SolidWorks software is used to complete the modeling of the whole gearbox. The gear mesh model is imported into ADAMS software and related settings are carried out to complete the dynamic modeling of the gear on the rigid body. According to the actual working condition, it is mainly set to define the rotating pair at four bearing positions; add the drive at the input end of the driving shaft, with the rotating speed set at 1500 R / min; define the load torque at the output end of the driven shaft as 2 N / M; define the contact force between the two gears. After the simulation calculation, the load change curve of each bearing center position can be extracted. Figure 1 is the spectrum of the horizontal force of the bearing position at the load end of the output shaft.
The gearbox is a single-stage transmission mode with two straight cylindrical gears. The number of teeth of the input pinion and the output pinion is 55 and 75 respectively. According to the above figure, the main frequency component of the excitation force borne by the bearing is 1375hz and its multiple frequency. 1375hz is the meshing frequency of the gearbox at the speed of 1500 R / min.
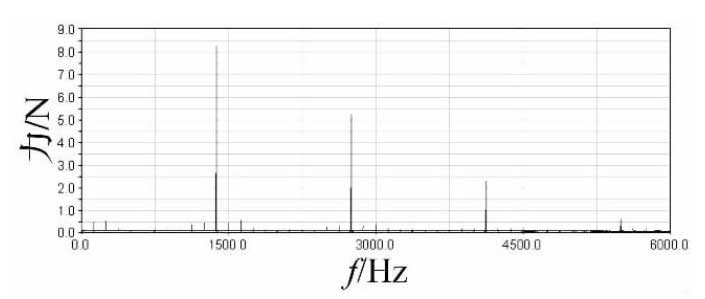
The APDL parametric design language of ANSYS software is used to complete the modeling, loading, solution and post-processing of gearbox. In order to improve the efficiency and accuracy of the solution, the solid 187 unit is used in the study to mesh the box body, with a total of 95771 units and 116714 nodes. The three-dimensional model of the box body is shown in Figure 2.
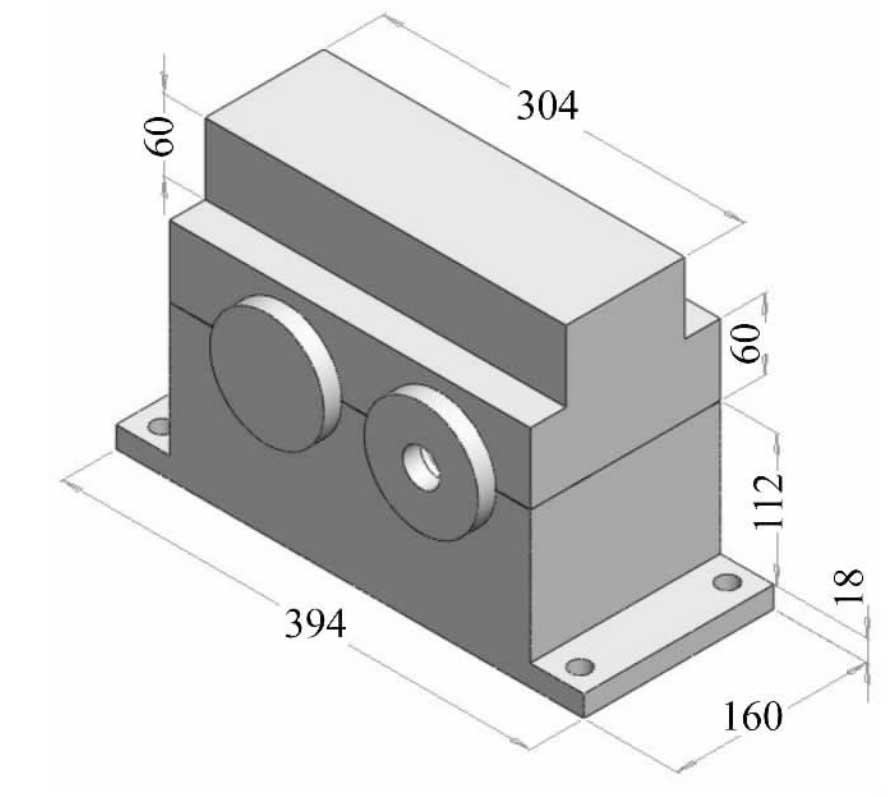
In addition, the bearing is a difficult part to deal with. In order to simplify the system properly, the mass unit of mass21 is established in the center of the four bearing positions of the box, which is connected with the corresponding position node of the bearing seat through the spring damping unit of combin14 to simulate the bearing, and the mass unit of mass21 is assigned the corresponding quality attribute.
The reliability of the finite element model is verified by comparing the results of modal simulation and modal test. The load spectrum of bearing center position calculated by Adams is extracted, which is read into ANSYS by APDL program and loaded into corresponding mass21 unit position. After completing the relevant settings, the steady-state vibration response of the box can be solved.