In a pair of assembled helical gear pairs, backlash J refers to the clearance between the tooth surfaces of meshing helical gears. The side clearance can be measured on the normal plane or along the meshing line, as shown in the figure, but it should be noted that it is calculated and specified on the end plane or meshing plane, i.e. the tangent plane of the base circle. A single helical gear has no backlash. It has only tooth thickness. The backlash of meshing helical gears is controlled by the center distance of a pair of helical gears and the actual tooth thickness of each helical gear.
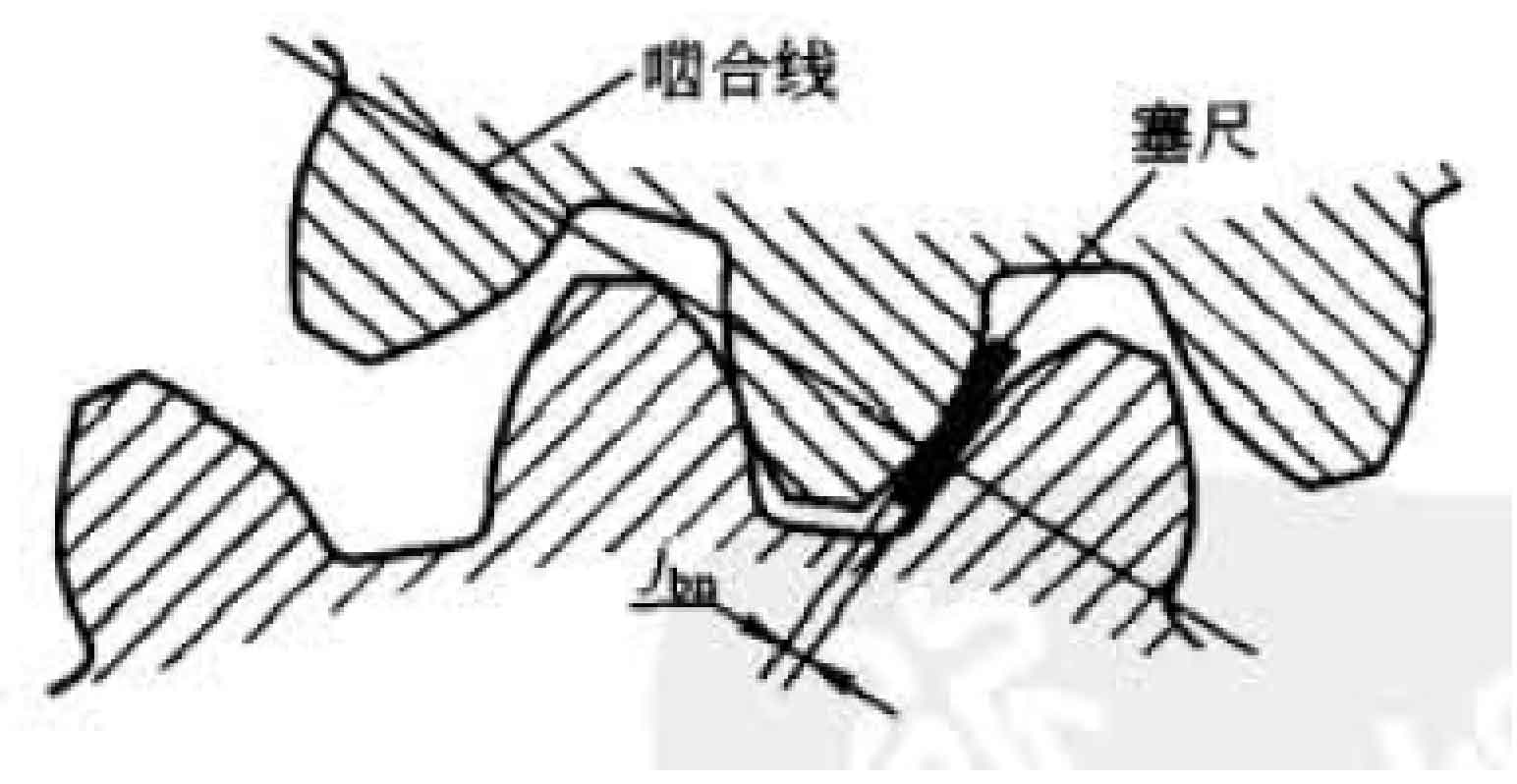
The meshing helical gear pair must have a certain backlash and ensure that the non working tooth surfaces will not contact each other. In a fixed meshing, the backlash is changed by the changes of speed, temperature, load and many other factors during operation. Under the condition that the static state can be measured, it is necessary to ensure that there is enough backlash so that the helical gear still has enough backlash under the most unfavorable working environment of loaded operation. The amount of backlash required is related to the size, accuracy, application and installation of helical gears.
Tooth backlash in helical gears, as with any gear type, refers to the intentional gap left between the mating teeth of two gears in mesh. This gap or play is essential for the proper operation of gear sets, allowing for thermal expansion, lubrication, and preventing tooth interference and damage under load. In helical gears, which feature teeth that are angled relative to the gear’s axis, backlash is still a critical parameter, but its measurement and implications can be slightly different due to the helical design.
Definition and Purpose
Backlash is defined as the amount of space between the backside of a tooth on one gear and the front side of the corresponding tooth on the meshing gear. For helical gears, this is typically measured along the normal plane — the plane perpendicular to the tooth’s helix angle — rather than directly along the path of the tooth face. This is because the helix angle of the teeth means that they engage more gradually, which affects how the backlash is distributed across the contact length of the teeth.
The main purposes of backlash in helical gears include:
- Accommodating Thermal Expansion: As gears operate, they can heat up, causing the metal to expand. Backlash provides the necessary space for this expansion, preventing the gears from binding or jamming.
- Allowing for Lubrication: The space created by backlash allows for adequate lubrication between the teeth, reducing wear and extending the life of the gear.
- Compensating for Manufacturing Imperfections: It’s nearly impossible to manufacture gears with perfectly matching tooth profiles. Backlash ensures that these minor imperfections do not lead to interference between the teeth during operation.
- Absorbing Shock Loads: In applications where gears may experience sudden or variable loads, backlash provides a small margin that can help absorb and distribute these forces, reducing the risk of damage.
Measurement and Specification
Backlash in helical gears is usually specified and measured in the normal plane to account for the helix angle. This means the actual physical gap you might see if looking at the gears from the side (the axial plane) is not the direct measure of backlash. The effective backlash considered for the gear’s operation is the component of this gap in the direction normal to the tooth face, which is a function of both the gap and the helix angle.
The amount of backlash required can vary based on the application, with tighter tolerances for precision machinery where exact positioning is critical, and more generous allowances for heavy machinery where temperature variation and shock loads might be more significant.
Tooth backlash in helical gears is a crucial design consideration that affects the gear’s performance, lifetime, and efficiency. Proper management and specification of backlash are essential for ensuring the reliable operation of gear systems, particularly in applications involving high speeds, varying loads, or significant temperature changes.