Gear transmission system mainly has 4 different lubrication states, including elastohydrodynamic lubrication, mixed lubrication, boundary lubrication and dry friction.The friction coefficient of tooth surface is different under different lubrication conditions.
1. Calculation of Friction Factor under Elastohydrodynamic Lubrication
In actual operating conditions, relative sliding speed, lubricant viscosity and other factors will affect the friction coefficient, which also becomes a function of time t.It is known from literature [15] 846-846 that the friction coefficient of tooth surface at any engagement point of main and driven wheels under ejection-hydrodynamic lubrication is.

F (s (t), Fhzi (t), Fhzi (t), 950, Sav) =b1+b4|s (t) |s (t) |Fhzi (t) |Fhzi (t) |Fhzi (t) lg0+b5e-|s (t) |Fhzi (t) lg0+b9eSav, b1-b9 are empirical regression coefficients; Fhzi (t) lg0+b9eSav, b1-b9 are empirical regression coefficients; 0 is dynamic viscosity coefficient of lubricating oil; Sav average surface roughness, mm; s (t) is average surface roughness, mm; s (mm; s (Hertz contact stress of driven wheel with Fhzi(t) dominant
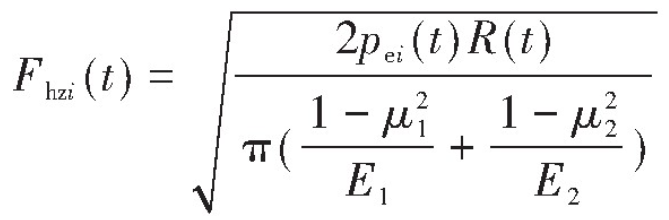
In this formula, the normal load per unit tooth width of driven wheels with pei(t) dominant is calculated as N/m.

In the formula, T is torque, N_m; Bi is main and driven gear tooth width is m M.
Average tooth surface roughness Sav is
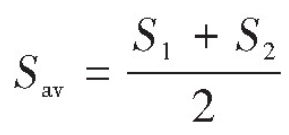
In the equation, S1 and S2 are respectively the roughness of the tooth surface of the primary and secondary gears.
The radius of curvature R(t) is
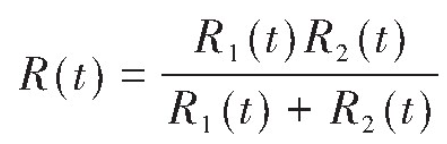
Relative sliding speed vs(t) and entrainment speed ve(t) are respectively
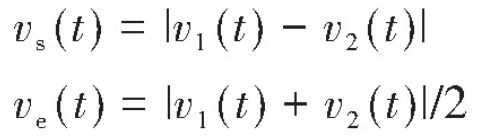
The roll-slip ratio s(t) is
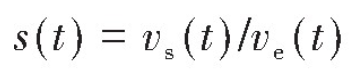
The empirical regression coefficient is b1=-8.916 465, b2=1.033 030, b3=1.036 077, b4=-354 068, b5=2.812 084, b6=-0.100 601, b7=0.752 755, b8=-0.390 958, b9=0.620 305.
2. Calculation of friction coefficient under mixed lubrication
The expression of the friction coefficient umi(t) of the tooth surface at any engagement point of the main and driven wheels under mixed lubrication is as follows:
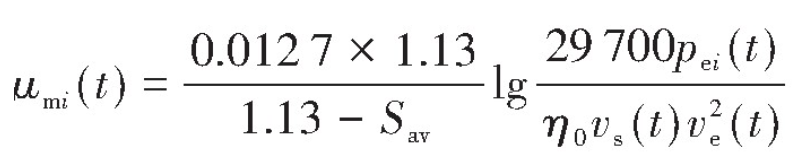
3. Calculation of friction coefficient under boundary lubrication
The expression of the friction coefficient of the tooth surface at any engagement point of the main and driven wheels under the boundary lubrication state is as follows:

In the formula, MUAV is the average friction coefficient; _is the adjustment factor, and 50 is usually taken to satisfy the smoothness of the curve; _is the gear ratio; Xi (t) is the periodic displacement of the meshing gear secondary and driven wheels, and its calculation formula is as follows:

In the formula, the indexing circle radius of ri-dominated and driven wheels is mm.
4. Calculation of friction coefficient under dry friction condition
The dry friction coefficient of the contact surface of the gear can be measured by measurement. Generally, the dry friction coefficient of the tooth surface in the gear drive is in the range of 0.1-0.5, where the friction coefficient of the tooth surface is mud=0.4.