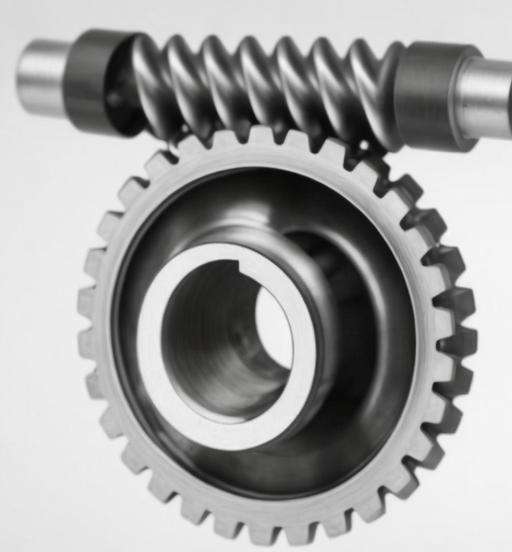
Abstract:
This paper proposes an optimization method based on the dual interlocking circular cutters (DICC) machining of straight bevel gears to minimize the transmission error fluctuation amount, aiming to improve their meshing performance. By introducing tool modification coefficients, average cutter radius, and blade angle, a tooth surface model considering tooth profile and tooth length modification is established. An optimization model targeting the symmetry of geometric transmission error and the minimization of load transmission error fluctuation is then formulated and solved using genetic algorithms. The results show a significant reduction in transmission error fluctuation, enhancing the gear pair’s performance.
1. Introduction
Straight bevel gears are widely used in aviation, aerospace, and automotive fields due to their simple structure, low axial force, and ease of installation. However, traditional manufacturing methods cannot meet the high-strength, low-noise, and high-reliability requirements of modern drives, necessitating exploration of new manufacturing techniques. This paper introduces a high-efficiency method using DICC for milling/grinding straight bevel gears, aiming to improve processing accuracy and efficiency.
2. Machining Principle of Dual Interlocking Circular Cutters
2.1 Tool Positioning
The coordinate systems involved in tool positioning are illustrated in Table 1, including the tool normal section reference coordinate system (Sm), the tool moving coordinate system (Sn), and the transformation between them.
Table 1: Coordinate Systems for Tool Positioning
Symbol | Description |
---|---|
Sm | Tool normal section reference coordinate system |
Sn | Tool moving coordinate system |
r(Q)m | Position vector of the cutting point Q in Sm |
u | Position vector pointing from Om to any point on the tool cutting edge |
u0 | Origin position of the parabolic modification curve |
at | Parabolic modification coefficient of the tool tooth profile |
2.2 Tooth Surface Generation
The position vector of the tooth surface generated by the DICC is obtained through coordinate transformation. The coordinates involved in the generation process are shown in Table 2.
Table 2: Coordinates in Tooth Surface Generation
Symbol | Description |
---|---|
Scg | Crown generating wheel coordinate system |
Scd | Dual interlocking circular cutter reference coordinate system |
rOcd | Position vector of the cutter center in Scg |
Mcg,cd | Homogeneous transformation matrix from Scd to Scg |
γi | Pitch cone angle of the gear being processed |
3. Mathematical Model of Straight Bevel Gear with Modification
A mathematical model considering tooth profile and tooth length modifications is established by introducing tool modification coefficients, average cutter radius (ρm), and blade angle (δ). The relationships among these parameters and their influence on the gear tooth surface are analyzed.
4. Optimization Design
The ideal geometric transmission error curve should be a downward-opening parabola, with cross-continuous and symmetrically positioned tooth pairs. The optimization process aims to minimize the load transmission error fluctuation.
4.1 Objective Function
The objective function for optimization is to minimize the load transmission error amplitude (ΔTe) after modification, as shown in the equation below:
4.2 Optimization Variables
The optimization variables include the tool modification coefficient (at), blade angle (δ), and average cutter radius (ρm).
4.3 Optimization Process
Genetic algorithms are employed for optimization due to the complexity and non-linearity of the problem. The optimization process involves encoding, initial population generation, fitness evaluation, selection, crossover, and mutation.
5. Results and Analysis
5.1 Comparison of Tooth Surface Marks
The tooth surface marks before and after optimization are compared, showing a reduction in the contact area due to tooth length modification.
5.2 Transmission Error Analysis
The geometric transmission error curve after optimization is basically symmetrical, avoiding edge contact under medium and light loads. The load transmission error amplitude decreases by 56.54%, effectively reducing vibration and noise.
6. Conclusion
- A mathematical model for straight bevel gears considering tooth profile and tooth length modifications is established.
- The tool modification coefficient significantly affects the geometric and load transmission errors, while the blade angle and average cutter radius mainly influence the contact area.
- By optimizing these parameters using genetic algorithms, the load transmission error fluctuation is effectively reduced, enhancing the gear pair’s performance.