Material selection is a critical aspect of gear manufacturing, and it significantly impacts the performance, durability, and reliability of gears. Gear forging, in particular, allows for a wide range of materials to be used, each with its own unique properties and advantages. Here’s why material selection is essential in gear manufacturing:
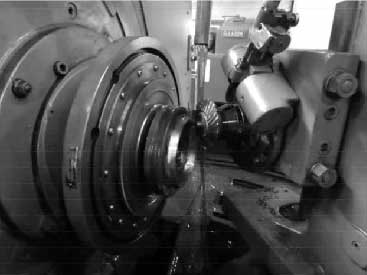
- Strength and Durability: Gears are subjected to high loads, forces, and repetitive stresses during operation. The selected material must possess adequate strength and durability to withstand these conditions without failure. Materials with high tensile and yield strength, as well as good fatigue resistance, are typically preferred for gear manufacturing. Gear forging allows for the use of materials like alloy steels, carbon steels, and specialty steels that provide the necessary strength and durability.
- Wear Resistance: Gears experience sliding and rolling contact, which can lead to wear and surface damage over time. The material used should have good wear resistance to ensure the gears maintain their dimensional accuracy and performance throughout their service life. Materials such as case-hardened steels, alloy steels with specific hardening treatments, and specialty alloys like tool steels or powder metallurgy steels are commonly chosen for their wear-resistant properties.
- Toughness and Impact Resistance: Gears may be exposed to sudden shocks, impacts, or overloads during operation. The selected material should exhibit high toughness and impact resistance to prevent catastrophic failures and to withstand unexpected loads. Tough materials, such as alloy steels with appropriate heat treatment, are preferred to ensure the gears can absorb energy and resist fracture under impact conditions.
- Fatigue Resistance: Gears undergo cyclic loading, which can lead to fatigue failure if the material is not properly selected. Fatigue resistance is a crucial consideration, especially in high-cycle applications. Materials with good fatigue resistance, such as through-hardened steels or specialty alloys, are selected to ensure the gears can withstand the repetitive loading and provide long service life without failure.
- Corrosion Resistance: Gears used in environments where corrosion or exposure to aggressive substances is a concern require materials with good corrosion resistance. For example, gears used in marine or offshore applications may need to withstand saltwater or acidic conditions. Stainless steels, corrosion-resistant alloys, or surface coatings can be utilized to enhance the corrosion resistance of the gears and ensure their long-term performance.
- Temperature and Heat Resistance: Gears employed in high-temperature environments, such as those found in aerospace, automotive racing, or industrial applications, need materials that can withstand elevated temperatures without significant loss of mechanical properties. Heat-resistant alloys, tool steels, or specialty materials with high-temperature capabilities are chosen to maintain gear performance and dimensional stability under such conditions.
- Machinability and Processability: Material selection also considers the ease of machining and processability. Gears often require secondary operations such as machining, grinding, or heat treatment. Materials that are easily machinable and exhibit good processability, while still meeting the necessary mechanical and performance requirements, are preferred to ensure efficient manufacturing processes and cost-effective production.
By carefully selecting the appropriate material for gear manufacturing, taking into account factors such as strength, durability, wear resistance, toughness, fatigue resistance, corrosion resistance, temperature resistance, and processability, gear manufacturers can ensure that the gears meet the specific application requirements and deliver optimal performance and reliability. Gear forging provides the flexibility to choose from a wide range of materials, allowing for the selection of materials that best suit the intended use and operating conditions, resulting in gears with a strong foundation and long service life.