Circular arc tooth profile gear is widely used because of its unique multi-point meshing transmission and convex concave tooth surface contact form. Compared with involute tooth profile gear, circular arc tooth profile gear has the advantages of high bearing capacity and less wear on the tooth surface. Circular arc tooth line cylindrical gear is a kind of cylindrical gear with convex and concave curve teeth processed by milling cutter head. The tooth line of this gear is circular arc and has the characteristics of symmetrical section in the center of tooth width. The circular arc tooth line cylindrical gear has the characteristics of ordinary straight tooth cylindrical gear and the advantages of helical gear transmission. Compared with herringbone gear, it eliminates the axial force and does not need to leave the undercut. It has a compact structure and can be processed and formed at one time. More importantly, its tooth line curvature is not zero, which can produce arch effect and improve the stress state. It has outstanding advantages. Circular arc tooth profile circular arc tooth line cylindrical gear is a new gear that applies circular arc tooth profile to circular arc tooth line cylindrical gear. Theoretically, this gear will have the advantages of circular arc tooth profile gear and circular arc tooth line cylindrical gear transmission at the same time.
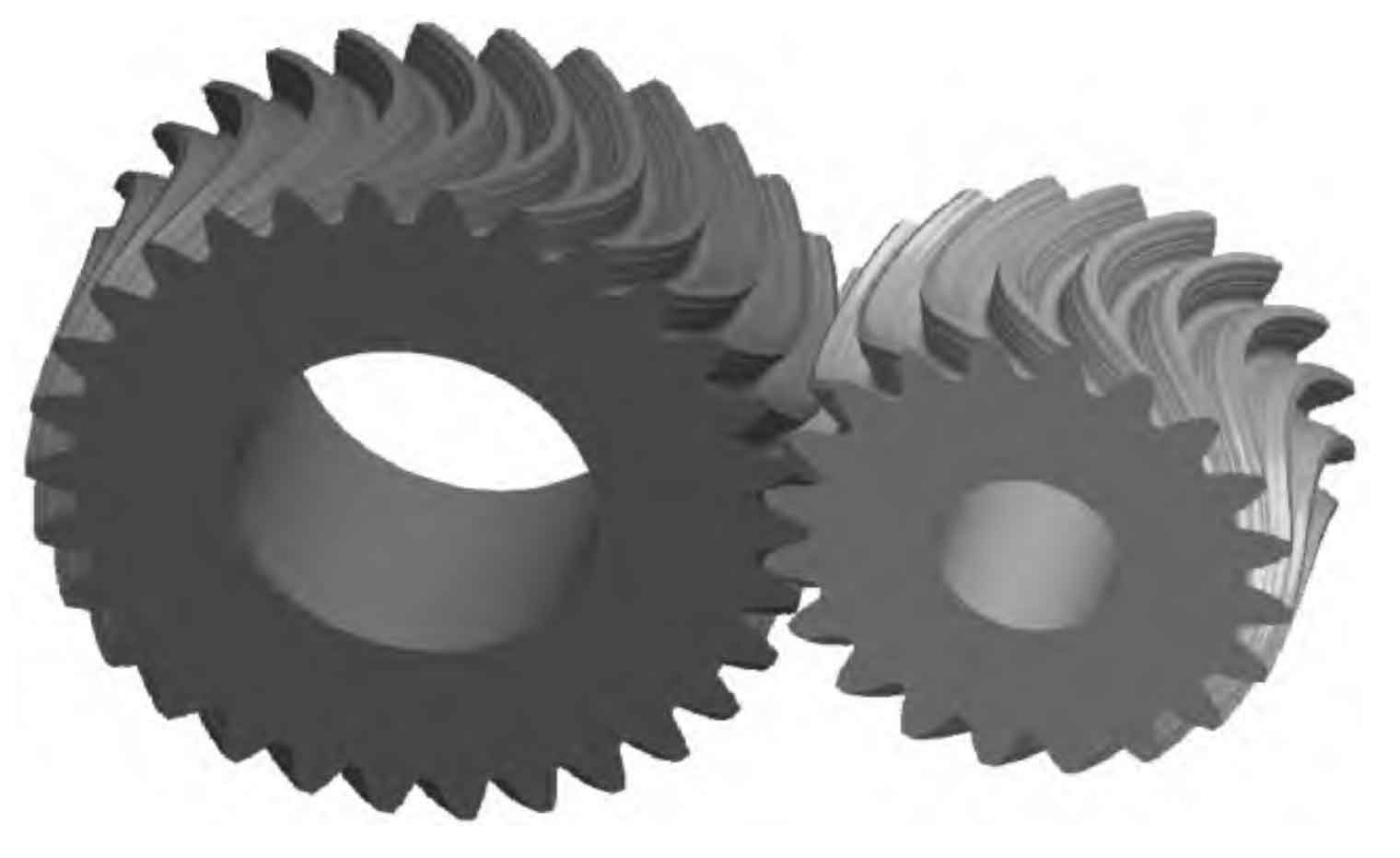
At present, scholars at home and abroad have done a lot of research on circular arc tooth profile gears and circular arc tooth line cylindrical gears. In the research of circular arc tooth profile gear: after single circular arc tooth profile and double circular arc tooth profile, four circular arc tooth profile and six circular arc tooth profile are proposed, and the meshing mechanism, bearing capacity and processing and manufacturing of four circular arc tooth profile and six circular arc tooth profile gears are deeply studied; In the research of circular arc cylindrical gear: sunzhijun et al. Analyzed the tooth surface contact stress of circular arc cylindrical gear, and the results confirmed that circular arc cylindrical gear has higher bearing capacity than involute spur gear and helical gear; Rui Tang et al. Gave the tooth surface equation of the circular arc tooth line cylindrical gear processed by the tooth strip cutter, established the three-dimensional solid model of the gear, and carried out the finite element contact stress analysis, and confirmed that the tooth arc radius had a great influence on the contact stress of the gear tooth surface; Mouru Qiang et al. Analyzed the influence of tooth profile error of circular arc tooth line cylindrical gear on transmission accuracy. Jia f et al. Established a three-dimensional solid model of circular arc tooth line cylindrical gear and analyzed its bending stress; Zhang Qi et al. Analyzed the tooth surface contact characteristics and machining methods of circular arc tooth line cylindrical gears; Fangyan Zheng et al. Proposed a new machining method of machining circular arc tooth line cylindrical gears by surface milling.
Wurongliang, a scholar from Taiyuan University of technology, discussed the basic meshing principle of circular arc gear, but there was no further research in the follow-up. Based on the gear meshing principle and differential geometry, the mathematical model of circular arc tooth profile circular arc tooth profile cylindrical gear tooth surface will be established according to the standard circular arc tooth profile, milling cutter head, circular arc bevel gear processing machine tool and the kinematic relationship between machine tool and workpiece. According to the mathematical model of tooth surface, the three-dimensional solid models of double circular arc tooth profile and four circular arc tooth profile circular arc tooth line cylindrical gears are established. Finally, the tooth surface contact analysis of the two gears is carried out by using the finite element method.
According to the milling principle of spiral bevel gear, the mathematical model of circular arc tooth profile circular arc tooth profile cylindrical gear tooth surface is established, and the discrete points of gear tooth surface are obtained according to the numerical method. On this basis, the three-dimensional solid model of gear is established by using three-dimensional design software.
Using finite element analysis software, the tooth surface contact analysis of double circular arc tooth profile and four circular arc tooth profile circular arc tooth line cylindrical gears is carried out, and the tooth surface contact stress nephogram is obtained. Through analysis, it is concluded that the tooth surface contact stress of four circular arc gear is about 80% of that of double circular arc gear. The research results can provide a theoretical basis for the design and application of circular arc tooth profile cylindrical gears.