Hypoid gears and spiral bevel gears are both types of bevel gears with specific design characteristics that make them suitable for various applications. While they share some similarities, they also have distinct strengths that set them apart. Let’s compare hypoid gears to spiral bevel gears in terms of their strengths and applications:
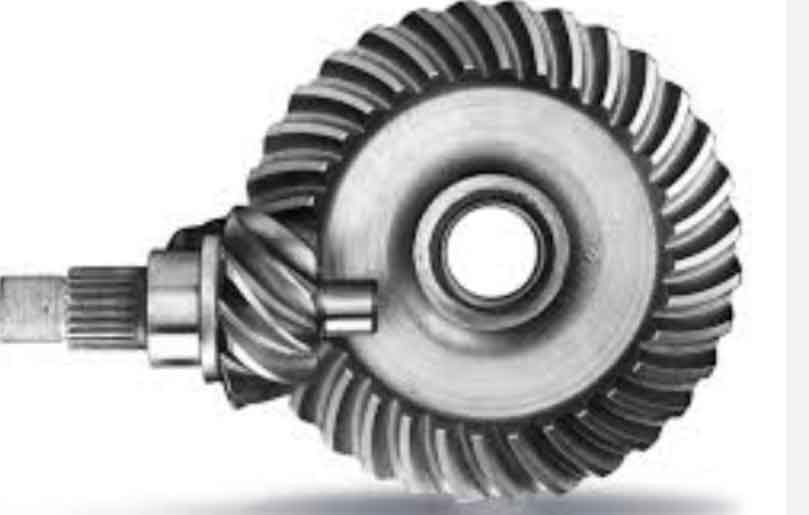
Hypoid Gears:
Strengths:
- Offset Axis: Hypoid gears have an offset axis, which allows them to transmit power between non-intersecting and non-parallel shafts. This feature provides design flexibility and adaptability to various drivetrain configurations.
- High Torque Capacity: Hypoid gears can handle high torque levels, making them ideal for applications that require heavy-duty power transmission.
- Compact Design: Hypoid gears allow for higher gear ratios within a more compact form, making them suitable for applications with limited space constraints.
- Smooth Operation: The helical design of hypoid gears enables smooth gear meshing, resulting in quieter operation compared to straight-cut bevel gears.
- Efficiency: Hypoid gears offer efficient power transmission, leading to lower power losses and improved energy efficiency.
Applications:
- Automotive Rear Differentials: Hypoid gears are commonly used in rear differentials of rear-wheel-drive and all-wheel-drive vehicles for efficient torque distribution to the rear wheels.
- Industrial Gearboxes: Hypoid gears find applications in various industrial gearboxes that require high torque capacity and compact designs.
- Power Tools: Hypoid gears are used in power tools, such as circular saws, where high torque transmission is essential.
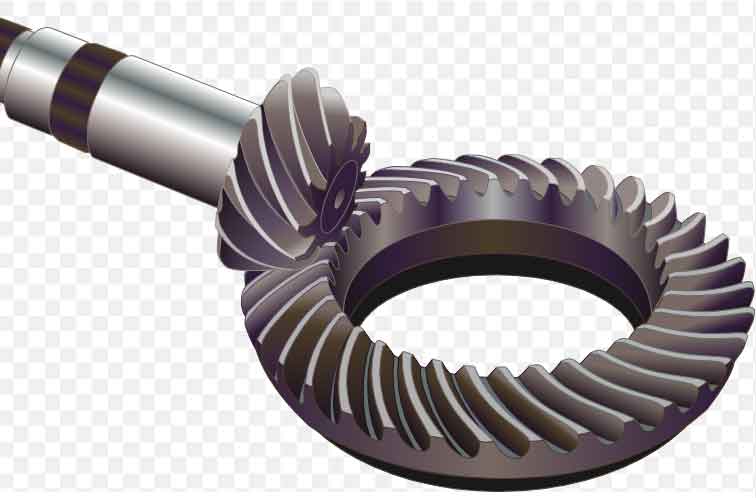
Spiral Bevel Gears:
Strengths:
- Intersecting Shafts: Spiral bevel gears have intersecting shafts at a specific angle, making them suitable for applications where the shafts need to be at a right angle to each other.
- High Precision: Spiral bevel gears provide high precision and accuracy due to their involute tooth profile, making them ideal for applications requiring smooth and reliable gear meshing.
- Load Distribution: The tooth contact pattern of spiral bevel gears allows for even load distribution, leading to improved gear life and reduced wear.
- Strength and Durability: Spiral bevel gears are known for their strength and durability, making them suitable for heavy-duty applications.
Applications:
- Machine Tools: Spiral bevel gears are used in machine tools, such as milling machines and lathes, due to their precision and load-carrying capacity.
- Aircraft Propellers: Spiral bevel gears are employed in aircraft propellers to efficiently transmit power from the engine to the propeller shaft.
- Marine Applications: Spiral bevel gears find use in marine propulsion systems, providing reliable torque transmission from the engine to the propeller.
In summary, both hypoid gears and spiral bevel gears have specific strengths and applications. Hypoid gears are well-suited for applications requiring offset shafts, high torque capacity, and compact design. On the other hand, spiral bevel gears excel in applications requiring high precision, load distribution, and strength. The choice between these gear types depends on the specific requirements of the application and the desired performance characteristics.