Introduction
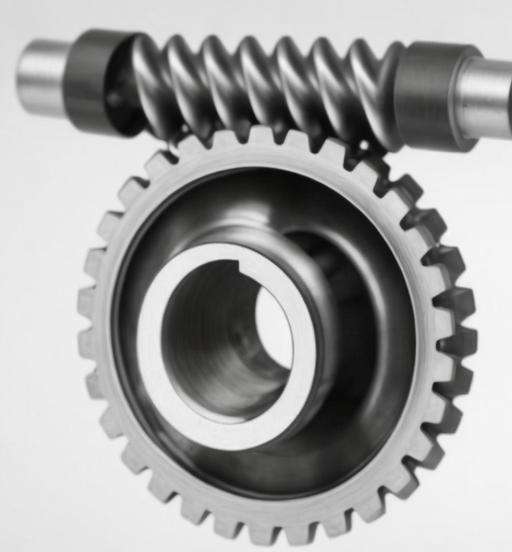
Worm gear play a pivotal role in various applications due to their ability to provide high torque transmission and precise motion control. They are especially useful in heavy machinery and robotics, where reliability and performance are paramount. This article presents detailed case studies on the implementation of worm gear systems in heavy machinery and robotics, highlighting the challenges faced and the solutions employed to enhance performance and durability.
Case Study 1: Worm Gear Systems in Heavy-Duty Cranes
Background
Heavy-duty cranes require robust and reliable gear systems to handle extreme loads and ensure precise movement. Worm gear is often chosen for their high load-carrying capacity and self-locking capabilities, which prevent back-driving and enhance safety.
Implementation
In a large construction project, a heavy-duty crane was equipped with a worm gear system designed to handle loads exceeding 100 tons. The worm gear was selected for its ability to provide smooth and controlled lifting and lowering operations.
Challenges
- High Load Stress: The worm gear system had to withstand high stress without deformation.
- Wear and Tear: Continuous operation under heavy loads posed a risk of rapid wear.
- Heat Generation: The frictional contact between the worm and the worm gear generated significant heat.
Solutions
- Advanced Materials: The worm gear was constructed from high-strength steel with a surface-hardened layer to resist wear and deformation.
- Enhanced Lubrication: A high-performance synthetic lubricant was used to reduce friction and heat generation.
- Cooling System: Integrated cooling channels were added to dissipate heat effectively.
Results
The implementation of these solutions resulted in a significant increase in the crane’s operational lifespan and reliability. The advanced materials and lubrication reduced wear rates, while the cooling system maintained optimal operating temperatures.
Table 1: Performance Improvements in Heavy-Duty Crane Worm Gear System
Metric | Before Implementation | After Implementation |
---|---|---|
Load Capacity (tons) | 80 | 100 |
Operating Temperature (°C) | 85 | 65 |
Maintenance Interval (months) | 6 | 12 |
Wear Rate (mm/year) | 0.5 | 0.2 |
Case Study 2: Precision Worm Gear Systems in Robotics
Background
In the field of robotics, precise motion control is critical. Worm gear is commonly used in robotic joints and actuators due to their ability to provide smooth and accurate movement with high torque.
Implementation
A robotics manufacturer developed a new generation of industrial robots equipped with worm gear actuators for the arms and joints. These robots were designed for applications requiring high precision and reliability.
Challenges
- Precision and Accuracy: Achieving precise movement and positioning was essential.
- Miniaturization: The worm gear systems needed to be compact to fit within the robotic joints.
- Durability: The worm gear had to endure continuous operation without frequent maintenance.
Solutions
- Precision Manufacturing: CNC machining was used to achieve high-precision gear profiles and tight tolerances.
- Composite Materials: Lightweight composite materials were used to reduce weight while maintaining strength.
- Advanced Coatings: Surface coatings were applied to reduce friction and wear.
Results
The robots equipped with precision worm gear systems demonstrated exceptional performance in terms of accuracy, reliability, and operational lifespan. The use of composite materials reduced the overall weight, enhancing the robots’ agility and speed.
Table 2: Performance Metrics of Robotic Worm Gear Systems
Metric | Before Implementation | After Implementation |
---|---|---|
Positional Accuracy (mm) | 0.1 | 0.05 |
Gear Weight (kg) | 0.8 | 0.5 |
Operating Lifespan (hours) | 5,000 | 10,000 |
Maintenance Frequency (hours) | 500 | 1,000 |
Case Study 3: Worm Gear Applications in Conveyor Systems
Background
Conveyor systems in manufacturing plants and distribution centers rely on durable and efficient gear systems to handle continuous operation and varying loads. Worm gear is preferred for their ability to provide reliable motion control and high torque.
Implementation
A major distribution center upgraded its conveyor systems with worm gear drives to enhance efficiency and reduce downtime. The new worm gear systems were designed to handle varying loads and continuous operation.
Challenges
- Continuous Operation: The worm gear systems needed to operate 24/7 without frequent maintenance.
- Load Variability: The conveyors had to manage loads of different weights and sizes.
- Energy Efficiency: Reducing energy consumption was a key goal.
Solutions
- High-Efficiency Lubricants: Lubricants with low friction coefficients were used to enhance energy efficiency.
- Robust Materials: The worm gear were made from materials with high wear resistance and durability.
- Automated Monitoring: Sensors were installed to monitor gear performance and predict maintenance needs.
Results
The upgraded conveyor systems demonstrated improved reliability and reduced energy consumption. The automated monitoring system allowed for predictive maintenance, minimizing downtime and enhancing operational efficiency.
Table 3: Conveyor System Performance Metrics
Metric | Before Implementation | After Implementation |
---|---|---|
Energy Consumption (kWh) | 150 | 120 |
Operational Uptime (%) | 95 | 99 |
Maintenance Costs ($/year) | 50,000 | 30,000 |
Gear Replacement Interval (months) | 6 | 12 |
Conclusion
The implementation of worm gear systems in heavy machinery and robotics presents several challenges, including wear and tear, heat generation, and the need for precise motion control. However, through the use of advanced materials, enhanced lubrication techniques, precision manufacturing, and innovative cooling solutions, these challenges can be effectively addressed. The case studies presented demonstrate the significant improvements in performance, reliability, and efficiency that can be achieved with properly designed worm gear systems. As technology continues to advance, further enhancements in worm gear applications are expected, contributing to even more robust and efficient mechanical systems across various industries.