We discuss the dynamic characteristics of the dynamic response of gears in time domain and frequency domain in three different cases (only considering stiffness excitation, only considering friction excitation, and considering stiffness excitation and friction excitation at the same time). In order to further explore the influence of stiffness excitation and friction excitation on gear dynamic response, the following analysis is carried out. Taking pitting-3 as an example, the dynamic responses of case I, case II and case III are compared to study the dynamic response of gears under three conditions: only considering stiffness excitation, only considering friction excitation, and considering stiffness excitation and friction excitation at the same time.
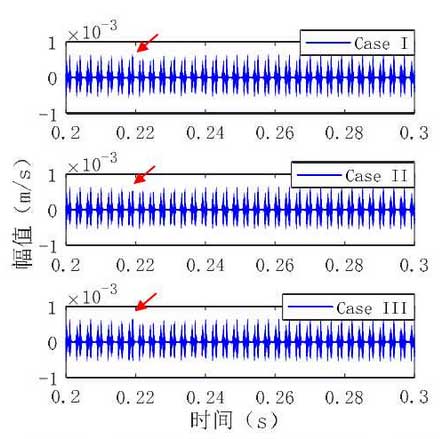
The speed signals of pitting-3 in case I, case II and case III are shown in Fig. 1. The dynamic response amplitudes of pitting-3 gears in case I, case II and case III are 0.00058 /, 0.00052 / and 0.00063 / respectively. It can be seen from Fig. 1 that the reduction of meshing stiffness and the sliding friction coefficient have obvious effects on the dynamic response of the gear system. From the amplitude of vibration response signal, when considering these two factors, the characteristics of pitting corrosion fault are more obvious than considering one factor alone.
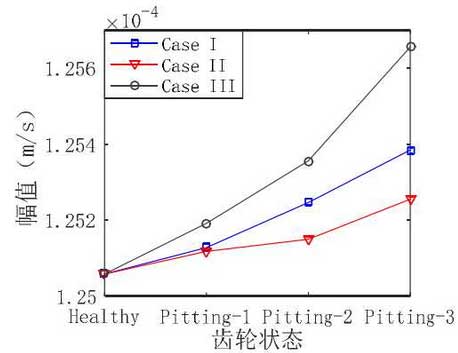
We also compare some statistical indexes of different pitting failure degrees in different simulation cases (case I, case II and case III). Figure 2 and figure 3 show the RMS value and peak peak value of vibration velocity signal respectively. It can be seen that the statistical index of gear dynamic response signal can clearly reflect the influence of different factors on the dynamic response when pitting occurs on the tooth surface. Through the analysis, it can be found that the RMS value and peak peak value of vibration speed signal increase almost linearly under different gear states of case I, case II and case III. When we compare the effects of meshing stiffness and sliding friction on the dynamic response, we can see that when there is a small pitting corrosion, the effect of only considering the sliding friction force (case II) is almost as large as that considering only the meshing stiffness (case I), especially for the RMS value. However, with the increase of pitting failure, the influence of time-varying meshing stiffness is gradually more than that of sliding friction.
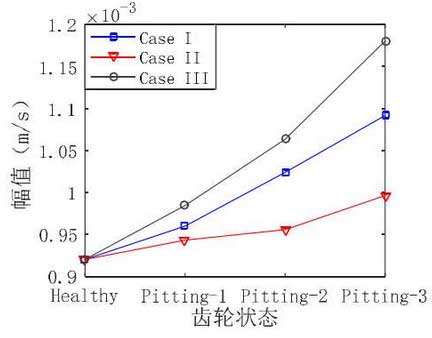
In this paper, the early micro pitting fault of gear is simulated. Firstly, the model of early micro pitting fault is established, and the influence of pitting fault on meshing stiffness and friction excitation of gear is studied. Then three simulation cases are passed: case I (only considering stiffness excitation), case II (considering only friction excitation) and case III (considering both stiffness excitation and friction excitation) respectively The influence of different gear states (health, pitting-1, pitting-2, pitting-3) on the dynamic response of gear system; finally, through the comprehensive analysis of the above simulation cases, it is concluded that the influence of only considering the sliding friction force is almost as large as that of considering only the meshing stiffness of the gear at the early stage of micro pitting. However, with the increase of pitting failure, the influence of time-varying meshing stiffness is gradually more than that of sliding friction.