Based on the acceleration signal of the key parts measured under typical working conditions, the dynamic stress response on the surface of the gearbox and the modal analysis of the gearbox, the fatigue cracking mechanism of the gearbox is studied.
(1) The fatigue crack starts at the corner of the inner surface of the gear box, where there is a stress concentration phenomenon, accompanied by defects such as porosity and pit, which reduces the bearing capacity of the gear box structure.
(2) The results show that the acceleration signal and dynamic stress response of axle box and gear box have higher vibration energy points at the frequencies of 575 Hz (high speed), 362 Hz and 632 Hz (low speed), respectively, and the frequencies of 575 Hz (high speed) and 362 Hz (low speed) are the line excitation frequency related to the train operation speed.
(3) The first two natural frequencies of the gearbox are 580 Hz and 635 Hz respectively, and the first and second natural frequencies of the gearbox are the same when the train running speed is 303 km / h and 190 km / h, which shows that the external excitation of the gearbox has intersection with its natural frequency, and the gearbox has resonance phenomenon.
(4) When the train is running in a high-speed straight line, the lateral acceleration response caused by the line excitation is more intense than that caused by the vertical acceleration. The local stress direction caused by the lateral acceleration is perpendicular to the crack surface, and the dynamic stress amplitude of the gear box is far greater than that in the low-speed stage. Therefore, the track excitation caused by the train running in a high-speed straight line causes the resonance of the gear box structure, resulting in the local high stress amplitude, It is the main cause of fatigue cracking of the box body.
1. Fatigue source analysis
The finite element simulation analysis of the gearbox is carried out, and the analysis results are shown in the figure.
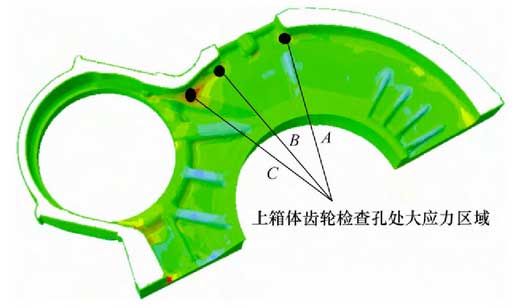
From the simulation analysis, it is known that the greater stress area of the upper box is the transition area between the vertical plate and the upper cover plate, where a is the crack initiation part of the fatigue crack of the cracked gear box, which is located at the inner corner of the box.
From the macro fracture analysis of the gearbox, it is known that there are casting defects such as casting pits and air holes at the crack fatigue source, resulting in local stress concentration of the structure; from the stress point of view, when the gearbox bears the transverse load generated from the axle, the local stress state of the fatigue source is related to the bearing installation mode on both sides of the big gear, The face to face mode is adopted for the bearing installation in the gearbox system.
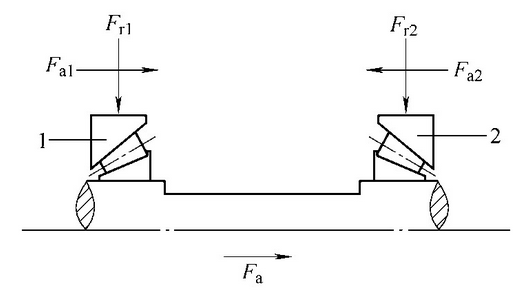
When the tapered roller bearing is installed face-to-face, its axial stress feature is that when it moves axially to the right, its load mainly acts on the right bearing. Therefore, when the gear box bears the transverse load, the fatigue source inside the box mainly bears the tensile stress.
2. Resonance fatigue
In the running state of high-speed EMU, the resonance fatigue phenomenon will occur when the wheel rail excitation frequency coincides with the natural frequency of the gearbox. Therefore, the modal analysis of the gearbox is carried out, and the analysis results are shown in the figure.
The results show that the first and second modes of the gearbox are 580 Hz and 635 Hz respectively, the first mode is axial bending of the gearbox, and the second mode is axial expansion deformation of both sides of the gearbox. It is known from the high-speed linear operation condition of the train that the vibration acceleration response of the axle box and the gear box has a higher energy point at the frequency of 576 Hz, and the transverse vibration energy is higher than the vertical vibration. The dynamic stress frequency response at the fixed code of the sensor outside the gear box has a highest energy point at the frequency of 576 Hz, which is basically consistent with the first-order natural frequency (580 Hz) of the gear box; When the train is running at a low speed and in a straight line, the vibration acceleration response of the axle box and the gear box appears a higher vibration energy point near the frequency of 365 Hz and 632 Hz, among which the vibration at 632 Hz is the most intense. The first-order dominant frequency of dynamic stress at the fixed code of the sensor outside the gear box is about 632 Hz, which is basically consistent with the second-order natural frequency (635 Hz) of the gear box, indicating that when the speed of high-speed train is 303km / h and 190km / h, the structure of the gear box has resonance phenomenon. A large number of examples show that resonance is an important reason for the failure of engineering structures, most of which are in the form of fatigue without obvious plastic deformation [14]. It can be seen from the driven stress amplitude that the dynamic stress amplitude generated during the high-speed straight-line driving is far greater than that during the low-speed straight-line driving, and the EMU is mainly in the high-speed straight-line driving state. Therefore, it can be concluded that the main cause of the fatigue cracking of the gear box is that the track excitation during the high-speed straight-line driving of the train causes resonance of the gear box structure, resulting in the local high stress amplitude.