The wind power planetary helical gear transmission system is a key component in the wind power generation gearbox. Wind turbines are mainly distributed in extremely harsh environments such as coastal areas, grasslands, and Gobi. The planetary gear trains in the gearbox work year-round in low-speed and heavy-duty environments. The root of the helical gear is also a stress concentration area, which is prone to cracking, further leading to faults such as fractures.
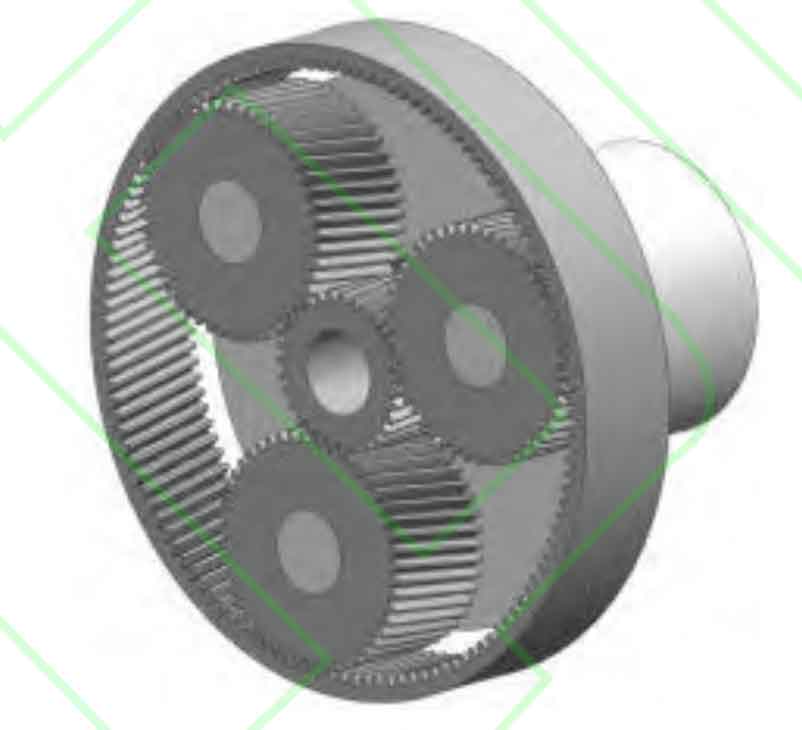
Many experts and scholars at home and abroad have done a lot of work on the relationship between helical gear crack failure and time-varying meshing stiffness. Yang et al. explored the method for solving time-varying meshing of helical gear pairs and solved it using the energy method; Chaari et al. investigated the relationship between cracks and the meshing stiffness of helical gear pairs, and solved the meshing stiffness of spur gear pairs when two types of cracks were generated using analytical methods; Feng et al. established a three-dimensional contact model for the generation of cracks in spiral bevel gears and studied the relationship between crack shape and time-varying meshing stiffness using finite element method; Wan et al. used the potential energy method to explore the relationship between cracks in helical gear pairs and time-varying meshing stiffness, and analyzed the impact on vibration, but the fitting of crack shape was too simple. Wan Zhiguo et al. used finite element simulation to analyze the propagation path of cracks and solved the relationship between the crack path and time-varying meshing stiffness using the potential energy method. Wu et al. analyzed and explored the causes of cracks in helical gear pairs, and established a multi degree of freedom model for cracked helical gears, which has important reference value for studying the mechanism of crack generation. Jia et al. established a three-dimensional model of through cracks in helical gears and proposed the use of time-frequency analysis to study the meshing characteristics of helical gears. The effectiveness of this method was verified through experiments.
Most of the research focuses on spur gears. Due to the existence of helical angle gears, the meshing method of helical gears is significantly different from that of spur gears, resulting in varying meshing stiffness. And the fitting of cracks is mostly based on simple straight lines, which differs greatly from the actual situation. There is less research on crack faults based on wind power helical gears. Based on the above problems, take the wind power planetary helical gear pair as the research object, establish a three-dimensional model, consider the root crack propagation in the depth direction and width direction, and fit it in the shape of a parabola. Through the cracked gear to simulate the time-varying motion state of the helical gear pair at different assembly angles, use the finite element method to obtain the average deformation of the sun gear root crack fault when meshing with the planetary gear, Calculate the time-varying meshing stiffness through the meshing stiffness solving formula. To provide reference for studying the motion characteristics of wind power helical gearbox when faults occur.