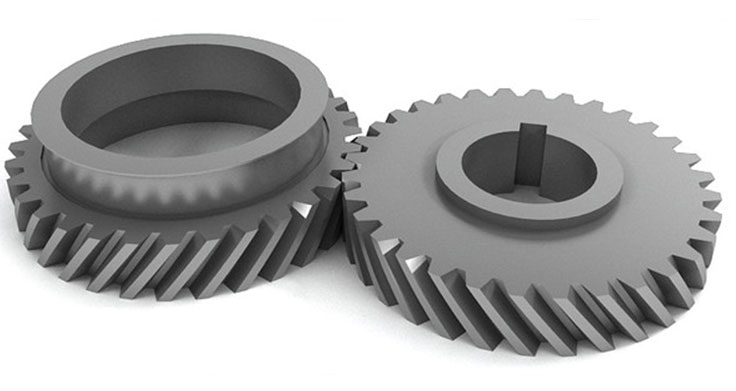
The strength of helical gears lies in their unique design and helical tooth profile, which enables them to handle higher loads and transmit substantial torque compared to other gear types. Let’s delve into the key factors that contribute to the load-bearing capacity of helical gears:
1. Helical Tooth Profile:
Helical gears have teeth with a helix angle, which is an angle formed by the teeth’s inclination with respect to the gear axis. The helix angle allows for gradual and continuous engagement of the teeth during meshing. This gradual engagement results in a smoother transfer of forces, reducing impact and stress concentration on individual teeth.
2. Load Distribution:
The helical tooth profile spreads the load across multiple teeth along the contact line. This load distribution characteristic ensures that the forces acting on the gears are distributed over a larger surface area, reducing the pressure on individual teeth and enhancing the gear’s load-carrying capacity.
3. Axial Thrust Absorption:
Helical gears produce an axial thrust force along the gear axis due to the helix angle. In double helical gears (herringbone gears), the helix angle is reversed on one side of the gear, canceling out the axial thrust forces. This design feature allows for better load balancing and minimizes the need for additional thrust bearings.
4. Larger Contact Area:
The helical tooth profile creates a larger contact area between meshing gears compared to spur gears. This larger contact area distributes the load more effectively and increases the gear’s capacity to carry higher loads and transmit greater torque.
5. Material Selection and Heat Treatment:
The choice of high-quality materials and appropriate heat treatment processes significantly impact the load-bearing capacity of helical gears. High-strength materials and proper heat treatment improve the gears’ hardness and durability, making them capable of withstanding higher loads without failure.
6. Gear Design Optimization:
Engineers can optimize the gear design based on specific application requirements to improve load-carrying capacity. Factors such as the helix angle, gear module or diametral pitch, tooth width, and material selection are considered during the design process to ensure the gears can handle the intended loads and torque.
7. Lubrication and Surface Finish:
Proper lubrication is critical for reducing friction and wear in helical gears during operation. Adequate lubrication ensures smoother gear engagement and contributes to the gear’s load-carrying capacity. Additionally, surface finishing processes like grinding or honing can improve the gear’s strength and wear resistance.
8. Quality Manufacturing:
Precise manufacturing processes, including gear cutting and finishing, are essential for achieving accurate gear tooth profiles and ensuring consistent quality. High-quality manufacturing contributes to the gears’ load-bearing capacity and overall performance.
Helical gears are widely used in heavy machinery, automotive transmissions, and other industrial applications that demand robust power transmission. Their load-bearing capacity, smooth operation, and efficiency make them an integral part of modern mechanical systems, allowing them to handle demanding loads and transmit power effectively across various industries.