In the field of mechanical engineering, planetary gear systems play a crucial role in various applications due to their advantages such as high power density, compact structure, and smooth transmission. However, the load sharing performance of these systems is often affected by factors such as manufacturing and installation errors, component deformation, and gear pair clearances. Therefore, improving the load sharing performance of planetary gear systems is of great significance for ensuring their reliability and performance.
The background and significance of this research lie in the need to address the issue of uneven load distribution in planetary helical gear systems. Uneven load sharing can lead to reduced system reliability, increased wear, and decreased efficiency. By studying the load sharing characteristics of these systems and developing appropriate analysis methods, it is possible to improve the design and performance of planetary gear systems, making them more reliable and efficient in various applications.
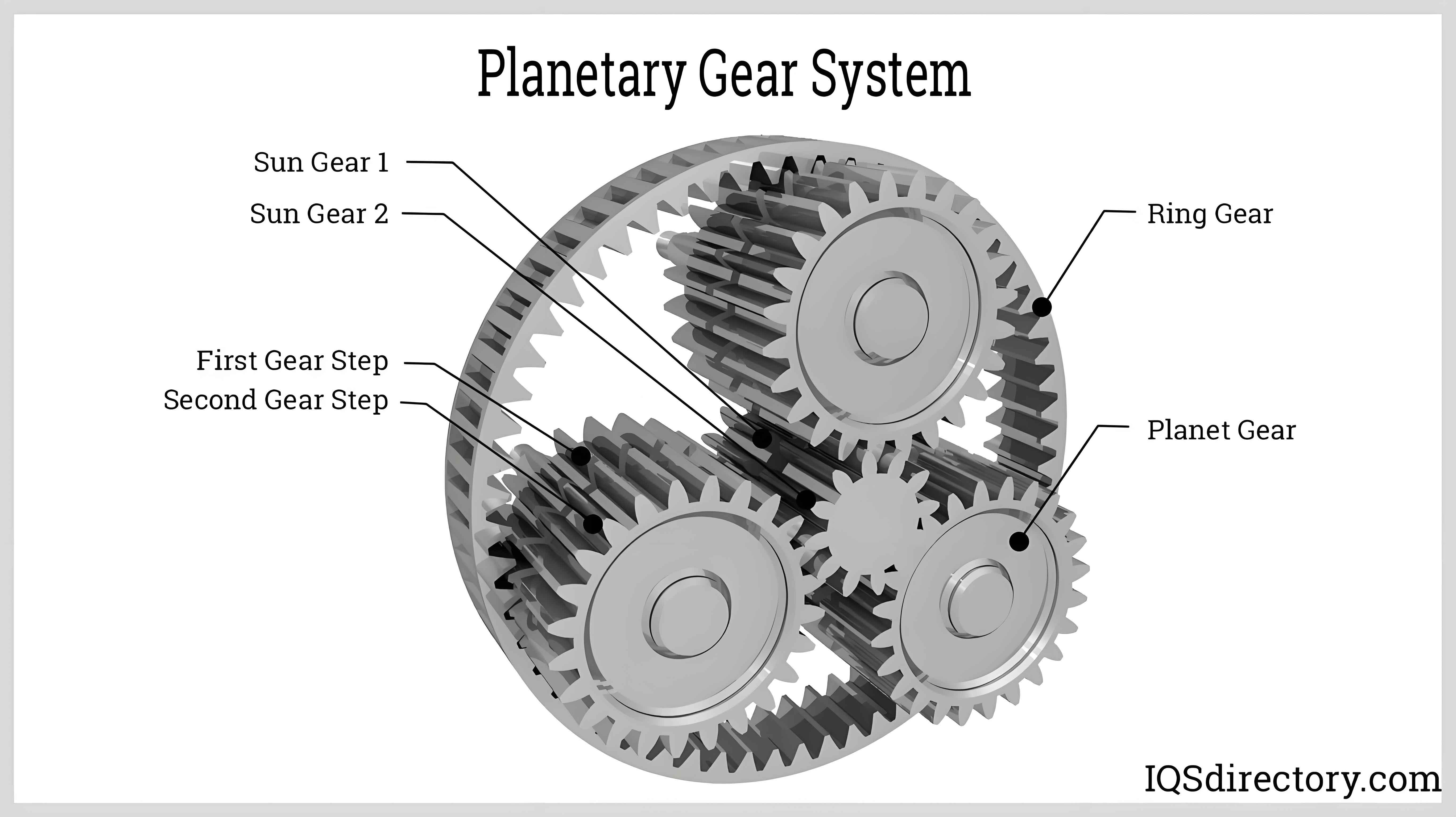
Previous studies on planetary gear systems have focused on various aspects, including the influence of manufacturing errors, installation errors, tooth modifications, and component floating on the load sharing performance. However, these studies often use simplified models or focus on individual factors, which may not accurately reflect the complex interactions within the system. Additionally, the traditional tooth surface loaded contact analysis methods are not suitable for the load sharing design and analysis of planetary gear systems due to the coupling relationships between the forces of the inner and outer gear pairs and the contact gaps of the planetary wheels.
The main content of this research includes the tooth surface geometric contact analysis of the planetary gear system, the establishment of the tooth surface loaded contact model considering the radial floating of the components, and the calculation examples and analysis.
- Tooth Surface Geometric Contact Analysis of the Planetary Gear System
- Basic Principle: The basic principle of tooth surface geometric contact analysis is that two continuously tangent contact tooth surfaces have a common contact point and normal line in the same coordinate system at any time. By listing the tooth surface geometric contact analysis equation based on this principle, the tooth surface contact imprint and geometric transmission error under light load can be obtained, and the meshing position and the initial tooth surface contact gap of the meshing tooth pair can be further calculated, providing data for the tooth surface loaded contact analysis calculation.
- Coordinate System: In the planetary gear system, multiple gear pairs are involved, and the position vector and normal vector of the contact points of each inner and outer gear pair need to be transformed into a unified fixed coordinate system. The meshing coordinate systems of each gear pair in the system are shown in Figure 1, where the of – xy – zf is a unified fixed coordinate system with the midpoint of the rotation center axis of the planet carrier as the origin, and its yf axis passes through the center axis of the local reference coordinate system of the first planetary wheel and is parallel to it.
- Installation Errors: The main installation errors considered in this study are the shaft intersection angle and center distance installation errors of the sun gear and ring gear relative to the unified fixed reference coordinate system.
- Tooth Surface Loaded Contact Model Considering Radial Floating of Components
- Model Equation: When the components float, the tooth surface loaded contact equation for the inner meshing pair is given by a set of equations, including the deformation coordination condition, force balance condition, radial floating condition for equal normal forces of the planetary wheels, and non-embedding condition for the tooth surface. Similar equations can be listed for the outer meshing tooth surface.
- Solution Method: The solution of the multi-body tooth surface loaded contact equation under component floating is difficult due to the influence of the shaft intersection angle error. Therefore, a stepwise iterative method is used to solve for the floating displacement of the components, the tooth surface load, and the tooth load deformation. The solution process involves decomposing the radial displacement of the ring gear (sun gear) into the X and Y directions along the unified fixed coordinate system, and iteratively determining the radial displacement in each direction using the golden section method until the step size of each displacement is smaller than the preset precision.
- Calculation Examples and Analysis
- Parameters and Assumptions: Taking the planetary gear basic parameters in Table 1 as an example, the planet carrier is fixed, the input torque of the sun gear is 1500 N·m, and there are installation errors in the center distance and shaft intersection angle. The sun gear and ring gear have no tooth modification, and the planetary wheel has a slight parabolic modification for tooth surface geometric contact analysis.
- Analysis without Radial Floating: When there is only the center distance installation error, the geometric transmission errors of each gear pair are different, but the curve shapes are the same, and the tooth surface contact trace positions are the same. The maximum geometric transmission error of the inner meshing gear pair follows a certain order, and the change law of the maximum load distribution coefficient is opposite to that of the geometric transmission error. The difference between the normal force at the meshing position and the theoretical uniform load normal force further reflects the load distribution of each planetary wheel.
- Analysis with Radial Floating: Under the combined installation error, the radial floating displacement is obtained through the multi-body tooth surface loaded contact analysis. The radial floating can make the geometric transmission errors of each gear pair approach each other, but it cannot achieve complete load sharing when there is a shaft intersection angle error. However, when only the center distance error is considered, ideal load sharing can be achieved.
- Load Sharing Effect: After radial floating, the maximum difference between the normal force at the meshing position of each gear and the theoretical uniform load normal force decreases, and the load carried by each gear pair approaches the theoretical uniform load. The load distribution on the full tooth surface of the planetary wheels becomes more equal after radial floating.
- Influence of Radial Floating: The radial floating only ensures that the macroscopic load between each gear pair tends to be equal, and the microscopic load sharing on the full tooth surface of a single gear needs to be achieved through tooth surface modification.
Analysis Aspect | Details |
---|---|
Without Radial Floating | Geometric transmission errors are different, but curve shapes and contact trace positions are the same. Maximum load distribution coefficient changes opposite to geometric transmission error. Difference in normal force reflects load distribution of planetary wheels. |
With Radial Floating | Radial floating displacement is obtained. It makes geometric transmission errors approach each other, but cannot achieve complete load sharing with shaft intersection angle error. Ideal load sharing is possible with only center distance error. |
Load Sharing Effect | Maximum difference in normal force decreases, and load approaches theoretical uniform load. Load distribution on full tooth surface becomes more equal. |
Influence of Radial Floating | Ensures macroscopic load equality, but microscopic load sharing requires tooth surface modification. |
The main conclusions of this research are as follows:
- The proposed multi-body tooth surface coupled loaded contact analysis method considers the coupling characteristics of the meshing forces and contact gaps of the inner and outer gear pairs, and can obtain the load distribution of each branch of the planetary wheel system and the tooth surface load distribution of all meshing tooth pairs. Compared to the commonly used concentrated mass modeling methods for planetary wheel systems, this method is a distributed force model and has certain advantages.
- After the radial floating of the components, the curve shape of the geometric transmission error of each gear pair in the system does not change, but the numerical value gradually approaches. This shows that the radial floating has no influence on the normal gap of the contact line of a single gear pair, but only affects the relative tooth gap between the gear pairs. The process of component floating is actually the process of gradually coordinating and approaching the initial tooth gaps of the inner and outer gear pairs.
- The radial floating only ensures that the macroscopic load between each gear pair tends to be equal, and for a single gear pair, the microscopic load sharing on the tooth surface needs to be further ensured through tooth surface modification techniques.
- When there is a shaft intersection angle error, the tooth gap (geometric transmission error) of each gear pair changes differently, and although the component floating can improve the load sharing, it cannot achieve complete load sharing. However, when only the center distance error of the sun gear and ring gear is considered, the geometric transmission errors and tooth surface imprints can completely coincide after radial floating, thus achieving ideal load sharing.
Conclusion | Details |
---|---|
Advancement of the Method | Considers coupling characteristics, obtains load distribution and tooth surface load distribution. Is a distributed force model with advantages over commonly used methods. |
Effect of Component Floating | Does not change curve shape of geometric transmission error, but makes numerical values approach. Indicates radial floating affects relative tooth gaps. Process of component floating is about coordinating initial tooth gaps. |
Load Sharing Limitation | Radial floating ensures macroscopic load equality, but microscopic load sharing requires tooth surface modification. |
Load Sharing with Different Errors | Shaft intersection angle error prevents complete load sharing, while only center distance error allows ideal load sharing through radial floating. |
However, this research also has some limitations. For example, the iterative solution process may be time-consuming, and the accuracy of the results may be affected by the simplifications and assumptions made in the model. Future research could focus on improving the efficiency and accuracy of the solution method, as well as considering more factors that may affect the load sharing performance of the planetary gear system.