Abstract
This paper presents a comprehensive analysis and optimization of assembly errors in the spindle cutter disc component of a bevel gear milling machine. By establishing a geometric feature error model based on small displacement torsors (SDTs), Monte Carlo simulation and response surface methodology are employed to determine the actual variation ranges of error parameters and their functional relationships with tolerances. An error model for mating surfaces is developed to investigate error propagation characteristics in both series and parallel mating configurations. A tolerance optimization model targeting minimum tolerance cost, subject to assembly precision reliability and tolerance principles, is formulated and applied to the spindle cutter disc component. The study reveals that an 8.36% reduction in machining costs can be achieved while maintaining an assembly precision reliability of not less than 97%, demonstrating the value of this approach in guiding tolerance design.
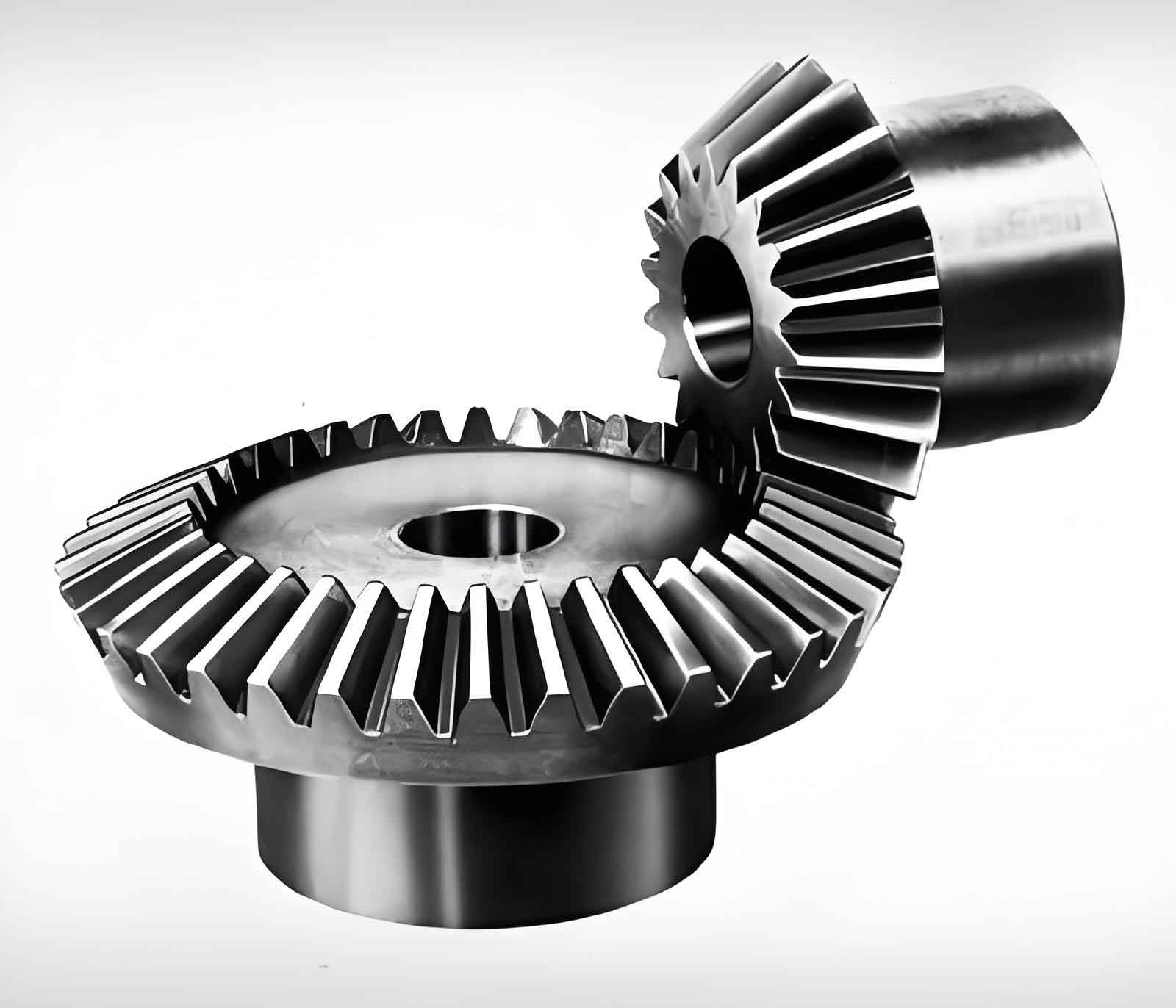
1. Introduction
The machining accuracy of components plays a crucial role in ensuring the overall assembly quality of machine tools, particularly in precision machinery such as bevel gear milling machines. Assembly errors, resulting from the accumulation of component errors, can significantly impact the performance and lifespan of the machine. Therefore, it is imperative to analyze the geometric features of components, establish accurate assembly error models, and optimize tolerance design.
Previous studies have extensively investigated tolerance modeling and optimization [1, 2, 3]. However, few studies have specifically focused on tolerance modeling for bevel surfaces and their mating configurations with planar surfaces, nor have they comprehensively addressed tolerance optimization considering both reliability and cost. This paper aims to fill this gap by modeling geometric errors of bevel surfaces, developing an assembly error propagation model, and optimizing tolerance design for the spindle cutter disc component of a bevel gear milling machine.
2. Geometric Feature Error Modeling
2.1 Small Displacement Torsors (SDTs)
SDTs represent the infinitesimal motion of a rigid body in six degrees of freedom, comprising three rotations (α, β, δ) around the x, y, and z axes, and three translations (u, v, w) along these axes. The SDT vector can be expressed as t=(α,β,δ,u,v,w)T.
2.2 Cone Error Modeling
For a cone with a specified taper angle and diameter tolerance, the cone error can be modeled using SDTs. Considering a cone with a base radius R, height h, and taper ratio 1:n, the diameter tolerance TU and TL define the upper and lower bounds of the cone diameter, respectively.
The SDT for a cone element can be expressed as t=(0,0,0,u,0,0)T, where u represents the radial deviation from the ideal cone surface. The variation of the cone element can be mathematically described using equations derived from geometric relationships (see Appendix A for detailed equations).
3. Mating Surface Error Modeling
3.1 Cone-to-Cone Mating
Cone-to-cone mating involves two mating cones, where the actual axis of one cone aligns with the ideal axis of the other. The error propagation in cone-to-cone mating can be modeled similarly to cylinder-to-cylinder mating, with the cone axis deviations represented as cylinders. The error model for cone-to-cone mating can be expressed in matrix form (see Appendix B for details).
3.2 Cone-to-Plane Mating
Cone-to-plane mating involves a cone mating with a planar surface. The error propagation in this configuration can be analyzed by considering the relative deviations between the cone axis and the plane. The error model incorporates both cone axis deviations and plane deviations (see Appendix C for details).
4. Error Propagation Analysis
4.1 Serial and Parallel Mating
In serial mating, errors propagate sequentially through the mating sequence, with each mating interface contributing to the cumulative error. In parallel mating, errors propagate through multiple parallel paths, requiring an analysis of potential interference and adjustment of mating orientations to ensure successful assembly.
Table 1 summarizes the error propagation properties for various mating configurations.
Mating Type | Strong Constraints | Weak Constraints | No Constraints |
---|---|---|---|
Cone-to-Cone Gap | z, w | u, v | None |
Cone-to-Plane | z | u, v, w | None |
5. Monte Carlo Simulation for Error Variation
Monte Carlo simulation is used to determine the actual variation ranges of error parameters. Assuming normal distributions for error components, a large number of random samples are generated and filtered based on the constraint inequalities derived from the geometric error models. The resulting distributions of error parameters are analyzed using statistical methods.
6. Response Surface Methodology
Response surface methodology (RSM) is employed to establish functional relationships between the actual variation bandwidths of error parameters and the corresponding tolerances. A quadratic polynomial response surface model is constructed, and the coefficients are determined using the least squares method in MATLAB.
7. Assembly Precision Reliability Analysis
The assembly precision reliability is evaluated using Monte Carlo simulation. The system’s reliability function R(T) is calculated as the fraction of samples satisfying the prescribed assembly precision constraints.
8. Tolerance Optimization Model
8.1 Tolerance-Cost Function
The tolerance optimization model aims to minimize the total machining cost while satisfying assembly precision reliability and tolerance principles. The tolerance-cost function typically depends on the specific geometric features and machining processes. For simplicity, a generic tolerance-cost function is adopted here (see Appendix D for details).
8.2 Constraints
The optimization is constrained by:
- Assembly Precision Reliability: The assembly precision reliability must exceed a predefined threshold (e.g., 97%).
- Tolerance Principles: Shape tolerances should be less than position tolerances, which in turn should be less than dimensional tolerances.
9. Case Study: Spindle Cutter Disc Component of a Bevel Gear Milling Machine
9.1 Component Overview
The spindle cutter disc component of a bevel gear milling machine consists of a spindle, a cutter disc, and a housing. The primary mating interfaces include cone-to-cone, cone-to-plane, and cylinder-to-cylinder configurations.
9.2 Error Propagation Model
An error propagation model is developed for the spindle cutter disc component, considering the serial and parallel mating configurations. The model incorporates SDTs for cone, plane, and cylinder elements, as well as the error propagation matrices for mating interfaces.
9.3 Tolerance Optimization
The tolerance optimization model is applied to the spindle cutter disc component, with the objective of minimizing machining costs while maintaining assembly precision reliability above 97%. The optimization is performed using the particle swarm optimization (PSO) algorithm in MATLAB.
Table 2 shows the optimized tolerance values and the resulting cost reduction.
Tolerance Item | Original Value (mm) | Optimized Value (mm) |
---|---|---|
T1 (Cylinder Diameter) | 0.022 | 0.024 |
T2 (Cylinder Straightness) | 0.003 | 0.006 |
T3 (Cylinder Position) | 0.005 | 0.008 |
… | … | … |
Original Cost | 115.03 | Optimized Cost |
Cost Reduction | – | 8.36% |
10. Experimental Validation
An experimental validation is conducted using a laser scanner to acquire point cloud data of the assembled spindle cutter disc component. The experimental setup.
The experimental assembly errors are compared with the predicted errors from the simulation model. Table 3 summarizes the comparison results.
Error Direction | Simulated Maximum (mm) | Experimental Value (mm) |
---|---|---|
X-axis | 0.052 | 0.018 |
Y-axis | 0.043 | 0.0056 |
Z-axis | 0.009 | 0.0021 |
The experimental results confirm the validity of the proposed error propagation model, with the experimental errors falling within the predicted ranges.
11. Conclusion
This paper presents a comprehensive approach for modeling and optimizing assembly errors in the spindle cutter disc component of a bevel gear milling machine. By employing SDTs, Monte Carlo simulation, and RSM, accurate error models are developed for cone, plane, and cylinder features. An error propagation model is formulated for serial and parallel mating configurations, and a tolerance optimization model is proposed to minimize machining costs while ensuring assembly precision reliability. Experimental validation demonstrates the effectiveness of the proposed approach.