Noise reduction in helical gear transmissions is a significant consideration, especially in industries where gear noise can impact overall equipment performance, user comfort, or adherence to regulatory standards. Here are some key strategies for reducing noise in helical gear systems:
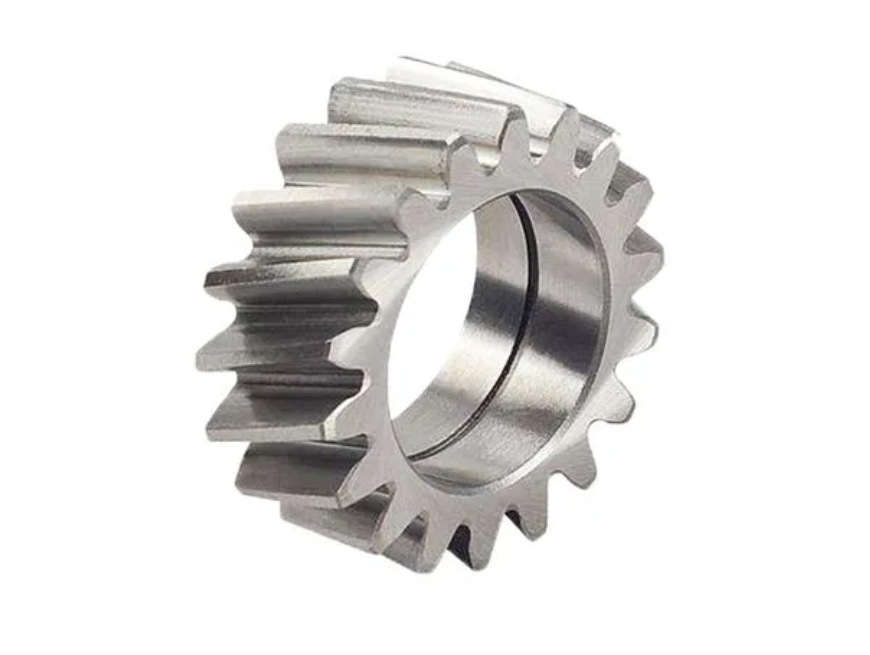
1. Precision Gear Design and Manufacturing
- Optimized Tooth Profile: Designing tooth profiles with specific modifications to reduce peak stress and even out the load distribution.
- High-Precision Manufacturing: Ensuring helical gear is manufactured with high precision to minimize errors in tooth form, helix angle, and pitch, which can cause noise.
2. Gear Material and Heat Treatment
- Advanced Materials: Using high-quality, durable materials for helical gear to reduce wear and deformation.
- Heat Treatment Processes: Such as case hardening or nitriding, to enhance surface hardness and longevity of helical gear.
3. Surface Finishing and Coating
- Microfinishing: A process that smooths the tooth surface to minimize friction and vibration.
- Coating Techniques: Applying advanced coatings (e.g., diamond-like carbon) to reduce friction and wear, thereby lowering noise levels.
4. Lubrication Strategies
- High-Quality Lubricants: Using lubricants that provide a stable film between gear teeth, minimizing metal-to-metal contact.
- Proper Lubrication Management: Ensuring consistent and adequate lubrication to reduce friction and wear.
5. Gear Alignment and Mounting
- Accurate Alignment: Proper alignment of helical gear shafts to avoid misalignment that can cause noise.
- Rigid Mounting: Secure and precise mounting of helical gear and bearings to prevent vibrations and noise due to movement.
6. Noise Damping and Isolation
- Damping Materials: Incorporating materials that absorb vibrations into helical gear housing.
- Isolation Techniques: Designing mounts or enclosures to isolate helical gear system from the rest of the machinery, preventing noise transmission.
7. Advanced Tooth Meshing Techniques
- Helix Angle Optimization: Adjusting the helix angle for better load distribution and smoother meshing.
- Double-Helical or Herringbone Gears: Using these designs to counterbalance axial forces and reduce vibrations.
8. Dynamic Analysis and Simulation
- Finite Element Analysis (FEA): Simulating helical gear performance to identify and mitigate potential noise issues.
- Dynamic Modeling: Using sophisticated software to model and analyze helical gear dynamics, enabling noise prediction and reduction strategies to be implemented during the design phase.
9. Addressing Environmental Factors
- Soundproof Enclosures: Encasing helical gear system in a soundproof housing.
- Ambient Noise Reduction: Implementing broader noise control measures in the operating environment.
Conclusion
The strategy for noise reduction in helical gear transmissions depends on various factors, including the specific application, operational parameters, and environmental conditions. A combination of these strategies is often used to achieve the desired noise reduction level while maintaining gear performance and durability. Advances in helical gear design, materials science, lubrication, and noise damping technologies continue to improve the ability to reduce noise in helical gear systems effectively.