Straight bevel gears and spiral bevel gears are both types of bevel gears used for power transmission between intersecting shafts at a right angle. While they serve similar functions, they have distinct design characteristics and performance attributes that make them suitable for different use cases. Here’s a comparison of straight bevel gears and spiral bevel gears in terms of their performance and typical applications:
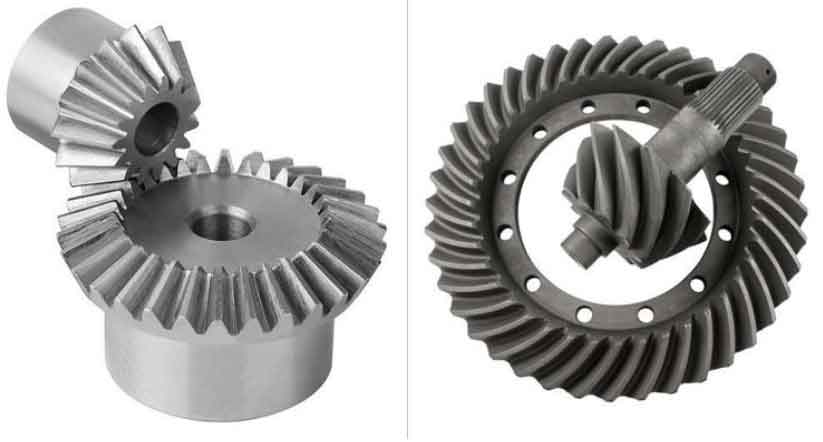
1. Tooth Profile:
- Straight Bevel Gears: Straight bevel gears have straight teeth that are cut directly across the gear face, forming a straight line.
- Spiral Bevel Gears: Spiral bevel gears have curved teeth that form a helix around the gear face, creating a smoother and more gradual meshing action.
2. Noise and Vibration:
- Straight Bevel Gears: Straight bevel gears can produce more noise and vibration during operation due to the abrupt meshing action of their straight teeth.
- Spiral Bevel Gears: Spiral bevel gears have a more gradual and continuous tooth engagement, resulting in reduced noise and vibration levels.
3. Load Capacity:
- Straight Bevel Gears: Straight bevel gears can handle high loads and transmit significant torque efficiently, making them suitable for heavy-duty applications.
- Spiral Bevel Gears: Spiral bevel gears also have a high load capacity and can transmit heavy loads effectively.
4. Efficiency:
- Straight Bevel Gears: Straight bevel gears have less sliding action during meshing, resulting in higher efficiency and reduced heat generation.
- Spiral Bevel Gears: Spiral bevel gears offer smoother meshing, which can lead to slightly higher efficiency compared to straight bevel gears.
5. Axial Thrust:
- Straight Bevel Gears: Straight bevel gears generate axial thrust forces along the gear shafts due to the contact between the mating gears. This axial thrust must be properly accommodated to prevent excessive axial loads on bearings.
- Spiral Bevel Gears: Spiral bevel gears are designed to minimize axial thrust, making them ideal for applications where axial loads need to be controlled.
6. Applications:
- Straight Bevel Gears: Straight bevel gears are commonly used in automotive differentials, industrial machinery, hand tools, marine propulsion systems, and farm equipment.
- Spiral Bevel Gears: Spiral bevel gears are preferred in precision applications such as aerospace, defense, robotics, and high-performance automotive systems, where smooth operation, reduced noise, and precision are critical.
7. Cost:
- Straight Bevel Gears: Due to their simpler design and manufacturing process, straight bevel gears are often more cost-effective to produce than spiral bevel gears.
- Spiral Bevel Gears: Spiral bevel gears require more complex machining and may be slightly more expensive to manufacture.
Both straight bevel gears and spiral bevel gears have their strengths and applications. Straight bevel gears are suitable for heavy-duty applications where high load capacity and efficiency are essential. On the other hand, spiral bevel gears excel in precision applications where smooth operation, reduced noise, and controlled axial thrust are critical. Selecting the appropriate gear type depends on the specific requirements of the application, including load capacity, efficiency, noise, vibration, and cost considerations.