Since the 1990s, with the development of computer software and hardware, numerical simulation methods have made great progress. There are many finite element software and methods that can be used to accurately simulate the plastic deformation process. Many experts and scholars at home and abroad have also studied this.
China has also done a lot of research on the forging process of gears by means of numerical simulation. Liuquankun, huchengliang and Wang Qiang studied the influence of mold geometry on metal flow, analyzed and compared three different mold design schemes by using numerical simulation method, and obtained a reasonable and feasible scheme.
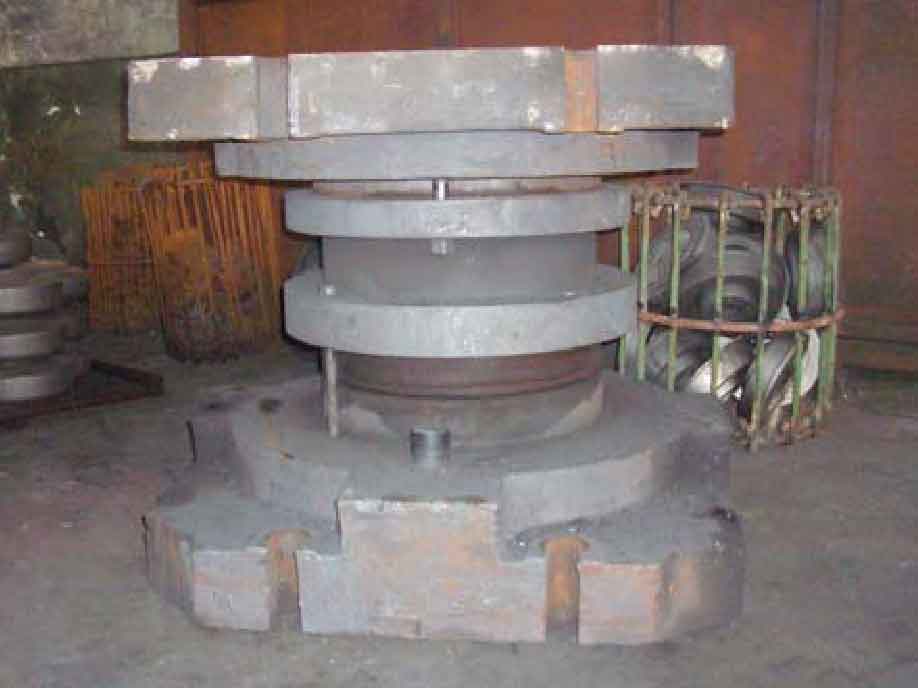
Zhangqingping, zhaoguoqun, etc. put forward a new scheme of closed die forging of spur gear formed by two-step inward flow splitting method, and simulated the forming process by three-dimensional rigid plastic finite element method. Zhan Xianyi, Liu Zhanfang, Liu daolun, etc. developed a three-dimensional finite element analysis system for gear precision forging, The system can analyze the mechanical response in the forging process and obtain the stress and strain data of the upper die, workpiece and lower die. Wanghuajun, Xia Juchen, chengpeiyuan, etc. simulated the precision forging of driven spiral bevel gear by finite element method, obtained the deformation process of gear forging, explained the reason why it is difficult to cold precision forge large section spiral bevel gear, and put forward the precision forging process scheme of driven spiral bevel gear.
Yangshenhua, koushuqing, etc. studied the cold block forging precision forming process of the planetary gear and half shaft gear of the car differential, analyzed it with the finite element method, and designed a special hydraulic die base system. Fang Yuan, luoshanming, Wang Wei, etc. studied the influence of the main structural parameters of the gear, such as the number of teeth, modulus and pressure angle, on the precision forging of spiral bevel gear by using the three-dimensional rigid plastic finite element method. The results show that the smaller the number of teeth and modulus, the smaller the forming load, while the change of pressure angle has little effect on the forming load. Hewangzhi, luoshanming, etc. used rigid plastic finite element method to analyze the warm forging process of spiral bevel gear, and analyzed the effects of friction, blank temperature, preheating temperature, forging speed and other parameters on the forging load, die temperature field and die wear of spiral bevel gear.
Jiangwenbin and gongdongmei studied the cold forging of cylindrical spur gears, and studied the effects of process parameters such as friction, forming speed and shunt aperture on forming load by using numerical simulation method. The results show that the friction force and shunting hole diameter have great influence on the forming load, and the forming speed has little influence on the forming load. Chong Dongmei also studied the cold forging process of large module cylindrical spur gear by using the floating die and radial split affinity process, and carried out numerical simulation by using the finite element software, and obtained the data of metal flow law and forming load in the deformation process.