After meshing, the preprocessing file is imported into ABAQUS and set as follows:
(1) Material definition: the material parameters of the big and small wheels are set according to the steel material. The young’s modulus is 2.06 × 108kpa, the material density is 7.8 × 10-3kg / mm3, and Poisson’s ratio is 0.3.
(2) Define assembly: assemble according to the assembly parameters obtained in the above assembly coordinate system. The assembly diagram of the big and small wheels is shown in Figure 1
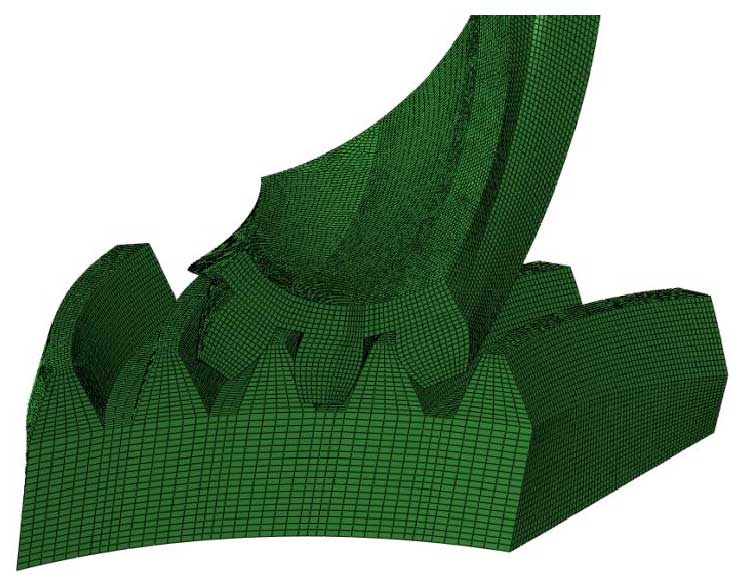
(3) Define the analysis step: the analysis step is defined as the dynamic explicit general analysis step. The analysis step time is set to 2 seconds, and the appropriate mass amplification factor is selected (the value of the mass amplification factor is based on the performance of the computer itself. The smaller the value is, the more reasonable it is, but the longer the calculation time is). The algorithm of dynamic explicit general analysis step is based on dynamic equation, and the analysis and calculation process does not need iteration and has good stability.
(4) Define the output of field variables and historical variables: change the average time interval frequency in the output of field variables to 100 (the larger the value of the average interval frequency, the higher the frequency of output, the better the continuity of output animation, but the more disk space is occupied); set the stress, contact, displacement, etc. of field variable output, and set contact of historical variable output.
(5) Definition of contact: firstly, contact attribute is defined, normal behavior is defined as hard contact, friction coefficient of tangential behavior is defined as 0.1, and penalty function is selected for friction formula; secondly, contact control is defined and contact control type is selected as ABAQUS Secondly, the contact pair is defined, in which the initial analysis step is selected, the contact type is explicit solver, and the contact pair of small wheel and large wheel is defined by the face-to-face contact algorithm of display solver. The concave convex surface of the small wheel and the large wheel as well as the continuous surface of the tooth root and tooth top are selected and defined as the driving surface and the driven surface respectively, The contact attributes and contact control are defined before; finally, the constraint is defined, and any point on the axis of the small wheel and the large wheel is taken as the rotation center, and the point is set as the reference point for coupling dynamic constraints between the inner ring of the small wheel and the inner ring of the large wheel, so that the boundary and load can be directly applied to the set reference point. The tooth contact definition is shown in Figure 2

(6) The boundary conditions and loads are defined: the rotation of the big wheel and the small wheel is not constrained. In order to make the big wheel and the small wheel rotate around their own axis, the resistance moment of the big wheel is set to 1500kgmm2 / S2 (the resistance moment is the load on the big wheel, and the rotation speed of the small wheel is set as 2 mm / s, both the big wheel and the small wheel are loaded by the smooth amplitude curve, which can avoid the sudden change of load, and is conducive to establish the stable contact relationship between the big wheel and the small wheel.