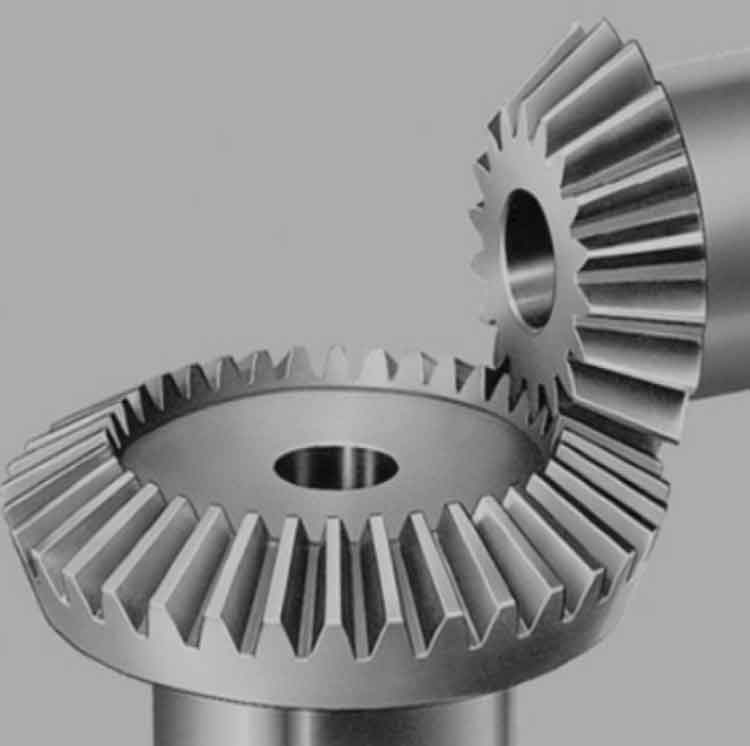
Analyzing stress distribution in straight bevel gear teeth is essential to ensure the gears can withstand the mechanical loads they encounter during operation. The stress distribution analysis helps engineers optimize the gear design, material selection, and heat treatment processes to ensure the gears’ reliability and longevity. Here’s how stress distribution in straight bevel gear teeth is analyzed:
1. Finite Element Analysis (FEA):
- FEA is a powerful numerical simulation method used to analyze stress distribution in complex geometries, including gear teeth.
- Engineers create a detailed 3D model of the gear, meshing the teeth accurately, and apply the loads and boundary conditions that simulate the actual operating conditions.
- The FEA software calculates the stress distribution throughout the gear tooth under various loads, helping identify high-stress regions.
2. Hertzian Contact Analysis:
- Hertzian contact theory is used to analyze the stress distribution at the contact points between the gear teeth during meshing.
- The analysis takes into account the contact forces, curvatures of the gear teeth, and material properties to calculate the contact stresses.
3. Lewis Equation:
- The Lewis equation is commonly used to determine the bending stress in straight bevel gear teeth.
- It considers factors such as the applied load, gear geometry, and material properties to calculate the maximum bending stress at the gear tooth root.
4. AGMA Standards:
- The American Gear Manufacturers Association (AGMA) provides standards and guidelines for gear design and analysis.
- AGMA standards include recommendations for gear stress analysis and factors of safety to ensure gears meet the required durability and strength criteria.
5. Material Properties and Heat Treatment:
- Accurate material properties, such as modulus of elasticity and yield strength, are crucial for stress analysis.
- Heat treatment processes, like carburizing and quenching, are considered to achieve the desired hardness and strength distribution in the gear teeth.
6. Dynamic Analysis:
- Dynamic analysis considers the effects of gear rotation and meshing frequency on stress distribution.
- The dynamic loads and vibrations are analyzed to assess the gear’s fatigue life and potential failure modes.
7. Tooth Profile Optimization:
- Tooth profile modifications, such as crowning and tip relief, can be applied to achieve more uniform stress distribution and improve the gear’s load-carrying capacity.
8. Finite Life and Durability Assessment:
- The analysis considers the number of gear mesh cycles the gear is expected to endure during its operational life.
- Based on this, a durability assessment is made to ensure the gear meets the required lifespan without failure.
By analyzing the stress distribution in straight bevel gear teeth, engineers can optimize the gear design, material selection, and manufacturing processes to ensure the gears can handle the mechanical loads with sufficient safety margins and achieve long-lasting and reliable performance in various applications.