For the hypoid gear in the automobile drive axle, the previous research mainly focused on simulating the machining process of the hypoid gear to obtain the high-precision outer profile of the hypoid gear, optimizing the geometric parameters of the hypoid gear and the machining parameters of the machine through the geometric contact analysis of the hypoid gear, and then calculating the stress, load distribution and transmission error of the hypoid gear tooth root through the static finite element method, However, these calculation results can not fully reflect the vibration and noise response of the gear system during the meshing process of hypoid gears. Many fretful hypoid gear meshing noise problems still exist in the vehicle drive axle.
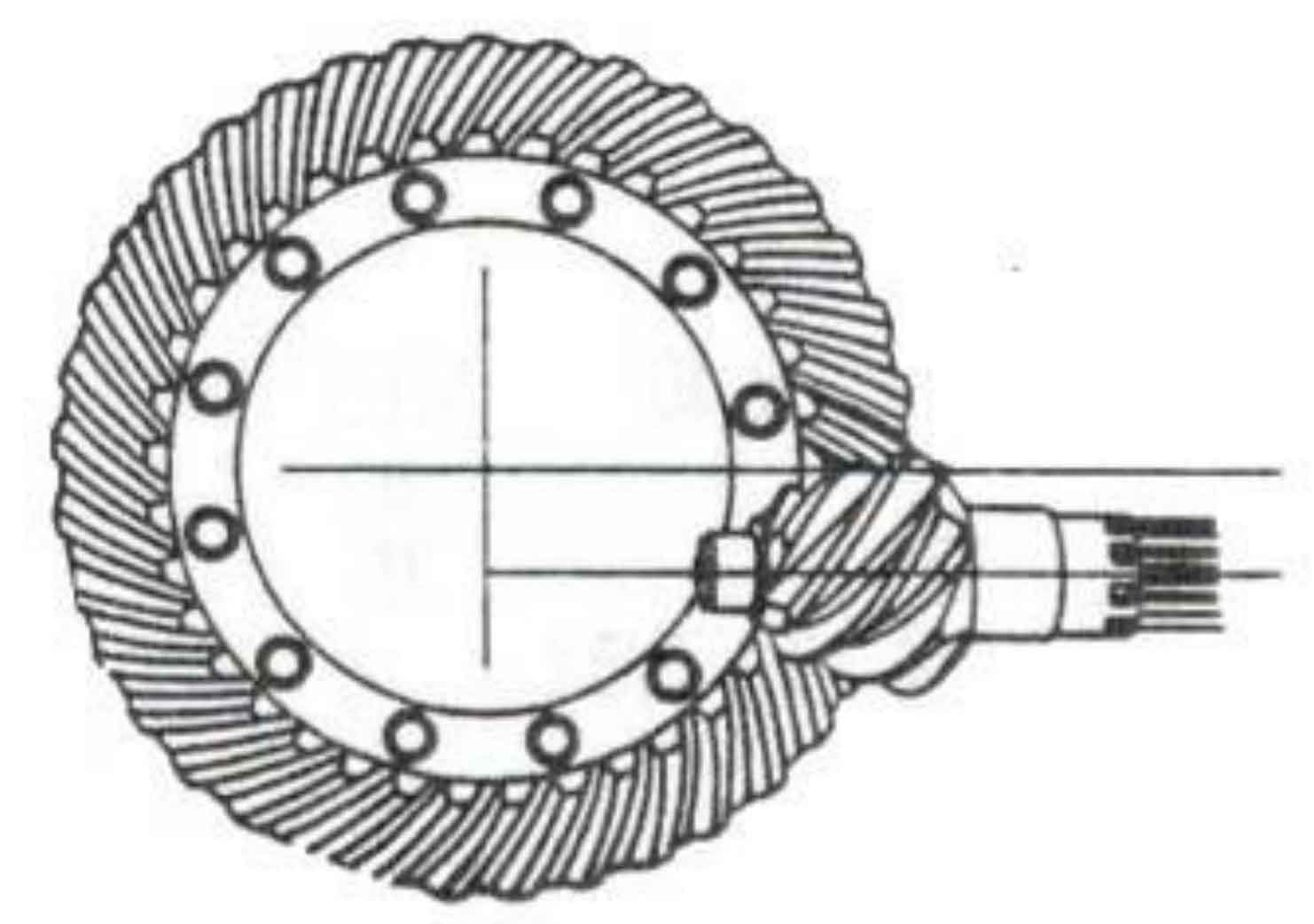
Therefore, many researchers have established the dynamic response mathematical model of the hypoid gear system, studied the influence of the stiffness, damping and inertia mass of each component in the hypoid gear system on the dynamic system of the hypoid gear, and established the relationship between the static analysis of the hypoid gear and the dynamic response of the system through the meshing stiffness. In the establishment of the hypoid gear dynamics system, the biggest difference between the hypoid gear and the spur gear is the gear meshing stiffness. This is because the direction of the meshing force of the spur gear remains basically unchanged during meshing. There are relatively mature calculation methods and empirical formulas, but the geometric shape and meshing process of the hypoid gear are complex, During the meshing process of hypoid gears, the direction of meshing force and the position of meshing point change with the change of gear rotation angle and loading force. Compared with spur gears, the meshing stiffness of such gears is less studied.
In the past, the meshing model of hypoid gears was based on empirical design formula or gear geometric meshing analysis. With the improvement of gear design and analysis requirements, the contact analysis of hypoid gears put forward higher requirements. In this section, a complete time-varying stiffness calculation method of hypoid gears is established. The static finite element model of hypoid gears is established based on the real gear contact to simulate the real operation process of gears. The time-varying meshing stiffness of hypoid gears is obtained by post-processing the finite element calculation results.