Spur gear is fundamental components in various mechanical systems, requiring precise manufacturing to ensure efficient and reliable performance. Over time, spur gear cutting techniques have evolved, improving accuracy, reducing production times, and enhancing spur gear performance. This study compares traditional spur gear cutting techniques, such as hobbing and shaping, with modern techniques, including CNC machining, laser cutting, and additive manufacturing.
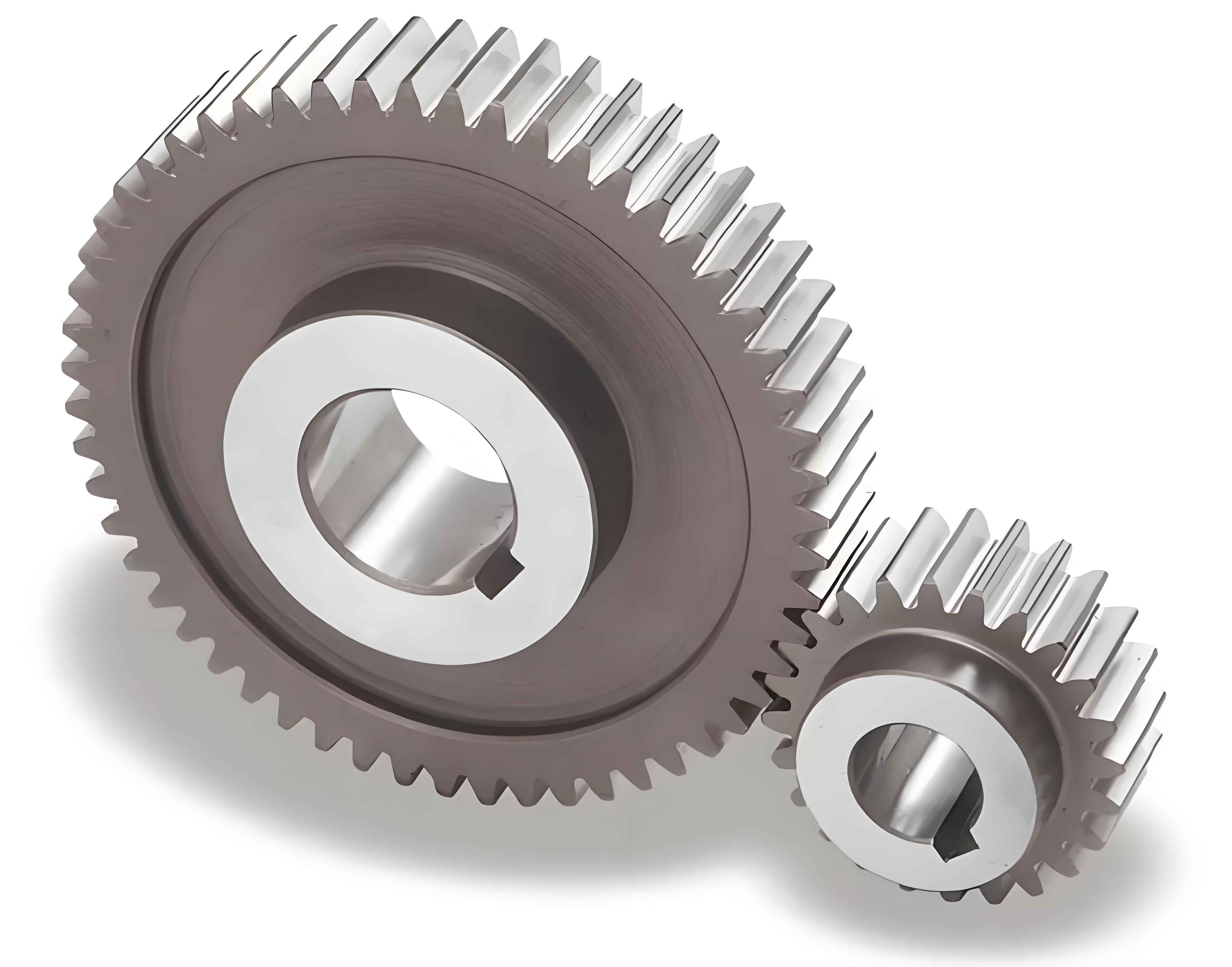
Traditional Spur Gear Cutting Techniques
- Hobbing
- Process: Hobbing uses a hob, a specialized cutting tool, to progressively cut teeth into the spur gear blank.
- Advantages: Efficient for mass production, good for various spur gear sizes, and provides high accuracy and surface finish.
- Disadvantages: Limited flexibility in spur gear design, setup time can be lengthy, and requires dedicated machinery.
- Shaping
- Process: Spur gear shaping uses a reciprocating cutter that moves up and down while the gear blank rotates.
- Advantages: Suitable for internal and external spur gear, capable of producing gears with complex profiles.
- Disadvantages: Slower than hobbing, less efficient for large-scale production, and limited to certain spur gear sizes.
Modern Spur Gear Cutting Techniques
- CNC Machining
- Process: Computer Numerical Control (CNC) machines use computerized control to precisely cut spur gear teeth.
- Advantages: High precision, flexibility in spur gear design, quick changeover between different gear types, and reduced manual labor.
- Disadvantages: Higher initial investment in machinery and software, requires skilled operators.
- Laser Cutting
- Process: Laser cutting uses a focused laser beam to melt and cut through the spur gear material.
- Advantages: Extremely precise cuts, suitable for thin materials, minimal tool wear, and fast production times.
- Disadvantages: Limited to certain materials, not suitable for very thick spur gear, and high energy consumption.
- Additive Manufacturing (3D Printing)
- Process: Additive manufacturing builds gears layer by layer using materials like metal powders or polymers.
- Advantages: Allows for complex and custom spur gear designs, minimal waste material, and reduced lead times for prototypes.
- Disadvantages: Currently limited by material properties for load-bearing applications, slower for large-scale production, and higher cost for certain materials.
Comparative Analysis
- Precision and Accuracy
- Traditional Techniques: Generally provide high precision, especially hobbing, but can be limited by the mechanical constraints of the machines.
- Modern Techniques: CNC machining and laser cutting offer superior precision and repeatability. Additive manufacturing provides good accuracy but is still evolving for high-load applications.
- Production Efficiency
- Traditional Techniques: Efficient for large-scale production but involve longer setup times and more manual adjustments.
- Modern Techniques: CNC machining and laser cutting significantly reduce setup times and increase production speed. Additive manufacturing is less efficient for mass production but excels in prototyping and custom spur gear production.
- Design Flexibility
- Traditional Techniques: Limited by the capabilities of the cutting tools and machines. Complex spur gear geometries are more challenging to produce.
- Modern Techniques: CNC machining and additive manufacturing offer high flexibility in spur gear design, allowing for more intricate and customized spur gear profiles.
- Cost Considerations
- Traditional Techniques: Generally lower initial equipment cost but higher operational costs due to longer setup times and more manual labor.
- Modern Techniques: Higher initial investment in advanced machinery and software but lower operational costs due to automation and faster production times.
Conclusion
Modern spur gear cutting techniques such as CNC machining, laser cutting, and additive manufacturing provide significant advantages in precision, efficiency, and design flexibility over traditional methods like hobbing and shaping. While traditional techniques remain relevant for certain applications, the advancements in modern manufacturing technologies are driving the industry towards more automated, flexible, and efficient production processes. Adopting these modern techniques can lead to improved spur gear quality, reduced production times, and cost savings in the long run.