Introduction
Hypoid gear is essential in automotive and industrial applications due to their efficiency in transferring power between non-intersecting shafts. The choice of material for hypoid gear significantly impacts their performance, durability, and overall lifespan. Traditionally, hypoid gear has been made from various steel alloys, but advances in materials science have introduced modern composites as potential alternatives. This article compares traditional alloys and modern composites used in hypoid gear manufacturing, focusing on their properties, advantages, and limitations.
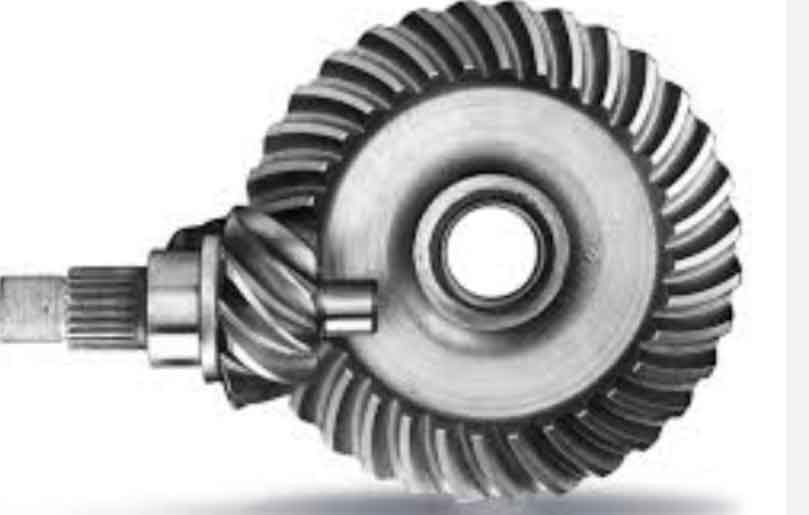
Traditional Alloys in Hypoid Gear
Traditional alloys, particularly various grades of steel, have been the go-to materials for hypoid gear. These alloys are chosen for their high strength, toughness, and wear resistance.
Common Traditional Alloys
- AISI 8620 Steel: A low-carbon alloy steel with excellent case hardening properties.
- AISI 9310 Steel: Known for its high hardenability and fatigue resistance.
- AISI 4140 Steel: A chromium-molybdenum alloy steel with good toughness and wear resistance.
Advantages of Traditional Alloys
- High Strength: Traditional steel alloys provide excellent tensile and yield strength, essential for withstanding high loads.
- Durability: These alloys are highly durable and resistant to wear and fatigue, making them suitable for demanding applications.
- Thermal Stability: Steel alloys maintain their properties under varying temperatures, which is critical for automotive applications.
Limitations of Traditional Alloys
- Weight: Steel alloys are relatively heavy, which can be a disadvantage in applications where weight reduction is critical.
- Corrosion: Despite being durable, steel alloys are susceptible to corrosion, requiring additional protective coatings or treatments.
- Cost: High-quality alloy steels can be expensive, impacting the overall cost of hypoid gear production.
Modern Composites in Hypoid Gear
Modern composites, such as carbon fiber-reinforced polymers (CFRP) and advanced ceramics, offer new possibilities for hypoid gear manufacturing. These materials are engineered to combine the best properties of their constituent materials, resulting in high-performance components.
Common Modern Composites
- Carbon Fiber-Reinforced Polymer (CFRP): Known for its high strength-to-weight ratio and excellent fatigue resistance.
- Glass Fiber-Reinforced Polymer (GFRP): Offers good mechanical properties and is more cost-effective than CFRP.
- Advanced Ceramics: Such as silicon nitride, these materials provide exceptional hardness and wear resistance.
Advantages of Modern Composites
- Lightweight: Composites like CFRP are significantly lighter than steel, contributing to weight reduction in automotive applications.
- High Strength-to-Weight Ratio: Composites can achieve similar or superior strength compared to traditional alloys while being much lighter.
- Corrosion Resistance: Many composites are inherently resistant to corrosion, reducing the need for additional protective measures.
- Design Flexibility: Composites can be tailored to specific applications, allowing for greater design flexibility and optimization.
Limitations of Modern Composites
- Cost: High-performance composites can be more expensive to produce and process than traditional alloys.
- Manufacturing Complexity: The fabrication of composite materials can be more complex and require specialized equipment and techniques.
- Thermal Sensitivity: Some composites may not perform as well as metals under extreme temperatures or may require additional thermal management.
Comparative Analysis
The choice between traditional alloys and modern composites for hypoid gear depends on various factors, including the specific application requirements, cost considerations, and performance goals. The table below summarizes the key differences between these materials.
Property | Traditional Alloys | Modern Composites |
---|---|---|
Strength | High | High to Very High |
Weight | Heavy | Lightweight |
Wear Resistance | Excellent | Good to Excellent |
Corrosion Resistance | Requires Coatings/Treatments | Inherently High |
Cost | Moderate to High | High |
Manufacturing Complexity | Relatively Simple | More Complex |
Thermal Stability | Excellent | Varies; Some require management |
Fatigue Resistance | High | High to Very High |
Conclusion
Both traditional alloys and modern composites offer distinct advantages and limitations for hypoid gear manufacturing. Traditional steel alloys provide high strength, durability, and thermal stability, making them reliable for demanding applications. However, modern composites present an opportunity for significant weight reduction, superior corrosion resistance, and high strength-to-weight ratios, though often at a higher cost and with more complex manufacturing requirements.
The choice between these materials should be guided by the specific performance requirements, environmental conditions, and cost constraints of the application. As materials science continues to advance, the potential for innovative composite materials to enhance hypoid gear performance and efficiency will only grow.