Because the coordinate system of milling cutter head is not the coordinate system of CNC machine tool, but also requires the angle parameters of the wheel blank to be cut, therefore, for NC programming and tool setting, it is necessary to find the relationship between the milling cutter head, the wheel blank to be cut and the coordinate system of CNC machine tool, and translate the coordinate system into the coordinate system xwowyw of CNC machine tool.
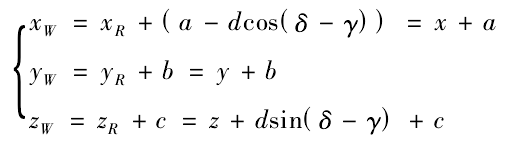
The figure shows the relationship between the position of the milling cutter head, the wheel blank to be cut and the coordinate system of the CNC machine tool. From the coordinate relationship in Fig. 6, a series of instantaneous position coordinates (XW, YW, ZW) of the milling cutter head can be obtained, which can be used to control the movement of the milling cutter head, and coordinate with the corresponding instantaneous shaft angle α (the difference between pitch angle δ and root cone angle γ) and the shaft rotation angle φ. The spiral tooth non bevel gear can be machined.