Transmission principle of this kind of planetary transmission. According to its meshing characteristics, it belongs to NGW type, which is characterized by that the internal gear 3 is meshed with the sun gear 1 and the common planet gear 2. When the sun wheel rotates at high speed, the planetary wheel rotates between the sun wheel and the inner gear, and rotates around the sun wheel. The planet carrier outputs the low-speed revolution motion of the planet wheel. One of the structural forms of NGW type reducer.
According to the above structural principle, when the planetary carrier is used as the input shaft, it is the planetary speed increaser. It is one of the structure forms of planetary speed increaser, which is used for the speed increase of turbine compressor.
Therefore, the planet wheel can be in any relative position on the rotating frame (without aligning a specific tooth), and the rotor can be installed into the central wheel from the axial direction.
For such planetary transmissions without directional assembly requirements, they can be assembled according to the above requirements after disassembly during installation.
If the manufacturer adopts directional assembly in order to improve the meshing quality, the maximum (or minimum) radial runout of each planet wheel shall be placed on the same meshing position during the general assembly. During the disassembly, in order to not reduce the original meshing quality, the planet wheel shall be marked with meshing mark, and reassembled according to the mark.
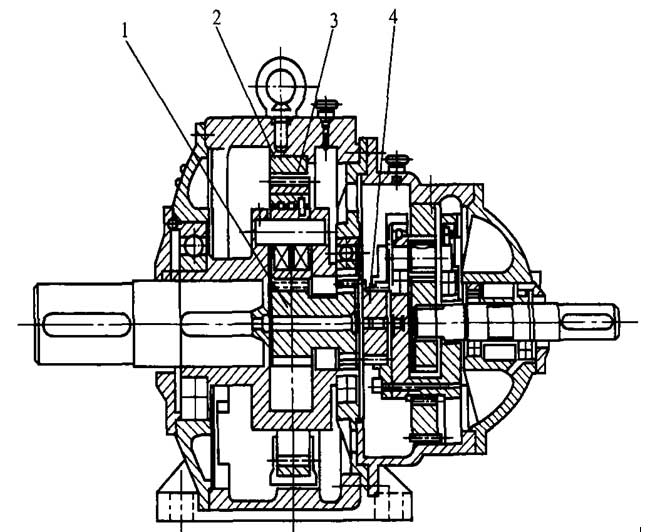
1.Assembly features
Because NGW planetary transmission has been designed to meet the following assembly conditions:
Z1 is the number of sun gear teeth;
Z3 – number of internal gear teeth;
U — number of planetary gears.
Therefore, the planet wheel can be in any relative position on the rotating frame (without aligning a specific tooth), and the rotor can be installed into the central wheel from the axial direction.
For such planetary transmissions without directional assembly requirements, they can be assembled according to the above requirements after disassembly during installation.
If the manufacturer adopts directional assembly in order to improve the meshing quality, the maximum (or minimum) radial runout of each planetary wheel shall be placed on the same meshing position during the general assembly, as shown in Figure 6-22. During the installation and disassembly, in order not to reduce the original meshing quality, the meshing marks shall be marked on each planetary wheel and reassembled according to the marks.
2.Inspection of backlash
The center distance of NGW planetary transmission is generally not adjustable, and the backlash is mainly guaranteed by the machining accuracy of each part and the reduction of tooth thickness. If it is necessary to check the side clearance, the lead pressing method can be used, which is the same as measuring the cylindrical gear.
When the sun gear and the inner ring gear adopt floating structure, if you want to measure the backlash, you should align and fix each floating part in the special tool before measuring.
When the inner ring gear is of non floating structure, in order to make the tooth side clearance between the inner ring gear and each planetary gear evenly distributed, when assembling the inner ring gear, housing and end cover after installation and disassembly, it should be assembled according to the original locating pin, otherwise, the coaxiality of each part and the inner ring gear should be corrected as much as possible.
3.Inspection of contact accuracy
The contact accuracy of gear is an important index to evaluate the quality of planetary gear transmission device, so attention should be paid to it during installation. The inspection method is the general coloring method. In order to facilitate identification, the planetary gears should be colored and inspected one by one to observe the contact with the sun gear and the inner gear ring. For the transmission with double-sided operation, check it in the positive and negative directions.
For high-speed planetary transmission, the contact accuracy of tooth surface is generally required to be no less than level 6.
4.Inspection of axial clearance
When one or more floating elements are in series in the gearbox, certain axial clearance shall be reserved between floating elements and non floating elements or between floating elements, generally 0.5-1mm. During installation, attention shall be paid to check and do not jack up to ensure the possibility of free adjustment of radial and axial positions.