Gear force analysis can be concluded that the radius of curvature of the tooth root fillet is the main factor affecting the bending stress of the tooth root under the condition that the other parameters of the gear are unchanged, that is, the bending fatigue strength of the tooth mainly depends on the radius of curvature of the tooth root fillet . From the results of physical and chemical tests, it can be seen that the hardness of the gear core is low, and the low hardness of the core will reduce the fatigue bending strength of the gear teeth. The study found that during gear operation, if the meshing spots are small, it will cause eccentric load, which will also reduce the bending fatigue strength of the gear teeth.
The radius of the root of the gear is enlarged by using a projector, and the radius of curvature of the root of the large helical gear is measured to be about 2.2mm at both the large and small ends. The study believes that if the radius of curvature of the tooth root fillet is too small, stress concentration will occur at the tooth root when the gear is stressed, which will lead to the initiation of fatigue cracks. The study found that when the radius of curvature of the tooth root fillet increases from 0.75mm to 1.5mm, the bending fatigue life of the gear is about 3 times the original. According to the starting position of the crack, it can be judged that the main reason for the low fatigue life of the tooth of the large helical gear is that the radius of curvature of the tooth root corner is too small. Too small radius of curvature of the tooth root fillet increases the stress concentration at the tooth root of the large helical gear during operation, resulting in a significant reduction in bending fatigue life.
The microstructure and hardness of the gear core will also significantly affect the fatigue performance of the gear. As the hardness of the core increases, its support for the hardened layer of the gear will also increase, thereby increasing the fatigue strength of the gear. That is to say, within the range required by the technical standards, the increase in the hardness of the core will increase the fatigue life of the gear. The lower hardness of the core will weaken its supporting effect on the hardened layer of the gear surface and reduce the fatigue life of the gear. The hardness test results show that the hardness of the gear core is low, so it is necessary to use materials that control hardenability or change the heat treatment process to increase the hardness of the gear core.
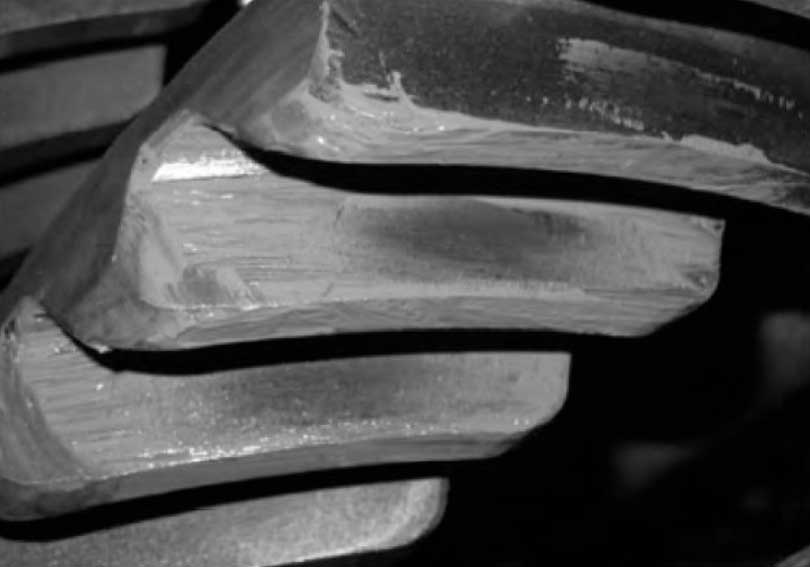
The size of the meshing spot during the operation of the large helical gear is measured, and the results are shown in the figure. According to the provisions of GB / T 13924-2008 “Involute Cylindrical Gear Precision Inspection Rules” and GB / Z18620.4-2008 “Cylinder Gear Inspection Code of Practice Part 4: Inspection of Surface Structure and Contact Contact Spots” The gear spots required for different grades of gears are different. The accuracy grade of the failed large helical gear is 7 ~ 8. According to the requirements of the above national standard, the meshing spot should be in the middle of the tooth surface, the length should not be less than 70% of the full tooth width, and the height should not be less than 60% of the full tooth height. The actual meshing spot size of the large helical gear in the figure is significantly smaller than the standard technical requirements in the direction of tooth width.
From the above analysis, it can be concluded that the fracture process of the large helical gear is as follows: under the bending stress of the large helical gear during working, the radius of curvature of the tooth root of the gear and the size of the meshing spot are small, resulting in stress at the tooth root Concentration, and because the hardness of the gear tooth core is low, the support for the surface hardening layer is weak, and eventually cracks initiate near the root of the small end of the middle of the convex surface of the gear tooth. With the continuous action of bending stress, the initiating crack spreads toward both ends of the gear tooth and the gear tooth center around the crack source. When the crack propagates towards the small end, it will buckle up towards the tooth tip, causing the resistance of its propagation process to gradually decrease, causing the crack to quickly expand to the small end. When the crack propagates toward the big end, the resistance to expansion is relatively large, and the speed of expansion is less than that of the small end. This also leaves a section of the big-end transient break zone that is too late to expand when the gear breaks.