Virtual assembly is to determine the relative position between models and complete model assembly through the reference and link relationship between parts. First, the solid models of the driven wheel and the driving wheel are established, and then the solid assembly is carried out according to the installation position. After assembly, interference analysis and meshing area inspection shall be carried out.
The specific assembly process of hypoid gear is to create a new file, enter the assembly module, first import the driven wheel, and then assemble according to the absolute position. Then install the driving wheel according to the theoretical assembly position x = – 86mm, y = 52.5mm z = – 30mm (where z = – 30mm is the offset distance of the driving wheel). Both the driving wheel and the driven wheel can rotate around their own axes until they are fully meshed and free from interference. The tangent constraint is added to the tooth surfaces in contact with each other to make them in contact. The assembled model is shown in the figure.
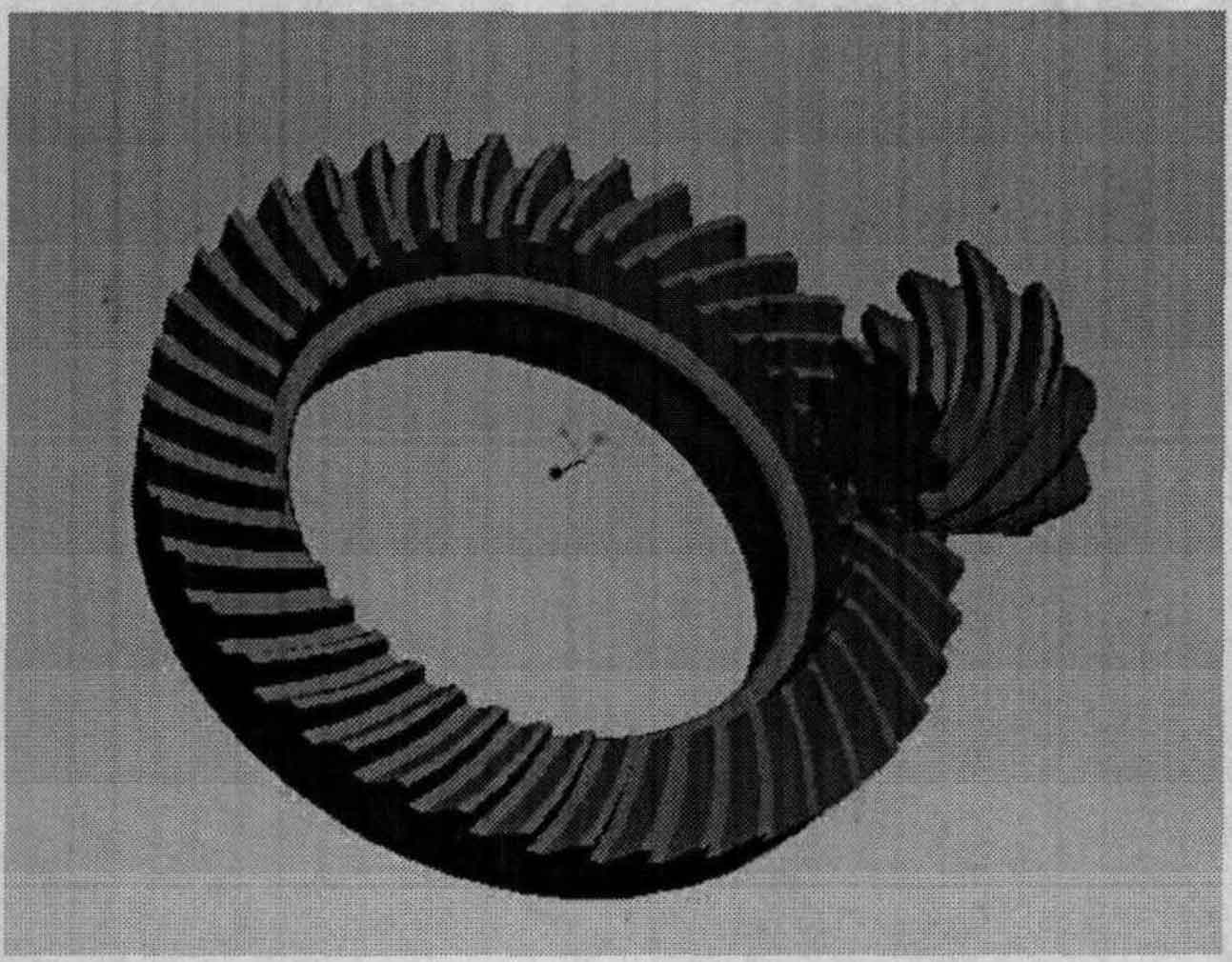
In the assembly model of Pro / E, interference inspection analysis can be performed. In the process of meshing and transmission of an aligned hyperboloid gear, if the assembly is not reasonable, interference may occur between the teeth: if two teeth collide with each other and are embedded, this will make the subsequent analysis not converge and the result is invalid. Therefore, it is very important to establish an accurate model and assembly, which is directly related to the accuracy of the results. Interference inspection is to evaluate the assemblability of hypoid gear pair. During the whole process of hypoid gear dynamic meshing, check whether there is interference between the driving wheel and the driven wheel, and whether the clearance size and assembly tolerance design are reasonable. Check whether the assembly path, assembly relationship and constraint conditions are reasonable and whether they can engage normally. Through the interference inspection of a hypoid gear, the results show that the two gears are in the process of meshing transmission Normal engagement without interference.
The above is a detailed process of hypoid gear entity modeling. Through the above steps, the hypoid gear modeling is completed. Then align the hyperboloid gear model for assembly and interference inspection analysis. The model is accurate and reliable. The theoretical model lays a foundation for finite element analysis.