Helical gears are the most widely used transmission device and play an important role in various transmission systems in fields such as automobiles, machine tools, and aviation. Due to the installation error of the axis and the influence of elastic deformation, the working condition of the helical gear deteriorates, resulting in vibration, noise, and even failure of the helical gear due to off load. Tooth alignment modification can reduce the impact of meshing in and out of helical gears, improve uneven load distribution, and thereby reduce vibration and noise. However, in the traditional grinding process of helical gears with tooth profile modification, there are fundamental machining errors on the tooth surface, resulting in distortion of the tooth surface. TIAN et al. analyzed the contact traces generated during the meshing process and found that the grinding amount of different contact traces corresponding to the same end section is different, and the tangential slope of the modification curve at the upper and lower surfaces of the helical gear is the highest, resulting in distortion phenomenon. When machining a modified helical gear with a formed grinding wheel, the radial feed rate of the grinding wheel is the highest at the meshing point, resulting in the maximum material removal at the tooth top and root of the upper and lower surfaces of the helical gear, and the modified tooth surface is twisted. Twisting errors can cause problems such as increased vibration and impact, resulting in poor meshing effect and increased noise during the transmission process of helical gears. Therefore, in order to improve the meshing performance of helical gears, it is necessary to analyze the mechanism of distortion error in tooth profile modification helical gears and its impact on contact mechanical properties.
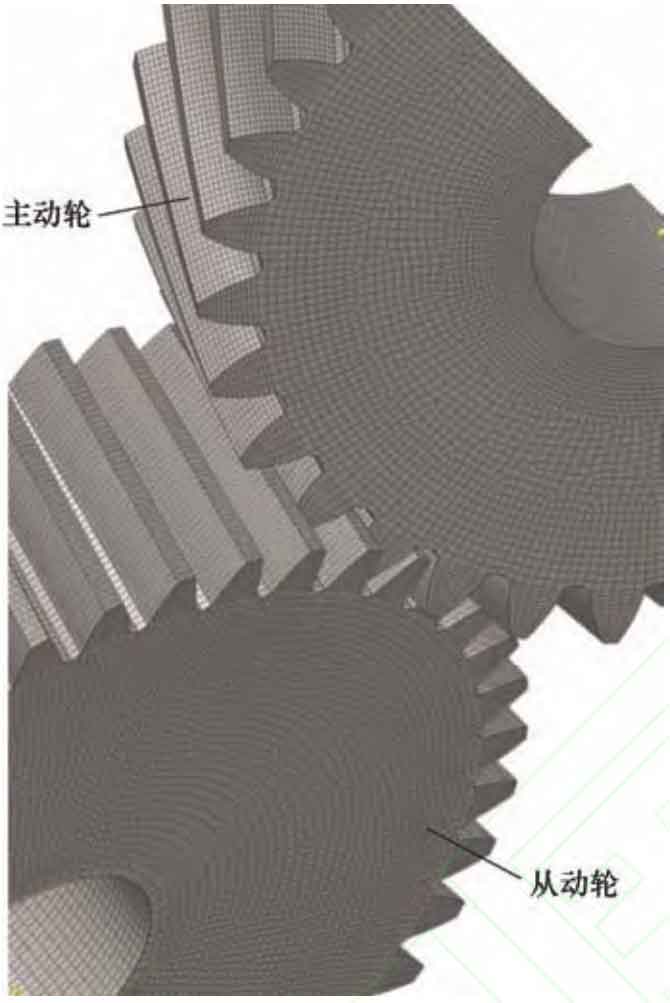
At present, domestic and foreign scholars have conducted a series of studies on the contact analysis of helical gears with tooth profile modification. LITVIN et al. established the meshing equation between the grinding wheel and the machined helical gear, and solved the contact trace through analytical methods. Fang Zongde applied Professor LITVIN’s helical gear meshing theory to propose a tooth contact analysis and computer simulation method for helical gears. Taking a pair of helical gear transmissions as an example, the meshing path, meshing marks, and transmission error of this pair of helical gears were calculated and obtained. Tang Jinyuan et al. established a contact analysis (TCA) model for drum teeth with installation errors, and analyzed and proved that this method can accurately predict the position of the contact trajectory by adjusting the modification parameters and installation errors. Lv Hongzhan et al. established a mathematical model for the drum shaped surface of modified straight teeth, and based on the TCA results, discretized the contact points on the tooth contact line to solve the distribution of tooth load. Zhou Yao et al. established a finite element meshing model of intersecting involute cylindrical and variable thickness helical gear pairs, and studied the influence of different modification methods and amounts on transmission errors and contact marks. On the basis of considering the actual meshing stiffness and static transmission error of helical gears, Chen Siyu et al. studied the influence of different modification amounts and lengths on the dynamic characteristics of helical gears.
In contrast, there is relatively little research on contact analysis of helical gears with distortion errors. For example, Gao Shihao et al. established a tooth surface distortion model based on diagonal worm gear grinding method, simulated and analyzed the meshing performance of helical gear pairs with different distortions, and obtained the influence of tooth surface distortion on meshing performance. HSU et al. proposed an improved variable pressure angle hob for diagonal feed to reduce tooth surface distortion during tooth profile modification, and studied the transmission errors of contact elliptical and helical gear pairs generated by traditional hobs and improved variable pressure angle hobs. TIAN et al. compared the maximum normal stress and contact stress of standard helical gears, tooth profile modified drum teeth, and drum teeth with twist errors, and found that twist errors increase the maximum normal stress and contact stress. The above literature has conducted research on the contact analysis of twisted tooth surfaces, but lacks mathematical equations for drum tooth surfaces containing distortion errors, and there is relatively little research on the influence of design parameters on the contact analysis of modified tooth surfaces. On the basis of the relevant literature mentioned above, analyze the influence of modification amount and helix angle on the distortion of modified helical gears, and further analyze the influence law of both on transmission error and contact ellipse.
Based on the mechanism of distortion error, the mathematical equation of tooth profile modification drum tooth surface containing distortion error is derived. The TCA model of the active wheel drum tooth with distortion error and the unmodified driven wheel is established. The influence of modification amount and helix angle on distortion amount, transmission error, and contact ellipse is studied, and the influence of helix angle and modification amount on contact stress of twisted tooth surface is verified through finite element analysis. The research results can provide theoretical support for the optimization design of tooth profile modification helical gears and help improve the meshing performance of helical gears.
(1) Based on the mechanism of distortion error in modified helical gears, the mathematical equation of the drum tooth surface containing distortion error was derived, and a TCA model of the drum tooth of the driving wheel containing distortion error was established.
(2) According to the calculation formula for distortion, the modification amount and helix angle are selected as the main design parameters. As the modification amount and helix angle increase, the distortion amount increases and the tooth surface distortion phenomenon becomes more severe.
(3) The increase in modification amount and helix angle leads to an increase in the amplitude of transmission error, and the amplitude changes dramatically during meshing in and out, resulting in unstable transmission, increased vibration and noise; The modification amount has little effect on the contact ellipse area, while increasing the helix angle reduces the length and short axis radius of the contact ellipse, reduces the contact ellipse area, and increases the contact stress on the tooth surface. The influence of helix angle and modification amount on tooth contact stress was verified through finite element analysis, which can be used to guide the optimization design of helical gears with tooth profile modification.