The static and dynamic finite element simulations of the same helical gear pair are carried out respectively. From the stress nephogram of both, whether static or dynamic simulation, the contact line is an inclined line with a certain angle with the edge of the tooth. At the same time, the position of the maximum stress is the position of the sharp angle of the helical gear tooth that is easy to cause stress concentration, which is consistent with the actual working condition. The stress obtained from the dynamic contact calculation of the helical gear is greater than that obtained from the static contact calculation of the helical gear. This is because the load deformation of the helical gear pair will produce a relatively large meshing impact in the meshing process, resulting in a certain offset of the meshing line and a certain change in the speed of the driven wheel, resulting in strong vibration and impact.
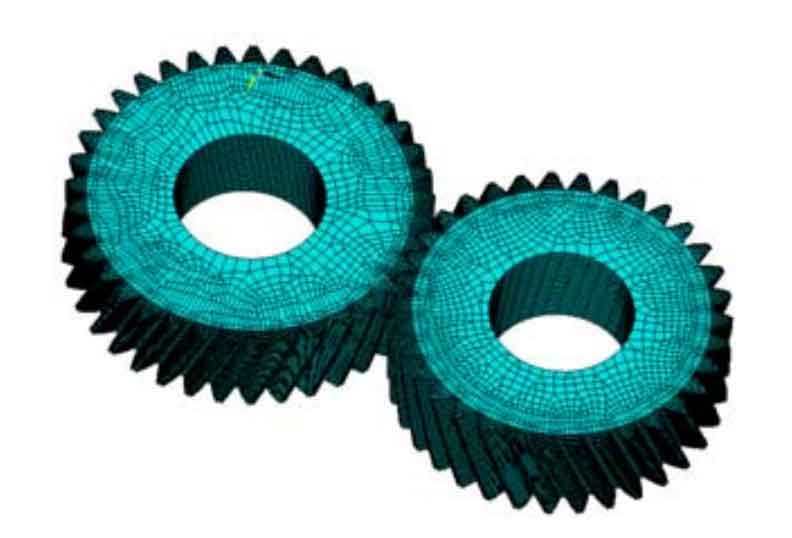
In the whole meshing process of helical gear, the contact of tooth surface is very complex, and the static contact analysis only considers the meshing of tooth surface in a transient state, which can not fully reflect the dynamic characteristics of helical gear in the transmission process. Therefore, the static contact analysis method of helical gear is not perfect, while the dynamic analysis can calculate the contact stress and change trend of different meshing positions in the process of one-time solution.