Transmission error is an important index of gear transmission performance. Transmission error refers to the difference between the actual position and the ideal position of the passive output gear. The ideal position refers to the position of the driven gear when the master and slave gears are both ideal involute tooth profile and have no elastic deformation. According to the model established in Section 2, the finite element analysis is carried out, and the transmission error curves of the gear pair under four groups of twist coefficients are extracted. As shown in Figure 1, with the increase of the tooth surface distortion coefficient, the transmission error decreases as a whole, and the maximum peak value decreases from 12.83 μ m to 10.79 μ m, which is reduced by 15.90%. It is generally believed that gear transmission error is the source of vibration and noise of gear system. Therefore, the transmission error can be effectively reduced by improving the tooth surface distortion, which is conducive to the vibration and noise reduction of helical gear.
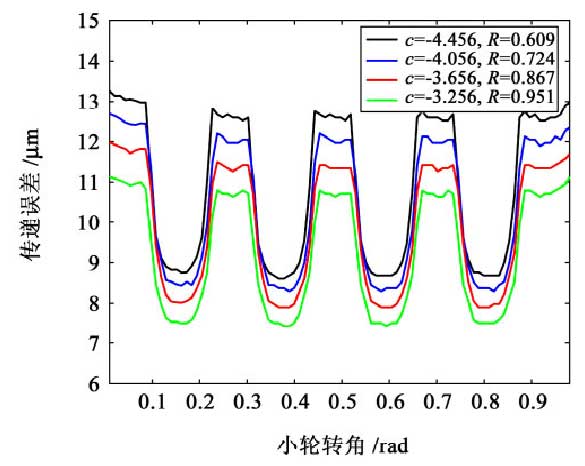
Meshing stiffness is the ability of tooth to resist deformation during gear meshing. Different from other elastic systems, gear transmission system will not only produce dynamic response due to external excitation, but also change the meshing stiffness due to the change of the number of meshing teeth, the elastic deformation of gear teeth and the error of gear teeth in the transmission process, resulting in the dynamic meshing force of teeth. The dynamic excitation caused by the time-varying meshing stiffness is one of the most important dynamic excitation forms in gear transmission. As shown in Fig. 2, with the increase of twist coefficient, the tooth surface twist decreases and the meshing stiffness increases. The peak value increases from 1.829 × 108 to 2.118 × 108, increasing by 15.80%.
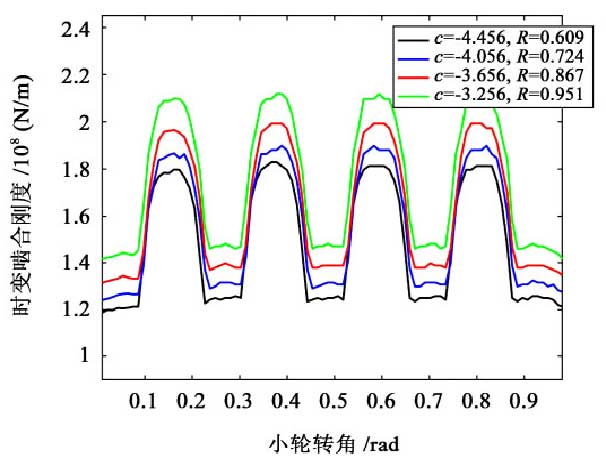
The biggest purpose of tooth alignment modification is to improve the edge contact and maximum contact stress. There is no edge contact, so only the maximum contact stress is considered. According to the calculation results of finite element model, the maximum contact stress of the third tooth with stable meshing period is extracted, as shown in Fig. 3. The maximum contact stress decreases with the increase of tooth surface distortion coefficient, and the peak value decreases from 1498.81 MPa to 1283.12 MPa, which decreases by 14.39%. At the same time, the contact stress which has a great influence on the meshing of gears is also reduced obviously, and the bearing capacity of helical gears is obviously improved.
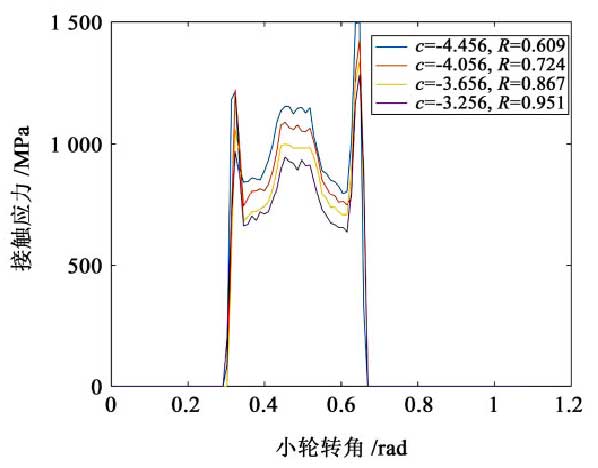