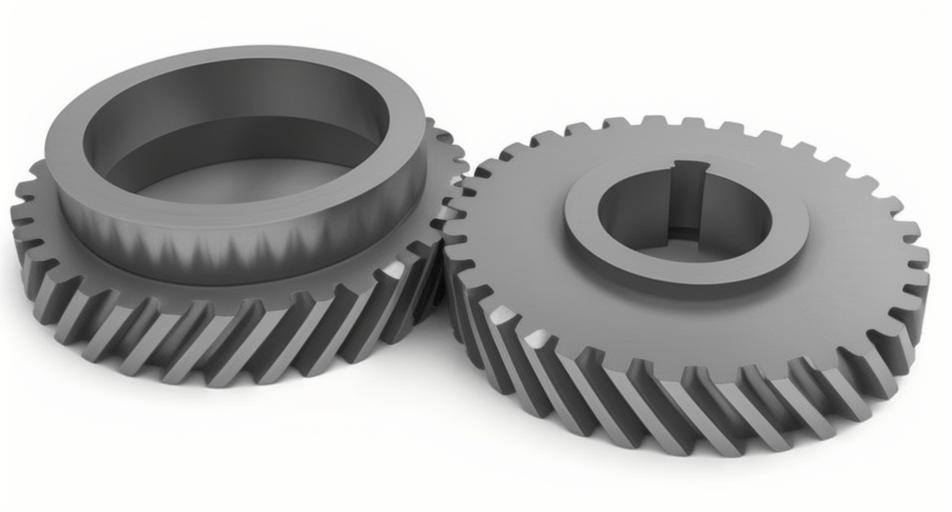
Helical gear is essential components in numerous industrial applications due to their high efficiency and ability to handle substantial loads smoothly. However, these gear is subject to wear and tear over time, which can lead to significant maintenance costs and operational downtimes. One effective way to enhance the wear resistance of helical gear is through various surface treatments. This article explores the impact of different surface treatments on the wear resistance of helical gear.
Surface Treatments for Helical Gear
- Nitriding: This heat treatment process diffuses nitrogen into the surface of the helical gear, creating a hard, wear-resistant layer. Nitriding improves fatigue strength and reduces wear significantly without the need for post-treatment machining.
- Carburizing: Carburizing involves adding carbon to the surface of helical gear and then quenching it to form a hard, wear-resistant outer layer while maintaining a tougher core. This treatment is beneficial for applications requiring high surface hardness and core toughness.
- Induction Hardening: This process involves heating helical gear surface using electromagnetic induction followed by rapid cooling (quenching). Induction hardening increases surface hardness, enhancing wear resistance and fatigue strength.
- Physical Vapor Deposition (PVD) Coating: PVD coatings, such as titanium nitride (TiN) or diamond-like carbon (DLC), are applied in thin layers to improve hardness and reduce friction. These coatings provide excellent wear resistance and extend gear life significantly.
- Chemical Vapor Deposition (CVD) Coating: Similar to PVD, CVD coatings involve depositing hard materials onto helical gear surface. CVD coatings offer superior wear resistance and are used in high-performance applications.
Comparative Analysis
To understand the effectiveness of these treatments, a comparative analysis was conducted using helical gear subjected to the same operational conditions. The following table summarizes the wear resistance improvement observed for each treatment.
Surface Treatment | Surface Hardness (HV) | Wear Resistance Improvement (%) | Fatigue Strength Improvement (%) |
---|---|---|---|
Nitriding | 900-1200 | 40-60 | 30-50 |
Carburizing | 700-850 | 50-70 | 40-60 |
Induction Hardening | 700-1000 | 30-50 | 20-40 |
PVD Coating (TiN) | 2000-2500 | 60-80 | 50-70 |
CVD Coating (DLC) | 3000-4000 | 70-90 | 60-80 |
Discussion
- Nitriding: Offers a good balance of surface hardness and wear resistance with moderate improvement in fatigue strength. It is particularly suitable for helical gear requiring consistent performance under cyclic loading.
- Carburizing: Provides substantial wear resistance and fatigue strength improvement. It is ideal for helical gear subjected to high stress and impact loads, combining a hard surface with a tough core.
- Induction Hardening: While it improves wear resistance and fatigue strength, it may not be as effective as nitriding or carburizing for applications requiring extreme hardness.
- PVD Coating: TiN coatings significantly enhance wear resistance and reduce friction, making them suitable for high-precision applications. However, the coating process can be expensive.
- CVD Coating: DLC coatings offer the highest wear resistance and fatigue strength improvement. They are ideal for extreme conditions but involve higher costs and complex application processes.
Conclusion
Surface treatments play a crucial role in enhancing the wear resistance of helical gear. Nitriding and carburizing are effective for balancing hardness and toughness, while PVD and CVD coatings provide superior wear resistance for high-performance applications. Selecting the appropriate surface treatment depends on the specific requirements of helical gear application, including load conditions, operational environment, and cost considerations.
By understanding the impact of these treatments, manufacturers can significantly extend the lifespan of helical gear, reduce maintenance costs, and improve overall system reliability.