Abstract
Spiral bevel gears are widely used in automotive, aerospace, and mining machinery due to their high load-bearing capacity, high transmission ratio, and efficiency. However, the manufacturing accuracy of these gears is directly related to the errors in the numerical control (NC) machine tools used for their production. This paper focuses on the sensitivity analysis of machine tool geometric errors that affect the tooth surface deviation of spiral bevel gears. By establishing a machining deviation model, both local sensitivity analysis and Sobol global sensitivity analysis are applied to study the influence of input parameter range changes on the output results. The key geometric errors affecting tooth surface deviation are identified, and guidelines for selecting the appropriate sensitivity analysis method are provided.
1. Introduction
Spiral bevel gears are characterized by their complexity in tooth surface geometry, making them challenging to manufacture with high precision. The accuracy of the manufactured gears is heavily influenced by the geometric errors of the NC machine tools used for cutting. Geometric errors, including linear and angular deviations, can lead to deviations in the tooth surface, affecting the performance and lifespan of the gear system.
1.1 Importance of Sensitivity Analysis
Sensitivity analysis is a powerful tool to study the impact of input parameter variations on output results. It helps identify the most influential input factors, allowing for targeted improvements in manufacturing processes. For spiral bevel gears, understanding the sensitivity of tooth surface deviation to machine tool errors is crucial for enhancing manufacturing accuracy and reducing post-processing compensation efforts.
1.2 Objective of the Study
The objective of this study is to analyze the sensitivity of spiral bevel gear tooth surface deviation to geometric errors in NC machine tools. This is achieved by:
- Establishing a mathematical model for machining deviation.
- Applying both local and global sensitivity analysis methods.
- Identifying the key geometric errors that significantly affect tooth surface deviation.
- Providing guidelines for selecting the appropriate sensitivity analysis method based on the characteristics of the model and input parameters.
2. Machine Tool Geometric Errors
The accuracy of NC machine tools is influenced by various geometric errors, including linear and angular deviations in the movement axes. These errors can be categorized into 30 different types for a typical five-axis machine tool used for spiral bevel gear production.
able 1 summarizes the 30 geometric errors considered in this study, with ε representing angular errors and δ representing linear errors.
Axis | Geometric Errors | Numbering |
---|---|---|
X | δxX, δyX, δzX, εαX, εβX, εγX | 1-6 |
Y | δxX, δyY, δzY, εαY, εβY, εγY | 7-12 |
Z | δxX, δyZ, δzZ, εαZ, εβZ, εγZ | 13-18 |
A | δxA, δyA, δzA, εαA, εβA, εγA | 19-24 |
B | δxB, δyB, δzB, εαB, εβB, εγB | 25-30 |
To analyze the sensitivity of tooth surface deviation to machine tool errors, a mathematical model must be established. This model relates the geometric errors to the deviations in the machined tooth surface.
3.1 Ideal Tooth Surface Equation
Under ideal conditions, the tooth surface of a spiral bevel gear can be described by a mathematical equation derived from the kinematic relationships between the various axes of the NC machine tool. The ideal tooth surface equation rg can be expressed as:
rg=MA⋅MB⋅MZ⋅MX⋅MY⋅rt(u,θ)
where Mq (with q = A, B, Z, X, Y\)) are the transformation matrices corresponding to each axis, and \(r_t(u, \theta) is the tool equation with u and θ as parameters.
3.2 Actual Tooth Surface Equation
In reality, the machined tooth surface deviates from the ideal due to geometric errors in the machine tool. The actual tooth surface equation reg can be expressed as:
reg=MA⋅MeA⋅MB⋅MeB⋅MZ⋅MeZ⋅MX⋅MeX⋅MY⋅MeY⋅rt(u,θ)
where Meq (with (q = A, B, Z, X, Y)) are the error matrices corresponding to each axis.
4. Sensitivity Analysis Methods
Sensitivity analysis can be broadly classified into local and global methods. Each method has its advantages and limitations, making it essential to choose the appropriate method based on the characteristics of the model and input parameters.
4.1 Local Sensitivity Analysis
Local sensitivity analysis involves varying a single input parameter while keeping others constant. The sensitivity coefficient is calculated based on the change in the output result due to the input variation. This method is straightforward and computationally efficient but may not capture interactions between input parameters.
4.2 Sobol Global Sensitivity Analysis
Sobol global sensitivity analysis considers the entire range and distribution of input parameters and their interactions. It decomposes the output variance into contributions from individual parameters and their interactions, allowing for a more comprehensive understanding of the sensitivity. However, this method requires significant computational resources, especially for models with many input parameters.
5. Case Study
To demonstrate the application of sensitivity analysis, a case study is conducted using the established tooth surface deviation model. The geometric parameters and processing conditions of the spiral bevel gear are shown in Table 2.
Parameter | Value |
---|---|
Number of teeth (Z1) | 18 |
Module at large end (mt) | 4.29 mm |
Face width (wb) | 45 mm |
Hand of spiral (left) | – |
Midpoint helix angle (β) | 35° |
Addendum height (ha) | 8.78 mm |
Dedendum height (hf) | 5.03 mm |
Pitch cone angle (γ1) | 27.21° |
Face cone angle (γp) | 31.65° |
Root cone angle (γf) | 25.36° |
Outside cone distance (Lo) | 140.9 mm |
Using the local sensitivity analysis method, the sensitivity coefficients of each geometric error are calculated. Figure 4 shows the results, indicating that certain errors have a higher impact on tooth surface deviation than others.
5.2 Sobol Global Sensitivity Analysis Results
The Sobol global sensitivity analysis considers the entire range and distribution of geometric errors. Figure 5 shows the global sensitivity coefficients in descending order, highlighting the most significant errors.
6. Comparison and Discussion
6.1 Comparison of Methods
Under ideal conditions with identical input parameter ranges and distributions, both local and global sensitivity analysis methods yield similar trends in sensitivity coefficients, as shown in Section 5. However, when the input parameter ranges vary, the Sobol method provides a more comprehensive understanding of the sensitivity, capturing interactions and non-linear effects.
6.2 Selection of Sensitivity Analysis Method
The choice of sensitivity analysis method depends on the characteristics of the model and input parameters:
- Local Sensitivity Analysis is suitable for models with linear or weakly nonlinear relationships, where input parameter ranges and distributions are not well-defined or similar.
- Sobol Global Sensitivity Analysis is preferred for complex, nonlinear models with well-defined input parameter ranges and high accuracy requirements.
7. Conclusion
This paper presents a comprehensive sensitivity analysis of the impact of machine tool geometric errors on spiral bevel gear tooth surface deviation. By applying both local and Sobol global sensitivity analysis methods, key geometric errors that significantly affect tooth surface deviation are identified. Guidelines for selecting the appropriate sensitivity analysis method based on model and input parameter characteristics are provided. The findings contribute to enhancing the manufacturing accuracy of spiral bevel gears and reducing post-processing compensation efforts.
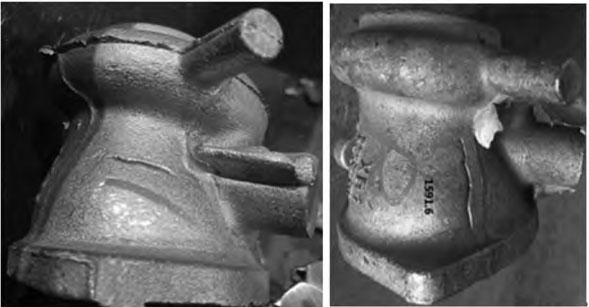