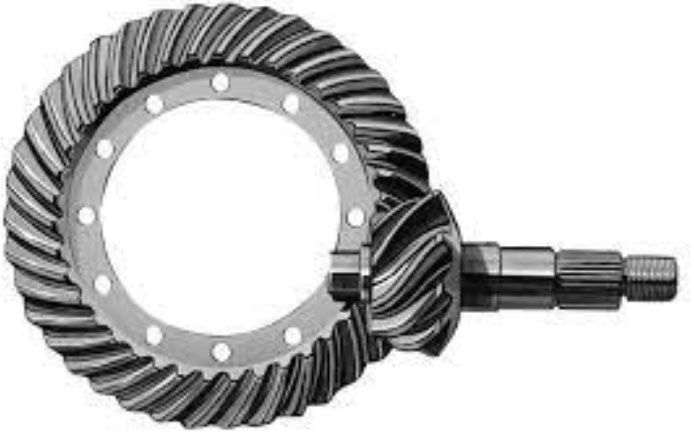
Introduction
Hypoid gear is critical component in many automotive and industrial applications due to their ability to transfer power between non-parallel shafts efficiently. Despite their advantages, hypoid gear is prone to various failure modes if not properly designed, manufactured, or maintained. This article presents case studies of hypoid gear failures, highlights the lessons learned from these incidents, and outlines preventative measures to avoid similar issues in the future.
Case Study 1: Gear Tooth Pitting in Automotive Differentials
Incident Overview
A major automotive manufacturer experienced frequent gear tooth pitting in the hypoid gear of their vehicle differentials. The issue led to increased noise, vibration, and eventual gear failure.
Failure Analysis
- Root Cause: Insufficient lubrication and improper gear alignment were identified as the primary causes of pitting.
- Consequences: The pitting accelerated wear and compromised hypoid gear tooth surface, leading to early failure.
Lessons Learned
- Lubrication: Adequate lubrication is essential to prevent surface wear and pitting. The use of high-quality lubricants with appropriate viscosity is critical.
- Gear Alignment: Ensuring proper hypoid gear alignment during assembly can significantly reduce the risk of uneven load distribution and surface wear.
Preventative Measures
- Implement regular maintenance schedules to check and replenish lubricants.
- Use advanced alignment tools and techniques during hypoid gear assembly to ensure precise alignment.
- Conduct routine inspections to detect early signs of pitting and address them promptly.
Case Study 2: Fatigue Cracks in Industrial Gearboxes
Incident Overview
An industrial gearbox manufacturer faced recurrent fatigue cracks in the hypoid gear used in heavy machinery, leading to unexpected downtime and costly repairs.
Failure Analysis
- Root Cause: High cyclic loads and improper heat treatment were found to be the main factors contributing to fatigue cracks.
- Consequences: The fatigue cracks propagated over time, leading to catastrophic hypoid gear failure under operational loads.
Lessons Learned
- Load Management: Understanding and managing the operational loads can help in designing gear that withstand high cyclic stresses.
- Heat Treatment: Proper heat treatment processes are crucial to enhancing the fatigue resistance of hypoid gear.
Preventative Measures
- Perform detailed load analysis during the design phase to ensure hypoid gear can handle expected operational loads.
- Implement stringent quality control measures for heat treatment processes to achieve optimal hardness and toughness.
- Use advanced materials and coatings to enhance fatigue resistance.
Case Study 3: Gear Tooth Scuffing in Marine Applications
Incident Overview
A marine equipment supplier encountered severe gear tooth scuffing in the hypoid gear of their propulsion systems, resulting in reduced efficiency and increased maintenance costs.
Failure Analysis
- Root Cause: The scuffing was attributed to high surface temperatures and inadequate lubrication under heavy loads.
- Consequences: The scuffing caused surface damage, increasing friction and leading to rapid gear wear.
Lessons Learned
- Thermal Management: Effective thermal management can prevent excessive surface temperatures that contribute to scuffing.
- Lubrication Under Load: Ensuring adequate lubrication under varying load conditions is essential to prevent scuffing.
Preventative Measures
- Use lubricants specifically designed for high-load and high-temperature conditions.
- Implement cooling systems or materials that enhance heat dissipation from hypoid gear surface.
- Regularly monitor operating conditions to ensure lubrication efficacy and prevent overheating.
Case Study 4: Corrosion in Agricultural Machinery
Incident Overview
An agricultural machinery manufacturer experienced significant corrosion issues in the hypoid gear used in their equipment, leading to gear degradation and failure.
Failure Analysis
- Root Cause: Exposure to harsh environmental conditions and the use of inappropriate materials were identified as the main causes of corrosion.
- Consequences: Corrosion weakened hypoid gear structure, leading to increased wear and eventual failure.
Lessons Learned
- Material Selection: Choosing materials with inherent corrosion resistance is vital for applications exposed to harsh environments.
- Protective Coatings: Applying protective coatings can provide an additional barrier against corrosive elements.
Preventative Measures
- Select corrosion-resistant materials such as stainless steel or appropriately treated alloys.
- Apply protective coatings like zinc or phosphate to enhance corrosion resistance.
- Design maintenance protocols that include regular cleaning and inspection to mitigate the effects of corrosion.
Comparative Analysis of Failure Modes and Preventative Measures
Failure Mode | Root Cause | Consequences | Preventative Measures |
---|---|---|---|
Gear Tooth Pitting | Insufficient lubrication, misalignment | Increased wear, noise | Regular maintenance, high-quality lubricants, precise alignment |
Fatigue Cracks | High cyclic loads, improper heat treatment | Catastrophic failure | Load analysis, quality heat treatment, advanced materials and coatings |
Gear Tooth Scuffing | High surface temperatures, inadequate lubrication | Surface damage | High-load lubricants, thermal management, operational condition monitoring |
Corrosion | Harsh environment, inappropriate materials | Gear degradation | Corrosion-resistant materials, protective coatings, regular cleaning |
Conclusion
Understanding the root causes of hypoid gear failures through detailed case studies provides valuable insights for improving gear design, manufacturing, and maintenance practices. By implementing the lessons learned and adopting effective preventative measures, engineers can enhance the reliability, performance, and longevity of hypoid gear systems across various applications. Regular monitoring, precise manufacturing, proper lubrication, and material selection are key strategies to mitigate the risks of gear failure and ensure optimal operation.