Straight bevel gear is critical components in many mechanical systems, and their performance can be significantly enhanced by applying advanced surface coatings. This study compares various wear mechanisms in straight bevel gear and evaluates the effectiveness of different surface coatings in mitigating these wear mechanisms.
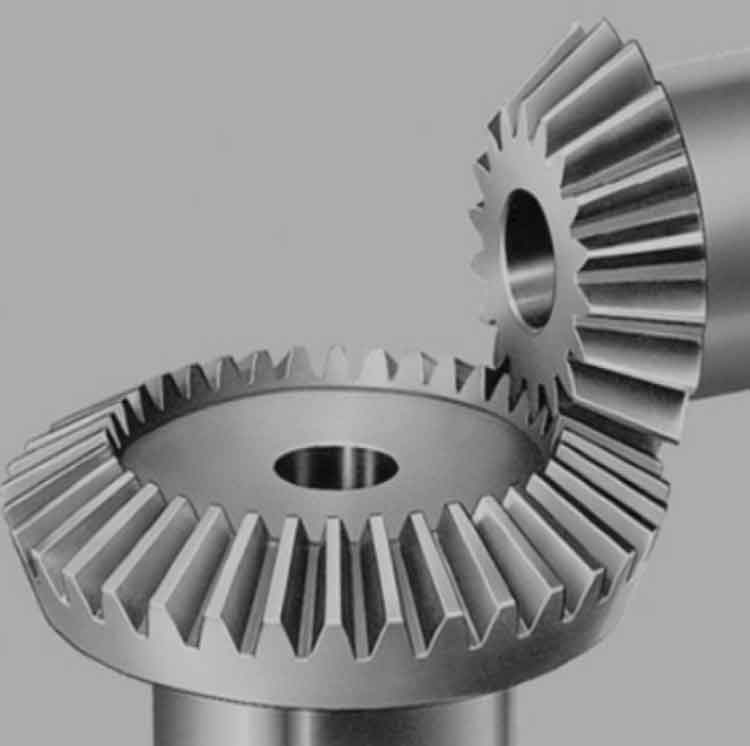
1. Introduction
Wear Mechanisms:
- Adhesive Wear: Occurs when two surfaces slide against each other, causing material transfer from one surface to another.
- Abrasive Wear: Happens when hard particles or asperities on one surface dig into the softer surface.
- Fatigue Wear: Results from repeated loading and unloading cycles, leading to surface cracks and material spalling.
- Corrosive Wear: Involves chemical or electrochemical reactions that degrade straight bevel gear material.
Advanced Surface Coatings:
- Physical Vapor Deposition (PVD): Creates thin, hard coatings with excellent adhesion and wear resistance.
- Chemical Vapor Deposition (CVD): Produces coatings with high hardness and thermal stability.
- Thermal Spray Coatings: Applies a wide range of materials, including metals, ceramics, and composites, to enhance wear resistance.
- Electroplating: Deposits metal layers, such as chromium or nickel, to improve surface hardness and corrosion resistance.
2. Methodology
Gear Samples:
- Straight bevel gear made from standard gear materials (e.g., alloy steel).
- Coated with various advanced surface treatments: PVD, CVD, thermal spray, and electroplating.
Testing Conditions:
- Simulate real-world operating conditions with controlled environments for temperature, load, and speed.
- Conduct tests for specific wear mechanisms: adhesive, abrasive, fatigue, and corrosive.
Wear Evaluation:
- Surface Analysis: Use scanning electron microscopy (SEM) and atomic force microscopy (AFM) to examine surface wear features.
- Weight Loss Measurement: Measure weight loss before and after testing to quantify material removal.
- Hardness Testing: Perform microhardness tests to assess the hardness of coatings.
- Fatigue Testing: Conduct cyclic loading tests to evaluate fatigue wear resistance.
3. Results and Discussion
Adhesive Wear:
- Uncoated Gears: Significant material transfer and surface roughening.
- PVD Coatings: Excellent reduction in adhesive wear due to high hardness and low friction coefficients.
- CVD Coatings: Similar performance to PVD with slightly better thermal stability.
- Thermal Spray Coatings: Moderate improvement in adhesive wear resistance.
- Electroplating: Effective in reducing wear but less durable than PVD and CVD.
Abrasive Wear:
- Uncoated Gears: Deep scratches and grooves from hard particles.
- PVD Coatings: High resistance to abrasive wear due to hard, smooth surface.
- CVD Coatings: Superior to PVD in environments with high temperatures and abrasive particles.
- Thermal Spray Coatings: Provides a tough barrier but can suffer from coating delamination.
- Electroplating: Good initial protection, but performance degrades with prolonged exposure to abrasives.
Fatigue Wear:
- Uncoated Gears: Rapid development of surface cracks and spalling.
- PVD Coatings: Significant improvement in fatigue life due to surface hardening and reduced crack initiation.
- CVD Coatings: Exceptional fatigue resistance with minimal surface damage over long cycles.
- Thermal Spray Coatings: Improved fatigue life, but performance can vary with coating thickness and uniformity.
- Electroplating: Enhanced fatigue resistance, particularly with thick, well-adhered coatings.
Corrosive Wear:
- Uncoated Gears: Severe surface degradation in corrosive environments.
- PVD Coatings: Good resistance to corrosion with proper coating selection.
- CVD Coatings: Excellent corrosion protection, especially in high-temperature applications.
- Thermal Spray Coatings: Effective against corrosion but requires careful material selection to avoid porosity.
- Electroplating: Provides strong corrosion resistance, particularly with nickel or chromium coatings.
4. Conclusion
Overall Performance:
- PVD and CVD Coatings: Offer the best overall protection against all types of wear mechanisms, with PVD being slightly more versatile and CVD excelling in high-temperature applications.
- Thermal Spray Coatings: Provide substantial improvements but can be prone to issues like delamination and porosity.
- Electroplating: Effective for both wear and corrosion resistance, but performance depends on coating thickness and adhesion quality.
Recommendations:
- For applications involving high loads and temperatures, CVD coatings are recommended due to their superior thermal stability and wear resistance.
- PVD coatings are suitable for applications requiring low friction and high hardness.
- Thermal spray coatings can be used where cost is a concern, and moderate improvement is acceptable.
- Electroplating is effective for corrosion-prone environments, provided the coatings are applied with high quality and precision.
By selecting appropriate surface coatings based on specific wear mechanisms and operational conditions, the service life of straight bevel gears
can be significantly extended, leading to improved performance and reduced maintenance costs.