact stress error within 2%.
- Comparison of Contact Stress Distribution Cloud Maps:
- The contact stress distribution cloud maps obtained by the loading contact characteristic calculation method and the finite element method are shown in Figure 13.
- The results show that the contact characteristics of the two methods match well, and the maximum contact stress values are close.
- Conclusion:
- The binary polynomial is used to modify the tooth surface of the straight bevel gear, and the discrete tooth surface points are generated. Then, the B-Spline surface is used to reconstruct the modified tooth surface equation. Based on the gear meshing principle, the contact analysis of the gear pair can be effectively conducted to obtain the instantaneous conjugate contact trace points and the contact trace during the entire meshing cycle.
- Based on the Hertz contact model, the loading contact analysis model is constructed on the basis of the contact analysis. By using the beam deformation model, the cumulative integral potential energy method, the series stiffness model, and the deformation coordination and force balance principles, the calculation task of the meshing characteristics of the modified straight bevel gear is completed.
- By comparing the results of the loading contact characteristic calculation method with the finite element calculation results, the contact characteristics of the two are consistent, and the errors of the contact force and the contact stress are within 2%. Compared with the finite element method, this model adopts a simple integration and iterative loop solution method, which can effectively improve the loading contact analysis efficiency of the modified bevel gear.
- The loading contact characteristic calculation method can be extended to the loading contact analysis of spiral bevel gears and other bevel gear pairs. The accurate calculation of the loading contact characteristics can also provide a reference standard for the rapid iterative optimization design of the bevel gear pair transmission system.
- In the follow-up research, based on the above research content, the dynamic model of the straight bevel gear system will be constructed to analyze the vibration response signal of the entire system and propose a design method for high-power density gearboxes.