The low life of the bevel gear of automobile rear axle in China is always a big problem. There are two problems in heat treatment: one is the low hardness of the center, the other is the large distortion. The low core hardness is mostly to reduce the distortion, but it affects the contact fatigue and bending fatigue strength. When the contact line length changes from curve 5 to 2, the peak stress increases by more than 60% due to the large distortion and poor engagement. Therefore, the distortion of the rear axle bevel gear is not only the size accuracy, but also the strength problem.
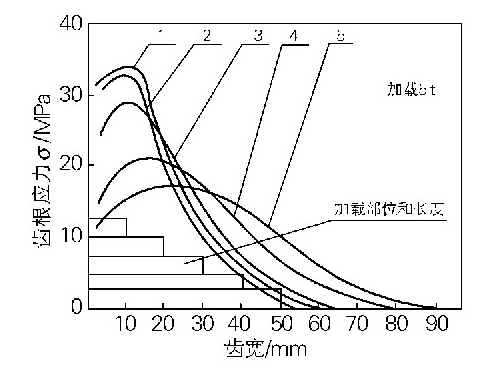
1. Press hardening of special structure gear
1) Technical concept
Because of the particularity of bevel gear structure, it is difficult to control the distortion by free quenching, but many domestic gear producers advocate free quenching in order to simplify the process, facilitate the operation and reduce the cost. Unfortunately, for decades, the distortion of bevel gears has been perplexing the gear industry in China. At the same time, the development of press quenching technology and equipment has also been greatly affected.
In fact, in the heat treatment production, for the bending distortion of workpieces such as small twist drills and slender bars, we all agree to use pressure straightening, so as to achieve stable mass production. As for the thin-walled large circular bevel gear and the gear sleeve of automobile synchronizer and other parts in the gear manufacturing, the press quenching can lose or reduce the influence of various potential distortion factors in the material, machining and heat treatment process in the production process under strong pressure, which in general costs much less than the free quenching, Press hardening should be an important and indispensable process.
2) Production application
The key of press hardening after carburizing of bevel gear is to control flatness and ovality of inner hole. The accuracy of quenching press, die and process parameters are the main factors affecting the distortion of bevel gear during press quenching. Table 12 is the main reason for the distortion out of tolerance during press quenching.
2. New press hardening technology
Recently, a mould pressing induction hardening process has been developed abroad for the quenching of special gears, especially bevel gears and synchronizer gear sleeves [22].
The advantages of induction quenching and mould pressing quenching are integrated in the mould pressing induction quenching of bevel gear. See Figure 29 for the induction quenching press. The press adopts four independent and controllable quenching circuits, which can greatly reduce the distortion and greatly reduce or cancel the subsequent processes. Inductor, up and down die pressing device and correction core die can be installed on standard induction hardening machine.
As the process is based on the carburized gear, there is no need to change the material, and the surface hardness and hardening layer depth remain the same. Therefore, the production equipment and process of the process are greatly simplified.
See Figure 30 for the layout of traditional carburizing press quenching production line and mould pressing induction quenching production line. It can be seen from the figure that the number of units in the die-casting induction quenching production line is reduced. Moreover, since the induction quenching adopts water-based coolant quenching, the gear after heat treatment does not need to be cleaned. The built-in inductor can not only be used for heating quenching, but also for heating tempered parts without additional equipment, so the production cost is greatly reduced.
Recently, a new idea is put forward in the process of bearing ring press quenching in foreign countries, which can be used for reference.