During the operation of the machine, it is subjected to external load or self load. Some of these loads are inevitably applied to the helical gear, and then the force analysis of the helical gear shaft leads to bending and torsion.
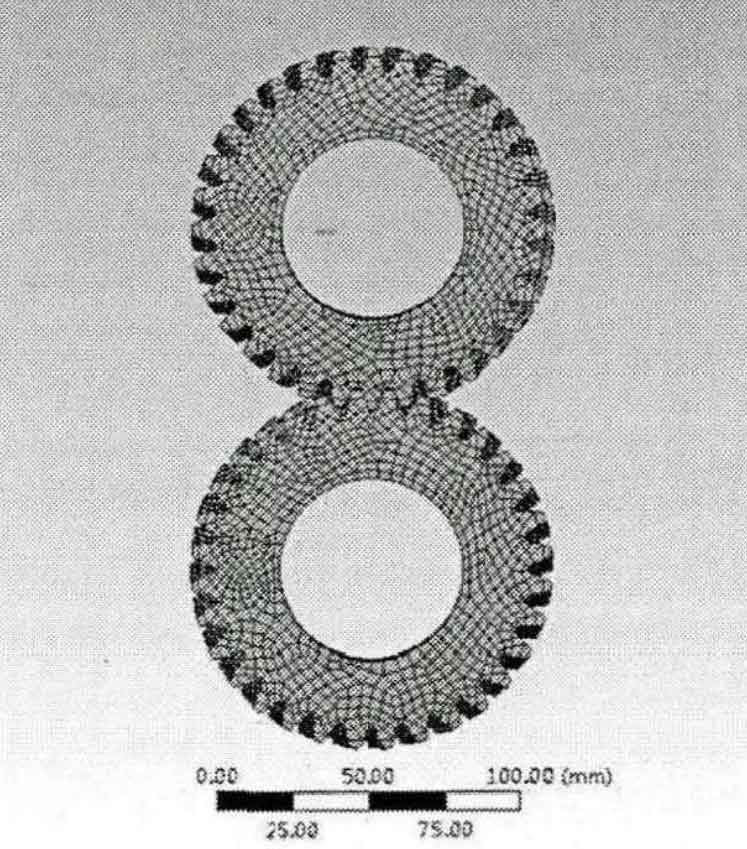
At the same time, there are processing errors in the helical gear itself, installation errors in the bearing installation, and self deformation. In combination with the above uncontrollable factors, when the helical gear is running, it may lead to unbalanced operation of the helical gear, resulting in offset, uneven stress and humidity of the helical gear, which will lead to premature damage of the helical gear.
In order to make the force on the helical gear more uniform, the following solutions are put forward: the optimal design of the helical gear or helical gear shaft, the adjustment of the relative spatial relationship between the helical gear and the bearing, the minimization of the installation error of the wheels and bearings, the improvement of the principle of the helical gear – tooth profile modification, etc. the tooth profile modification method is to cut the standard helical gear artificially, To make the stress distribution of the helical gear more uniform or reduce its maximum stress, or fine tune the helical angle of the helical gear to offset the tooth deformation of the helical gear and make the stress distribution on the meshing tooth surface uniform. The load on the contact line of helical gear teeth can be evenly distributed by tooth direction modification. The commonly used tooth profile modification methods include tooth end thinning, spiral angle trimming and drum trimming.